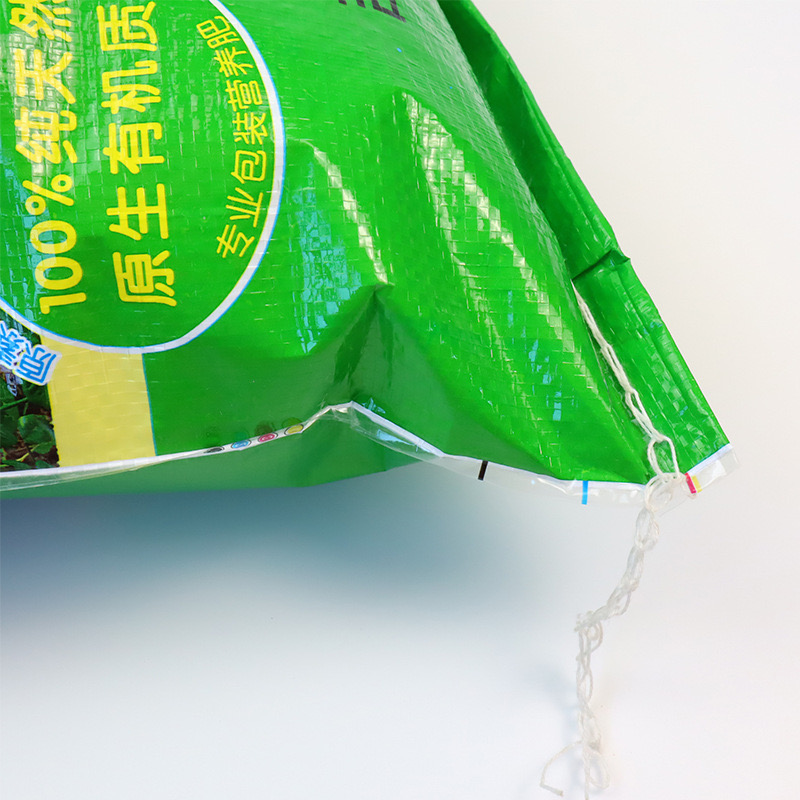
Introduction
In the packaging industry, Sewn Open Mouth PP Bags (also known as Sewn Open Mouth sacks or SOM Bags) are widely used for storing and transporting various products, especially in the agricultural, chemical, and industrial sectors. These bags offer numerous benefits, including durability, high load-bearing capacity, and flexibility in design. The manufacturing process and sewing techniques play a crucial role in enhancing the quality and functionality of these bags. In this article, we will explore the various factors influencing the choice of bag-making and sewing processes, focusing on aspects such as bottom seam types, sealing methods, thread material selection, and bag mouth designs.
Understanding Sewn Open Mouth PP Bags
Sewn Open Mouth Bags are woven polypropylene bags designed for open-mouth closure. They are ideal for applications requiring easy filling and closing without the need for complex sealing mechanisms. These bags are typically used for bulk products like grains, animal feed, and chemicals.
The basic structure of Sewn Open Mouth Bags includes the main woven body of polypropylene fabric, with the top mouth left open to facilitate easy filling. The opening is then sealed or sewn closed using various methods, depending on the application requirements.
Types of Seams and Their Importance
The bottom seam and how the mouth is closed are fundamental to the structural integrity and usability of Open Mouth Bags. There are several ways to close the bottom and mouth of these bags, each with its unique characteristics and advantages.
1. Bottom Seams: Block Bottom vs. Gusseted Bottom
- Block Bottom Bags are a popular choice for Sewn Open Mouth sacks. These bags have a flat, square bottom that offers superior stability when stacked. The flat base design is ideal for products that need to stand upright, such as agricultural grains or powdered chemicals.
- Gusseted Bottom Bags feature a pleated or folded bottom, which expands when the bag is filled. This design allows the bag to carry a larger volume of product while maintaining a compact form when empty.
Both of these bottom seam types require careful stitching to ensure load-bearing strength. The choice between a block bottom and a gusseted bottom depends on the specific needs of the product being packaged. For example, Block Bottom Bags are ideal for heavy-duty products that need a strong foundation, while Bottom Open Mouth Bags with gusseted seams work well for more flexible or lightweight contents.
2. Heat Sealing vs. Ultrasonic Welding
In addition to traditional sewing methods, modern technologies such as heat sealing and ultrasonic welding are increasingly used in the production of Sewn Open Mouth Bags.
- Heat Sealing involves applying high temperatures to the polypropylene material to melt and bond the edges together. This technique provides a strong, water-tight seal that enhances the bag’s durability.
- Ultrasonic Welding uses high-frequency sound waves to melt the material and bond it at the seams. This method is more energy-efficient and offers a cleaner, more precise seam than traditional heat sealing.
Each method has its advantages. Heat sealing is widely used for sealing bags that contain fine powders or liquids, while ultrasonic welding is more suitable for high-speed production environments, providing strong seams without the need for additional sewing threads.
3. Thread Material and Density
The choice of sewing thread material and the density of stitching are essential for ensuring the bag’s load-bearing capacity. Polypropylene threads are commonly used due to their excellent resistance to wear and tear, UV degradation, and moisture. For heavy-duty applications, nylon threads or polyester threads might be used to provide added strength and durability.
The stitch density refers to how closely the stitches are placed in the fabric. A higher stitch density results in a stronger seam that can better withstand the pressures of heavy loads. For example, a Sewn Open Mouth PP Bag designed to carry heavy products like cement may require a higher stitch density compared to one intended for lightweight materials like grains.
Various Bag Mouth Designs and Their Applications
The mouth design of a bag is crucial for both the filling process and the sealing method. Here are several types of bag mouth designs:
- Open Mouth Bags: As the name suggests, Open Mouth Bags have an open top, which makes them ideal for applications where quick filling is required. The open mouth can be sealed using stitching or heat sealing. These bags are commonly used in agriculture and bulk materials transport.
- Valved Open Mouth Bags: This design incorporates a valve at the mouth of the bag, allowing for automated filling while reducing spillage. The valve also helps in preventing air from escaping during storage, which is particularly useful for products sensitive to moisture.
- Heat-Sealed Open Mouth Bags: Heat-Sealed bags feature a heat-sealed closure at the mouth of the bag, providing a secure and airtight seal without the need for stitching. This method is often used for bags containing fine powders or other products that must remain secure during transit.
- Sewn Open Mouth Bags with Taped Mouth: A variation of the basic Sewn Open Mouth Bags, this design includes a reinforced tape along the mouth to provide additional sealing strength. These bags are often used for products that need a strong closure to prevent leakage or contamination.
Expert Insights: Choosing the Right Manufacturing Technique
Q: What are the main considerations when selecting a manufacturing technique for Sewn Open Mouth PP Bags?
A: The key factors include the type of product being packaged, the required bag strength, environmental conditions, and filling speed. For example, if you are packaging heavy industrial materials such as cement or sand, a Block Bottom Bag with high stitch density and nylon thread would be ideal. On the other hand, for lighter materials like grains, gusseted bags with polypropylene thread may suffice.
Key Factors for Choosing the Right Process:
Factor | Heat Sealing | Ultrasonic Welding | Sewing |
---|---|---|---|
Speed | Moderate | High | Low |
Durability | High | High | Moderate |
Cost Efficiency | Moderate | High | Low |
Energy Consumption | Moderate | Low | High |
FAQs on Sewn Open Mouth Bags
Q1: Can Sewn Open Mouth Bags be used for food packaging?
A1: Yes, Sewn Open Mouth Bags are widely used in food packaging, especially in applications requiring large quantities, such as grains, sugar, and animal feed. However, it is essential to ensure that the bags are made from food-grade materials and comply with regulatory standards for food safety.
Q2: How do I select the right thread for sewing these bags?
A2: For light-duty bags, polypropylene thread is sufficient. However, for heavy-duty applications, consider nylon or polyester thread, which offers greater strength and durability.
Conclusion
In conclusion, Sewn Open Mouth PP Bags are an essential solution for packaging bulk products across various industries. The selection of the right bag-making process, bottom seam design, and sewing technique plays a pivotal role in ensuring the functionality, durability, and cost-effectiveness of these bags. By understanding the nuances of different manufacturing techniques and bag mouth designs, companies can optimize their packaging processes to meet the specific needs of their products and customers.
For more detailed insights, explore our articles on the versatility of Open Mouth Bags in different industries and the evolution and benefits of Sewn Open Mouth PP Bags.