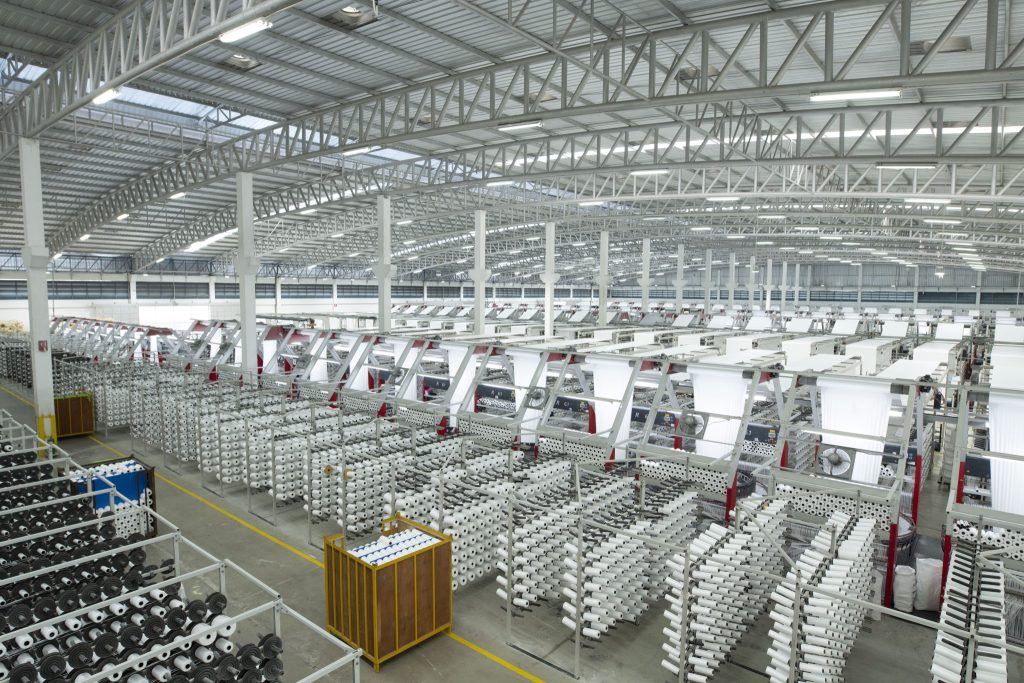
- 1. Introduction: The Dual Promise of Aesthetics and Durability
- 2. VidePak’s Quality Control Framework: Precision at Every Stage
- 3. Technological Edge: Starlinger and W&H Machinery
- 4. Customization and Market Adaptability
- 5. Future Innovations: Sustainability and Smart Packaging
- 6. Conclusion: Engineering Excellence for Global Demands
“Why are sewn open mouth bags increasingly favored for industries ranging from agriculture to construction?”
The answer lies in their adaptability to diverse product requirements, reinforced structural integrity, and VidePak’s industry-leading quality control systems that ensure compliance with global standards like ASTM and ISO. As a global leader in woven bag manufacturing, VidePak combines advanced Austrian Starlinger machinery with rigorous testing protocols to deliver bags that balance aesthetic customization and functional durability.
1. Introduction: The Dual Promise of Aesthetics and Durability
Sewn open mouth bags, characterized by their stitched closures and customizable designs, are critical for industries requiring both visual branding and robust material protection. From fertilizers to construction aggregates, these bags must withstand mechanical stress, environmental exposure, and logistical challenges. VidePak’s $80M annual revenue and global market presence reflect its ability to meet these demands through precision engineering and comprehensive quality assurance.
Key Insight:
“A bag’s strength isn’t just about threads—it’s about science. Our Starlinger systems and 16 extrusion lines ensure every gram of PP resin is optimized for performance.”
— Ray, CEO of VidePak
2. VidePak’s Quality Control Framework: Precision at Every Stage
VidePak’s 30+ years of expertise are embedded in its multi-layered quality assurance process, covering raw materials, production, and final product validation.
2.1 Material Testing: The Foundation of Reliability
- Virgin PP Resins: Sourced from certified suppliers, tested for melt flow index (MFI: 8–12 g/10 min) and ash content (<0.1%) to ensure consistency.
- Tape Production: Starlinger extruders maintain ±0.02mm thickness tolerance, reducing weak spots in woven fabrics.
2.2 Key Performance Tests
- Tensile Strength: ASTM D5034 tests validate tape tensile strength (>45 N/cm²) and elongation (>15%) using universal testing machines.
- Tear Resistance: Elmendorf tear testers (ASTM F1922) measure resistance to propagation, critical for abrasive materials like cement.
- Heat Seal Integrity: Seams are subjected to 0.5 bar pressure tests for 30 seconds to detect leaks.
- UV Resistance: Accelerated weathering tests (500 hrs at 85°C) ensure colorfastness and polymer stability.
Test Parameter | Standard | VidePak Benchmark |
---|---|---|
Tensile Strength | ASTM D5034 | >45 N/cm² |
Tear Resistance | ASTM F1922 | >12 N/mm |
Heat Seal Strength | ISO 13937-2 | >40 N/cm² |
UV Stability | ASTM D4329 | <5% strength loss |
Thickness Tolerance | ISO 4593 | ±0.03mm |
2.3 Secondary Quality Metrics
- Color Consistency: Spectrophotometers ensure ΔE <1.5 for brand uniformity.
- Edge Smoothness: Laser scanners detect burrs (>0.1mm) to prevent fiber shedding.
- Grammage Verification: Samples are weighed (±2g/m² tolerance) to optimize material usage.
3. Technological Edge: Starlinger and W&H Machinery
VidePak’s production leverages:
- Extrusion Lines: 16 W&H lines with closed-loop temperature control (200–250°C) to prevent polymer degradation.
- Circular Looms: 100+ Starlinger looms weaving 12×12 strands/inch for heavy-duty applications.
- Printing Systems: 30 machines offering 20+ Pantone colors and UV-resistant inks.
Case Study: A Southeast Asian rice exporter reduced spillage by 25% using VidePak’s PE-coated bags, validated by third-party lab tests.
4. Customization and Market Adaptability
VidePak’s bags cater to niche demands:
- Agriculture: Breathable weaves (8×8 strands/inch) for seed storage.
- Chemicals: Anti-static linings to prevent dust explosions.
- Retail: High-definition prints with QR codes for traceability.
FAQs:
- How do I choose between sewn and heat-sealed bags?
Sewn bags offer higher seam strength (40 N/cm² vs. 30 N/cm²), ideal for sharp-edged materials. - Are VidePak’s bags recyclable?
Yes—100% PP construction allows full recycling per EPBP guidelines.
5. Future Innovations: Sustainability and Smart Packaging
- Bio-PP Blends: Trials with 30% plant-based resins aim to reduce carbon footprint by 2030.
- IoT Integration: RFID tags for real-time humidity monitoring, piloted with EU pharmaceutical clients.
For deeper insights into sustainable practices, explore our guides on advanced PP recycling systems and high-speed production techniques.
6. Conclusion: Engineering Excellence for Global Demands
Sewn open mouth bags exemplify how form and function can coexist in industrial packaging. By integrating cutting-edge technology, rigorous testing, and ESG-driven innovation, VidePak not only meets but redefines market expectations.
Final Perspective:
“In packaging, every stitch tells a story of precision. VidePak’s commitment to quality ensures that story ends with reliability.”
— Journal of Industrial Materials, 2025