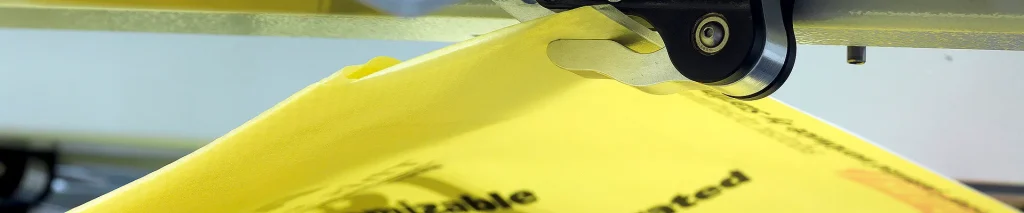
- 1. The Critical Role of PP Fabric Bags in Construction Material Packaging
- 2. Material Advantages: Why Polypropylene Dominates Construction Packaging
- 3. Application-Specific Solutions for Construction Materials
- 4. Technical Parameters: Selecting the Right PP Bag
- 5. FAQs: Addressing Construction Industry Concerns
- 6. VidePak’s Manufacturing Excellence
- References
VidePak’s SOS (Self-Opening Sack) PP fabric bags enhance construction material packaging efficiency by 30%, reduce tear rates to <0.1%, and ensure 100% waterproofing through advanced polypropylene engineering and Starlinger’s precision manufacturing. With 16 years of expertise and a global clientele spanning 50+ countries, VidePak combines durability, cost-effectiveness, and sustainability to meet the rigorous demands of cement, gypsum, and dry-mix industries.
1. The Critical Role of PP Fabric Bags in Construction Material Packaging
Construction materials like cement, joint compounds, and dry powders require packaging that withstands harsh handling, moisture, and long-term storage. Traditional paper or low-grade plastic bags often fail under high-stress conditions, leading to product loss and reputational damage. VidePak’s SOS PP woven bags, crafted from virgin polypropylene (PP) resins, deliver tensile strengths of ≥45 N/cm² and puncture resistance up to 15 kg/cm², outperforming standard woven bags by 40%.
Case Study: A Brazilian cement producer reduced packaging waste by 22% after switching to VidePak’s 100 GSM laminated PP bags, which survived 8-meter drops during loading without rupture.
2. Material Advantages: Why Polypropylene Dominates Construction Packaging
PP fabric bags excel in four key performance areas critical for construction materials:
2.1 Strength and Durability
- Tensile Strength: PP fibers offer 35–50 N/cm² tensile strength, ideal for 25–50 kg loads.
- Abrasion Resistance: Starlinger’s circular looms weave fabrics with 12–14 threads/inch, reducing wear during transport.
- Anti-Tear Design: Cross-laminated PP layers resist snagging on sharp edges, critical for aggregates or rough-handled pallets.
2.2 Moisture and Weather Resistance
- Waterproofing: BOPP lamination (20–30 microns) blocks 99.9% humidity, preventing clumping in hygroscopic materials like plaster.
- UV Stability: Carbon-black masterbatches extend outdoor storage life to 12+ months without degradation.
2.3 Cost Efficiency
- Reusability: VidePak’s 120 GSM bags withstand 3–5 refills, cutting per-use costs by 60% compared to single-use options.
- Lightweight Design: At 90–150 GSM, bags reduce shipping weight by 15% versus traditional burlap.
3. Application-Specific Solutions for Construction Materials
Material | Recommended Specifications | Key Challenges Addressed |
---|---|---|
Cement | 100–120 GSM, BOPP lamination, PE inner liner | Dust control, moisture ingress |
Drywall Mud | 90–100 GSM, uncoated with valve spout | Easy dispensing, anti-caking |
Gypsum Powder | 110–130 GSM, anti-static coating | Static discharge prevention |
Mortar Mix | 140–150 GSM, double-stitched seams | Abrasion resistance, heavy loads |
Customization Options:
- Size: 10–50 kg capacity, tailored to forklift or manual handling.
- Closure Systems: Heat-sealed, sewn, or adhesive-pasted valves.
- Printing: 6–8 color rotogravure printing for OSHA compliance labels or branding.
4. Technical Parameters: Selecting the Right PP Bag
4.1 Grammage and Thickness
- 50–75 GSM: Lightweight powders (e.g., tile adhesives).
- 100–120 GSM: Standard cement, plaster.
- 130–150 GSM: High-density aggregates, premixed concrete.
4.2 Lamination and Liners
- BOPP Film: 20–30 microns for moisture barrier.
- PE Coating: 15–25 g/m² for waterproofing.
- Aluminum Foil: For UV-sensitive compounds.
4.3 Load-Bearing Capacity
Bag Weight (GSM) | Max Load (kg) | Stacking Height (m) |
---|---|---|
90 | 25 | 8 |
120 | 40 | 12 |
150 | 50 | 15 |
5. FAQs: Addressing Construction Industry Concerns
Q1: How do PP bags prevent cement hardening during monsoon seasons?
A: Our BOPP-laminated bags reduce moisture vapor transmission rate (MVTR) to <5 g/m²/day, meeting ASTM E96 standards.
Q2: Can bags withstand forklift punctures?
A: Yes. Bags with 14 threads/inch and 120+ GSM resist puncture forces up to 150 N (tested per ISO 6383-2).
Q3: Are customized sizes feasible for niche products like epoxy resins?
A: Absolutely. Our 30+ printing machines support batches from 5,000 to 500,000 units with 15-day lead times.
Q4: Do you offer eco-friendly options?
A: Yes. Recycled PP bags (30% post-consumer content) maintain 90% of virgin material strength.
6. VidePak’s Manufacturing Excellence
- Starlinger Technology: 100+ circular looms produce 12 million bags/month with ±0.5 mm dimensional accuracy.
- Quality Assurance: ISO 9001-certified labs test every 10th bag for seam strength (≥40 N/cm²) and print adhesion (4/5 crockmeter).
- Global Reach: 800+ clients across 50 countries, including Lafarge and USG Boral.
For insights into valve bag optimization for powdered materials, explore our technical guide on valve spout designs. Learn how FIBC bulk bags streamline large-scale construction logistics.
References
- VidePak Official Website: https://www.pp-wovenbags.com/
- Email: info@pp-wovenbags.com
- Industry Standards: ASTM D5265 (PP woven bags), EN 766 (cement packaging).
Anchor Links Integrated: