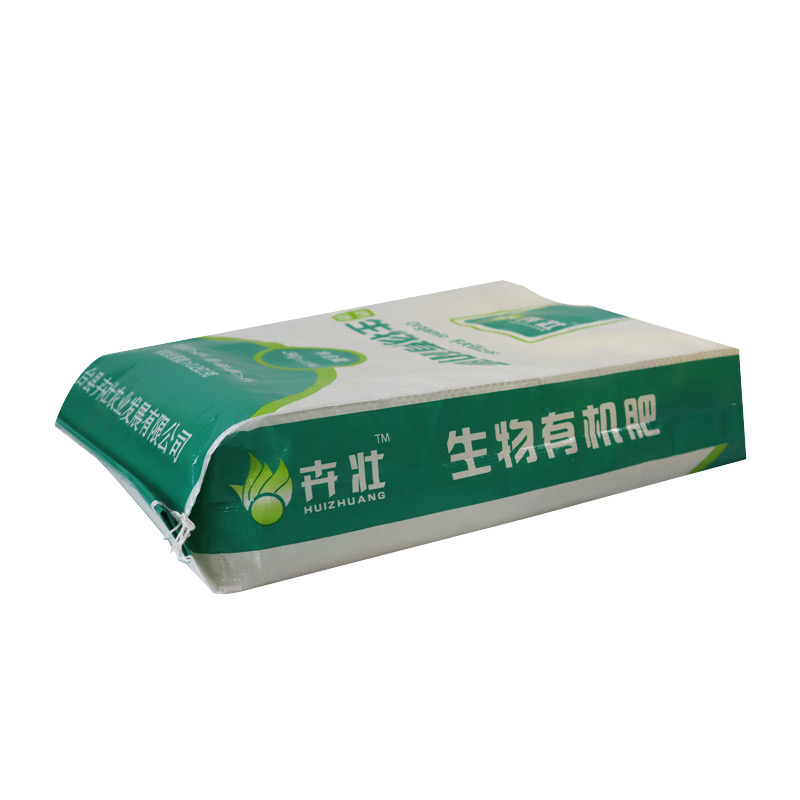
- Why Choose Printed BOPP Woven Bags?
- Ensuring Safety and Integrity in Chemical Powder Packaging
- Technical Advantages of Printed Woven Bags for Chemical Materials
- Comparative Analysis: Features of Printed BOPP Woven Bags
- Applications in Chemical Powder Packaging
- Customization Options to Meet Industry Needs
- Innovations in Preventing Leakage and Contamination
- Conclusion
Printed BOPP Woven Bags are an essential component in modern industrial packaging. Their versatility, durability, and ability to handle custom printing make them the ideal choice for storing and transporting a wide range of products, including chemical powder materials. These materials, such as titanium dioxide, color pigments, calcium titanate, silica powder, latex powder, sodium carbonate, and zinc sulfate, require specialized packaging to prevent leakage and contamination.
For detailed information on advanced manufacturing techniques, explore the craftsmanship behind Printed BOPP Woven Bags. Additionally, for insight into premium solutions tailored to diverse market needs, visit BOPP Woven Bags.
Why Choose Printed BOPP Woven Bags?
The increasing demand for high-quality packaging has positioned Printed BOPP Woven Bags as a leading solution. These bags offer several key benefits:
- Customizable Designs: Vibrant multi-color printing supports brand recognition.
- Durability: High tensile strength ensures resistance to tears and punctures.
- Moisture Resistance: Lamination provides excellent protection against moisture.
- Eco-Friendliness: They are recyclable and can be manufactured from sustainable materials.
Ensuring Safety and Integrity in Chemical Powder Packaging
Packaging chemical powders poses unique challenges due to the fine particle size, which can lead to potential leakage or contamination. Printed BOPP Woven sacks address these issues through innovative design features:
Outer Lamination
The outer lamination layer provides an additional barrier, safeguarding contents from moisture, dust, and environmental contaminants. This layer also enhances the bag’s aesthetic appeal with high-resolution prints.
Internal Liners
For products requiring extra protection, an internal liner is included. These liners, typically made of polyethylene, seal the contents and prevent powder leakage even under high-pressure handling.
Improved Weaving Density
Manufacturers enhance the weaving density of the polypropylene fabric to create a tighter mesh. This improvement minimizes gaps between fibers, ensuring the safe containment of powdery materials.
Parameter | Specification |
---|---|
Weave Density | 10×10 to 14×14 per inch |
Lamination Thickness | 20 to 30 microns |
Liner Material | LDPE (Low-Density Polyethylene) |
Liner Thickness | 25 to 60 microns |
Tensile Strength | 150 to 220 kgf/m |
Advanced Sealing Techniques
High-quality sealing methods, such as heat sealing and ultrasonic sealing, ensure the closure points are completely secure, preventing any escape of fine particles.
Technical Advantages of Printed Woven Bags for Chemical Materials
Printed Woven Bags deliver unmatched performance across diverse applications. Here’s how their features meet the demands of chemical powder packaging:
- High Load Capacity
These bags can handle weights up to 50 kg or more, accommodating large quantities of material efficiently. - Chemical Resistance
Polypropylene offers excellent resistance to a variety of chemicals, ensuring the bag’s integrity when in contact with its contents. - UV Stabilization
UV stabilization options are available, protecting the bags from degradation due to prolonged exposure to sunlight.
Comparative Analysis: Features of Printed BOPP Woven Bags
The table below highlights the advantages of Printed BOPP Woven Bags over other types of packaging.
Feature | BOPP Woven Bags | Paper Bags | PE Bags |
---|---|---|---|
Tear Resistance | Excellent | Moderate | Low |
Moisture Protection | High | Low | High |
Custom Printing | Multi-color | Limited | Limited |
Environmental Impact | Recyclable | Biodegradable | Non-recyclable |
Applications in Chemical Powder Packaging
Printed BOPP Woven sacks are widely used across industries handling chemical powders, including:
- Construction Materials
For materials like calcium titanate and silica powder, these bags provide moisture resistance, ensuring the quality of the contents. - Industrial Chemicals
Products like titanium dioxide and zinc sulfate benefit from the strong sealing and tight weave that prevent powder spillage during transportation. - Agricultural Chemicals
Fertilizers and other powdered agricultural products are securely stored in these bags, thanks to their high tensile strength.
Customization Options to Meet Industry Needs
To cater to the specific requirements of various sectors, Printed Woven Bags offer a range of customization features:
- Size Variations: From 5 kg to 50 kg capacities.
- Lamination: Glossy or matte finishes.
- Printing: Up to 8-color rotogravure printing for intricate designs.
- Closure Styles: Options include heat-sealed, stitched, or valved closures.
Customizable Element | Available Options |
---|---|
Bag Size | 30×40 cm to 60×100 cm |
Printing Colors | 1 to 8 |
Finish | Glossy/Matte |
Gussets | Flat/Side/Bottom |
Innovations in Preventing Leakage and Contamination
To address leakage challenges in chemical packaging, manufacturers integrate multiple layers of security. Below are some innovative methods:
- Multi-Layer Construction
Combining woven polypropylene with BOPP film and inner liners creates a three-layer structure that ensures maximum protection. - Ultrasonic Sealing
Advanced ultrasonic sealing technology produces airtight closures without the need for adhesives, making it ideal for sensitive materials. - Enhanced Stiffness
Laminated layers add stiffness to the bags, preventing them from collapsing during storage or transport, thereby reducing the risk of spillage.
Conclusion
Printed BOPP Woven Bags are redefining the standards of chemical powder packaging. Their robustness, customizability, and technical advancements ensure safe and efficient storage and transport. By incorporating advanced lamination, internal liners, and improved weaving techniques, these bags offer unparalleled protection against leakage and contamination, making them the industry’s go-to solution for chemical materials.