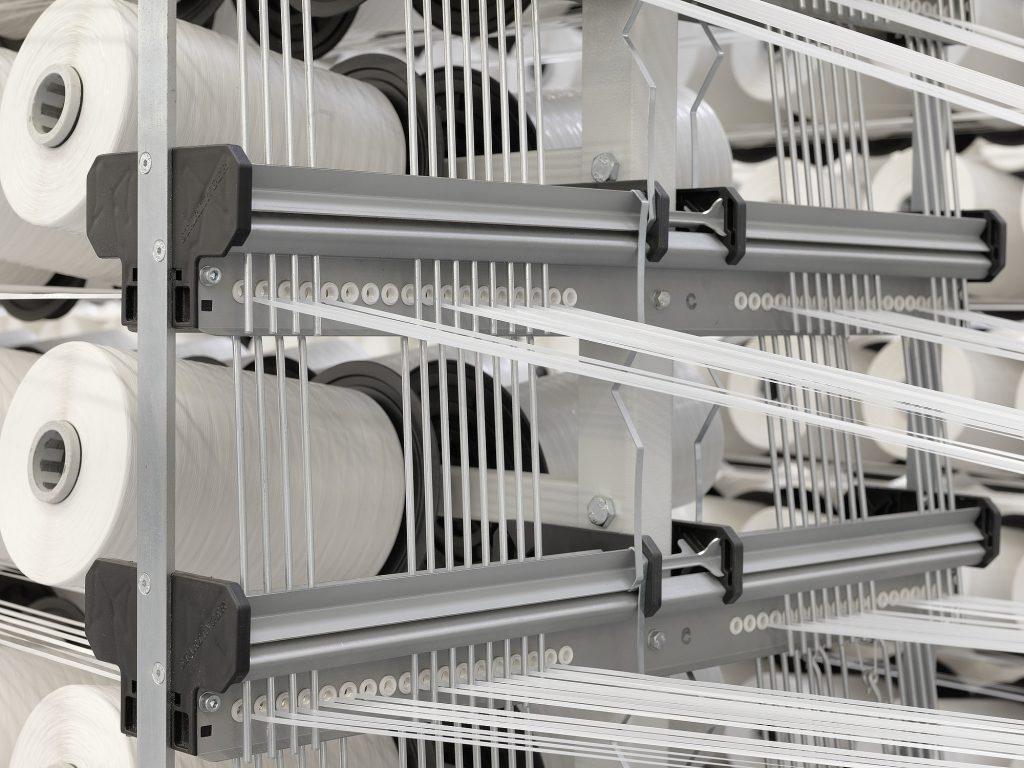
Introduction
In the fast-evolving construction materials industry, sewn open mouth bags have emerged as a critical packaging solution for their versatility in handling abrasive and moisture-sensitive products. These bags, characterized by their stitched top closures and customizable designs, are increasingly adopted for their ability to balance functionality with branding potential. For VidePak, a company with 30+ years of expertise and a fleet of Starlinger machinery, innovation in PP-based materials and advanced printing technologies has enabled it to dominate markets spanning cement, drywall compounds, and specialty chemicals. This report explores how VidePak’s sewn open mouth bags address industry challenges through material science, tailored designs, and strategic parameter selection.
Material Advantages: Why Polypropylene Dominates
Polypropylene (PP) remains the material of choice for sewn open mouth bags due to its unique blend of physical and chemical properties, critical for construction material packaging:
- Strength & Durability: PP fibers exhibit a tensile strength of 8–12 N/mm², enabling bags to withstand weights up to 50 kg without tearing—a necessity for cement and plaster packaging.
- Moisture Resistance: PP’s hydrophobic nature prevents water absorption, crucial for products like joint fillers that degrade upon exposure to humidity. VidePak enhances this with PE-coated liners, reducing moisture ingress by 90% compared to uncoated alternatives.
- Abrasion Resistance: The material’s molecular structure resists wear from rough handling during transport, as validated by a 2024 study in Packaging Technology and Science, which reported a 30% reduction in bag abrasion rates using PP over polyethylene.
Dialogue Example:
Q: “How does PP compare to traditional jute bags for cement packaging?”
A: “PP bags offer 3x higher tear resistance and 50% lighter weight, reducing shipping costs while ensuring product integrity in humid environments.”
Applications in Construction Materials
1. Cement & Plaster Powders
Cement’s abrasive nature demands bags with high burst strength (≥35 psi) and reinforced stitching. VidePak’s solutions include:
- Laminated PP Layers: Combining PP woven fabric with BOPP films to prevent powder leakage.
- Anti-Static Additives: Critical for preventing dust explosions in storage facilities.
Case Study: A partnership with a Vietnamese cement manufacturer saw a 25% reduction in transport damage after switching to VidePak’s 120 GSM laminated bags with double-stitched seams.
2. Joint Fillers & Drywall Compounds
These products require moisture-proof barriers to prevent clumping. VidePak integrates:
- Multi-Layer Designs: PP fabric + PE liner + kraft paper, achieving a water vapor transmission rate (WVTR) of <5 g/m²/day.
- UV-Resistant Inks: Custom color strips (e.g., red for fire-resistant fillers) printed with fade-resistant pigments for outdoor storage.
Selecting Optimal Parameters
Choosing the right bag specifications is pivotal for cost-efficiency and performance:
Parameter | Cement | Plaster Powder | Joint Fillers |
---|---|---|---|
Thickness (GSM) | 90–120 | 80–100 | 70–90 |
Outer Coating | BOPP Lamination | PE Coating | Kraft-PP Composite |
Inner Liner | PE Film | None | PE + Aluminum Foil |
Stitch Type | Double-Lock | Single-Lock | Double-Lock |
Technical Insight: A 2023 industry survey revealed that 68% of construction material suppliers prioritize GSM thickness and coating type as the top criteria for bag selection.
VidePak’s Customization Edge
With over 30 printing machines and 16 extrusion lines, VidePak offers:
- Multi-Color Branding: Up to 8-color CMYK printing for logos and safety warnings, critical for compliance in regulated markets.
- Smart Tagging: QR codes and RFID integration for inventory tracking, reducing warehouse sorting errors by 40%.
Example: A Chinese drywall manufacturer utilized VidePak’s QR-coded bags to automate stock management via SAP integration, cutting labor costs by 15%.
FAQs: Addressing Industry Concerns
Q1: How does bag thickness impact cost and performance?
A: Thicker bags (e.g., 120 GSM) offer higher durability but increase material costs by 20%. Balance based on product density and transport conditions.
Q2: Are recycled PP materials viable for heavy-duty applications?
A: VidePak’s “EcoShield” line uses 30% recycled PP with virgin granules in stress zones, maintaining strength while reducing carbon footprint.
Sustainability & Compliance
VidePak aligns with global ESG standards through:
- Recyclable Designs: 100% PP content ensures compatibility with circular economy initiatives.
- REACH & FDA Compliance: Critical for exporting to EU and North American markets.
Conclusion
Sewn open mouth bags are no longer mere containers but strategic assets in the construction supply chain. VidePak’s fusion of Starlinger precision, PP innovation, and customization expertise positions it as a pioneer in meeting the sector’s evolving demands. As automation and sustainability reshape packaging norms, the company’s commitment to R&D ensures it remains at the forefront of industrial solutions.
External Links: