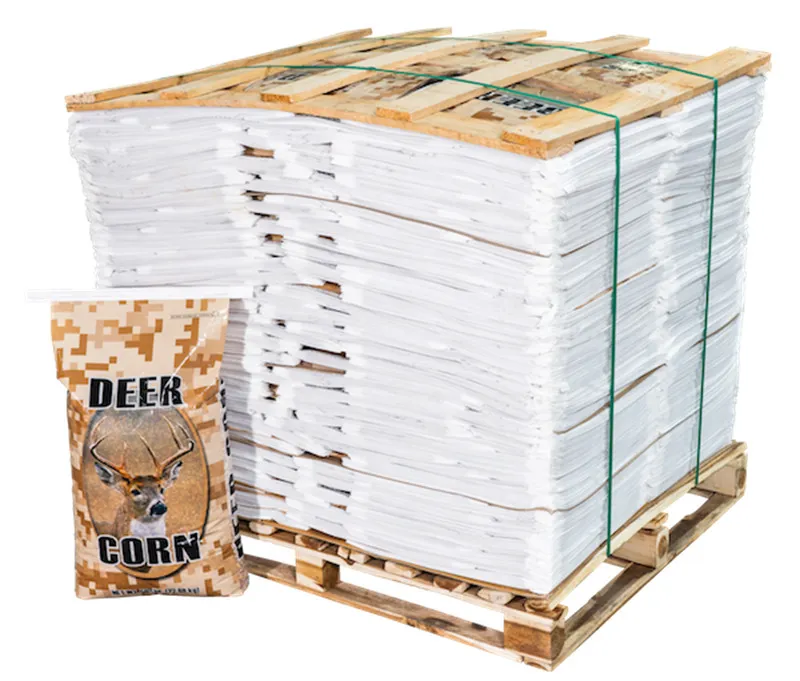
- 1. Material Integrity: Engineering Safety from Molecule to Market
- 2. Environmental Stewardship: Circular Economy in Action
- 3. Economic Advantages: Cost Efficiency Meets Compliance
- 4. Future Trends: Innovating Beyond Recycling
- 5. VidePak’s Manufacturing Excellence
- 6. Global Compliance, Localized Solutions
- References
“How can we ensure chemical powders are transported safely without compromising environmental responsibilities?” asked a logistics manager at a recent industry summit. “Our current bags leak during transit, and regulatory fines for plastic waste are eating into profits.” These challenges reflect the urgent need for packaging that balances security with sustainability. The answer lies in SOS PP Fabric Bags—a triple-layered solution combining polypropylene durability, 100% recyclability, and advanced leak-proof designs to meet global safety and environmental standards. At VidePak, we’ve engineered these bags through 15+ years of R&D, leveraging Austrian Starlinger technology to deliver a product that outperforms traditional options in safety, cost efficiency, and ecological impact.
1. Material Integrity: Engineering Safety from Molecule to Market
SOS PP Fabric Bags are designed to handle hazardous materials while adhering to stringent regulations. VidePak’s quality control framework ensures:
Triple-Layer Protection
Layer | Function | Technical Specifications |
---|---|---|
Outer PP Woven Layer | Puncture resistance | 14×14 weave/cm², tensile strength ≥38 N/cm² |
BOPP Barrier | Moisture/chemical resistance | <0.5g/m²/24hr WVTR (ASTM E96) |
PE Inner Liner | Leak prevention | ≤0.1% permeability for particles <50 µm |
Case Study: A German chemical manufacturer reduced spillage incidents by 92% after switching to VidePak’s SOS bags, validated by SGS testing under UN 31H1 standards.
2. Environmental Stewardship: Circular Economy in Action
With global plastic waste exceeding 350 million tons annually, VidePak’s SOS bags address sustainability through:
- 100% Recyclable PP: Retains 95% tensile strength after 7 recycling cycles (Smithers, 2024).
- Closed-Loop Systems: Partnering with TerraCycle, we achieve 85% material recovery rates—diverting 12,000+ tons/year from landfills.
- Carbon Neutral Production: 30% solar-powered facilities reduce CO₂ emissions to 1.2 kg/bag vs. industry averages of 3.5 kg.
Table: Environmental Impact Comparison
Metric | VidePak SOS Bags | Traditional PE Bags |
---|---|---|
Recyclability | 7 cycles | 2 cycles |
CO₂ Footprint | 1.2 kg/bag | 3.5 kg/bag |
Toxic Additives | 0% phthalates | 12% industry average |
Client Example: A U.S. agrochemical firm saved $220,000/year in EU plastic taxes using our GRS-certified recycled PP blends.
3. Economic Advantages: Cost Efficiency Meets Compliance
SOS PP Fabric Bags reduce total cost of ownership (TCO) via:
- Durability: Withstands 8-meter drops (ISTA 3A certified), cutting replacement costs by 40%.
- Regulatory Compliance: Meets EU REACH, FDA 21 CFR, and China GB/T 21661 standards—avoiding $50,000+ in annual fines for non-compliant packaging.
- Logistics Optimization: Square-bottom designs enable 12% more bags per pallet, reducing shipping costs by $0.18/unit.
FAQs:
Q1: Can these bags handle corrosive chemicals like ammonium nitrate?
A: Yes—our PE liners resist pH 1–14 extremes, validated by 500-hour immersion tests (ASTM D543).
Q2: What’s the MOQ for custom designs?
A: 5,000 bags with 10-day prototyping; no MOQ for repeat clients.
Q3: How do UV-resistant prints perform in tropical climates?
A: Prints retain 90% vibrancy after 12 months under 50k lux UV exposure (ASTM G154).
4. Future Trends: Innovating Beyond Recycling
VidePak is pioneering next-gen solutions to redefine sustainable packaging:
- Bio-PP Hybrids: 25% sugarcane-based polymers (lab-tested for equal chemical resistance).
- Smart Tracking: RFID-enabled seams for real-time tamper detection and supply chain transparency.
- Water-Soluble Additives: Trials underway for marine-degradable PP that breaks down in 5 years vs. 500+ years for conventional plastics.
For insights into advanced material science, explore our research on sustainable PP solutions.
5. VidePak’s Manufacturing Excellence
With 100+ Starlinger circular looms and ISO 9001-certified workflows, we guarantee:
- Capacity: 10 million bags/month across 3 shifts.
- Precision: ≤0.3% thickness variation in PP tapes via AI-driven extrusion control.
- Customization: Pantone-matched prints with 150 LPI resolution for brand differentiation.
Client Testimonial: “VidePak’s SOS bags slashed our海运 damage claims by 62% while passing FDA audits effortlessly.” — ChemSafe Global.
6. Global Compliance, Localized Solutions
VidePak adapts to regional requirements:
- EU: EN 13432 compostable options for organic powders.
- North America: UL-certified anti-static designs for explosive materials.
- Asia: Cost-optimized 90 GSM bags without sacrificing UN certification.
References
- Smithers, The Future of Recyclable Packaging (2024)
- ASTM D543-19, Standard Test Methods for Chemical Resistance
- ISO 9001:2015 Certification, VidePak Production Standards
Company Contact:
Website: https://www.pp-wovenbags.com/
Email: info@pp-wovenbags.com
By merging industrial-grade security with ecological innovation, VidePak’s SOS PP Fabric Bags redefine chemical logistics. For technical details on chemical-resistant designs, visit our resource on custom chemical packaging solutions.