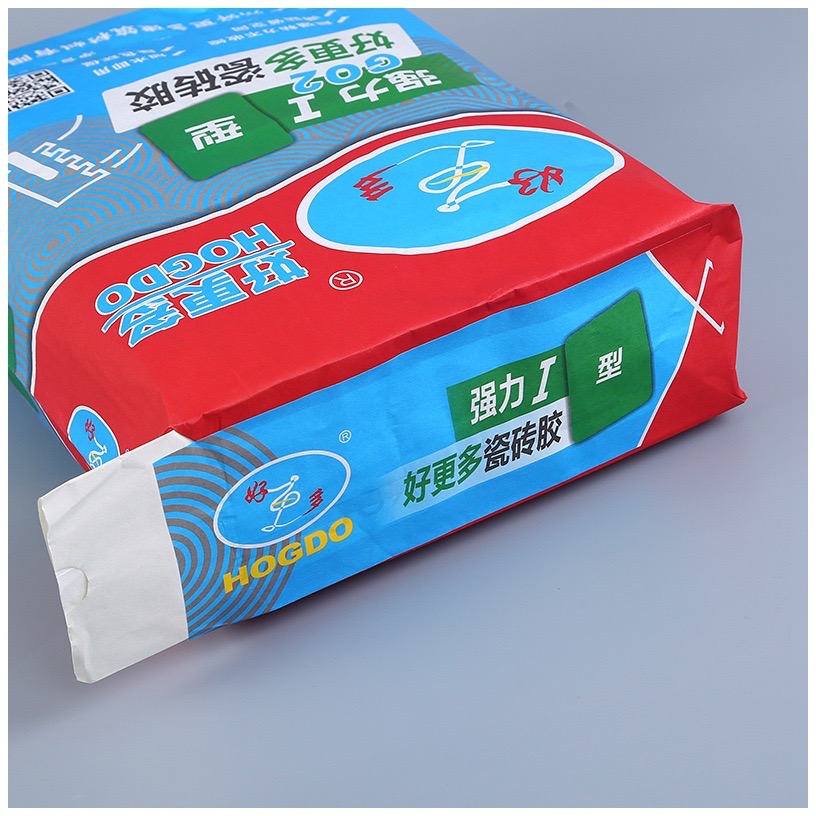
Square Bottom PP Valve Bags, also known as Square Bottom Valve sacks or Square Bottom Woven Bags, are highly efficient packaging solutions tailored for industries requiring strong, durable, and versatile sacks. The unique square-bottom structure allows these bags to maintain a stable, upright position, which optimizes stacking and storage efficiency. Beyond the practical design, choosing the right materials for these bags is essential, as various materials like PP, HDPE, PE, and aluminum foil each bring unique properties that impact performance. In this article, we will explore the features of Square Bottom PP Valve Bags and delve into the specifics of material selection, evaluating the benefits of each material in terms of functionality, durability, and suitability for different applications.
Key Features of Square Bottom PP Valve Bags
Square Bottom PP Valve Bags, often referred to as Valve Bags or Square Bottom PP Bags, are popular for their ability to offer both strength and flexibility. These bags are designed to withstand heavy loads, ideal for packaging products like cement, chemicals, agricultural products, and construction materials. Here are the main features that make them stand out:
- Self-Standing Structure: The square bottom design allows the bag to stand upright, ensuring stability and enabling easy stacking, which enhances storage and transportation efficiency.
- Automatic Sealing Valve: These bags feature a valve at the top, which can be quickly sealed after filling, reducing the need for additional sealing equipment and thus saving time and labor.
- High Load Capacity: Square Bottom Valve Bags are crafted from high-quality woven polypropylene, which provides excellent load-bearing strength without compromising flexibility.
- Moisture and UV Resistance: Many Square Bottom Valve sacks are laminated or coated to offer resistance to moisture and UV rays, protecting the contents from environmental factors.
Square Bottom PP Valve Bags also support custom designs, allowing manufacturers to tailor bag specifications like size, color, and printing to meet specific branding or functional needs.
Material Options for Square Bottom Valve Bags
The choice of material is a critical consideration in designing Square Bottom Valve Bags, as it directly influences durability, flexibility, and protection capabilities. Below, we discuss the common materials used in these bags, including their characteristics and applications in woven bag manufacturing.
Material | Properties | Applications |
---|---|---|
Polypropylene (PP) | Lightweight, durable, excellent tensile strength, resistant to chemicals and moisture | Suitable for various industrial uses, such as fertilizers, grains, and chemicals |
High-Density Polyethylene (HDPE) | Strong, rigid, impact-resistant, and highly resistant to chemicals | Often used for packaging heavy goods and providing added structural strength |
Polyethylene (PE) | Flexible, moisture-resistant, adaptable for coatings or liners to enhance waterproofing | Commonly used as an inner layer or liner in bags for food products or moisture-sensitive goods |
Aluminum Foil | Provides a superior barrier to moisture, light, and gases, highly durable | Used in applications requiring airtight protection, such as food or pharmaceutical products |
Each material brings specific advantages, from added durability to enhanced moisture resistance, making them suitable for various types of Square Bottom Valve sacks. The next section examines each material in more detail.
In-Depth Analysis of Bag Materials: PP, HDPE, PE, and Aluminum Foil
- Polypropylene (PP) Polypropylene is one of the most common materials used in Square Bottom PP Bags. Its strength-to-weight ratio is exceptional, providing durability without adding significant weight. Additionally, PP is resistant to various chemicals and moisture, making it ideal for packaging products that require a robust, durable bag. PP bags can withstand rough handling and heavy loads, which makes them perfect for bulk items like fertilizers, grains, and industrial chemicals. Another advantage of PP is its flexibility, allowing it to be woven into fabrics that retain durability while offering some stretch. This balance of rigidity and pliability is key in applications where a high load capacity is required.
- High-Density Polyethylene (HDPE) High-Density Polyethylene (HDPE) is renowned for its rigid structure and impact resistance. HDPE has a denser molecular structure than PP, which provides additional strength and chemical resistance, beneficial for applications that demand enhanced durability. Square Bottom Valve sacks constructed from HDPE offer exceptional load-bearing capacity, making them a preferred choice in industries handling heavy products, like building materials or large quantities of agricultural produce. However, HDPE lacks some of the flexibility of PP, which may limit its use in applications that require a softer, more pliable bag structure. Despite this, HDPE remains a top choice when extra structural integrity is necessary.
- Polyethylene (PE) Polyethylene, especially in its low-density forms, is commonly used as a coating or liner in Valve PP Bags. Its natural resistance to moisture makes it a preferred choice for bags that require waterproofing. PE layers are often laminated onto woven PP bags, providing a barrier against moisture and preventing the contents from being affected by humidity. This layer also enhances the bag’s suitability for food-grade applications, as PE is non-toxic and suitable for packaging consumable goods. For example, when combined with a PP base, PE provides both strength and waterproofing, creating a multi-layer bag that ensures product integrity.
- Aluminum Foil Aluminum foil is an advanced material used when absolute protection from moisture, gases, and light is necessary. This material is typically laminated onto the inner surface of the Square Bottom Woven Bags to provide a complete barrier, making it ideal for products requiring a high degree of protection, such as pharmaceuticals or certain chemicals. While aluminum foil offers unparalleled barrier properties, it also adds weight and cost, making it less commonly used in general applications. However, for highly sensitive or perishable contents, it is an excellent choice.
Why Material Selection Matters for Valve Bags
The choice of material for Square Bottom Woven Bags can significantly affect the performance and cost-effectiveness of the final product. Factors such as tensile strength, chemical resistance, flexibility, and environmental conditions should all be considered in material selection. Moreover, the application itself—whether for industrial, agricultural, or food-grade use—often dictates the most suitable material composition.
Here’s a closer look at how materials influence the functionality and longevity of Square Bottom Valve Bags:
- Load-Bearing Capacity: For heavy-duty applications, HDPE or reinforced PP are preferred due to their high tensile strength, which ensures bags remain intact under substantial loads.
- Moisture and Chemical Resistance: In environments where bags are exposed to moisture or chemicals, PP with a PE coating or laminated layers offers the best protection.
- Flexibility and Stackability: Materials like PP provide the flexibility needed for easy handling and stacking, critical for optimizing storage space.
- Barrier Properties: For products requiring complete protection from light and moisture, laminated bags with aluminum foil offer a solution that guarantees freshness and quality.
Final Thoughts: Choosing the Right Square Bottom PP Bag
Square Bottom PP Valve Bags are versatile, strong, and customizable packaging options that serve a broad spectrum of industries. The unique design enhances stability and efficiency in handling, while the selection of materials like PP, HDPE, PE, and aluminum foil allows manufacturers to tailor the bags to specific needs. By understanding the properties of each material, businesses can choose bags that deliver the required durability, protection, and functionality, ensuring that products are well-protected from production to delivery.
As Square Bottom Valve sacks evolve with innovations in material technology, their application potential will only broaden, making them a go-to solution in various packaging sectors. With the right material choices, these bags can provide a robust, adaptable packaging solution that meets the demands of modern industry.