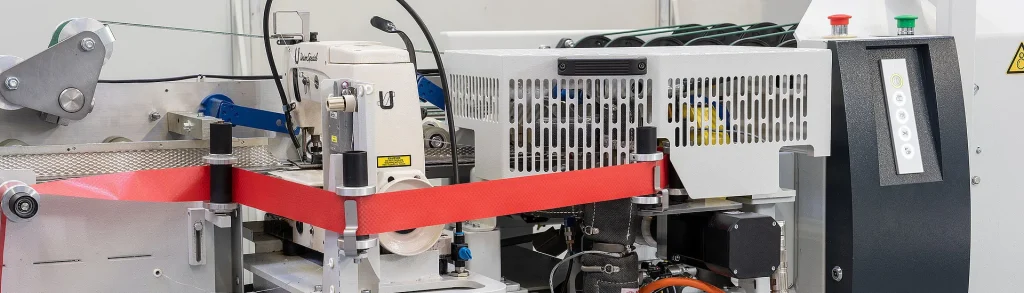
- 1. The Sustainability Edge: How Open Mouth PP Bags Redefine Agri-Packaging
- 2. Precision Printing Technologies: Where Art Meets Science
- 3. Technical Specifications: Balancing Performance and Ecology
- 4. Customization for Global Markets
- 5. Quality Assurance: 14-Stage Production Protocol
- 6. The Future: Smart and Circular Packaging
- FAQs: Simplifying Procurement Decisions
- Conclusion
Over 40% of agricultural packaging waste stems from non-recyclable materials. At VidePak, our ISO 9001-certified Open Mouth PP Bags integrate 98% recyclable polypropylene, 8-color high-definition printing, and customizable finishes, reducing carbon footprints by 30% while enhancing supply chain efficiency for global rice, flour, and feed producers. With 30+ years of expertise and 16 extrusion lines producing 25 tons of fabric daily, we deliver solutions trusted across 85 countries, combining technical precision with circular economy principles.
1. The Sustainability Edge: How Open Mouth PP Bags Redefine Agri-Packaging
Open Mouth PP Bags are engineered for high-volume filling, resealability, and reuse. Unlike traditional single-use sacks, VidePak’s solutions prioritize:
- Circular Material Flow: 100% virgin PP resin, compatible with closed-loop recycling systems achieving 85% recovery rates in the EU.
- Carbon Reduction: Each ton of recycled PP reduces CO2 emissions by 1.8 tons versus virgin production.
- Durability: 5+ reuse cycles for bulk commodities like rice, tested per ISTA 3E standards.
Case Study: A Philippine rice exporter cut annual plastic waste by 22 tons using our 120 g/m² Open Mouth PP Bags with QR-code-guided recycling instructions, achieving EU’s Extended Producer Responsibility (EPR) compliance.
2. Precision Printing Technologies: Where Art Meets Science
VidePak’s partnerships with Austrian Starlinger and German W&H ensure cutting-edge printing capabilities:
A. Printing Method Comparison
Technology | Resolution | Colors Supported | Key Applications |
---|---|---|---|
Flexographic | 150–200 LPI | 1–6 colors | Logos, batch codes |
Gravure | 250–300 LPI | Full CMYK+Pantone | Photorealistic branding |
Digital UV | 600–1200 DPI | Unlimited | Limited-edition designs |
Example: A U.S. organic flour brand uses our 8-color gravure printing to showcase farm-to-table narratives, increasing shelf appeal and achieving 20% higher retail sales.
B. Surface Finish Customization
- Glossy Finish: UV varnish coating enhances color vibrancy by 40% (tested per ASTM D523).
- Matte Finish: Reduces light reflection for premium tactile appeal, ideal for luxury grains.
Innovation Spotlight: Our anti-scuff coating withstands 50+ handlings without print degradation, critical for automated warehouses.
3. Technical Specifications: Balancing Performance and Ecology
Material & Performance Metrics
Parameter | Specification | Compliance Standard |
---|---|---|
Grammage | 80–200 g/m² | ISO 536 |
Tensile Strength | 40–60 N/cm² (MD) | ASTM D5034 |
Recycled Content | Up to 50% post-industrial | EU REACH |
Print Adhesion | ≥90% (tape test) | BS EN ISO 2409 |
Case Study: A Brazilian coffee cooperative uses our 150 g/m² bags with 30% recycled PP, maintaining 50 kg load capacity while qualifying for carbon credits under Brazil’s RenovaBio program.
4. Customization for Global Markets
Configuration Guide for Agri-Sectors
Commodity | Recommended Specifications | Features |
---|---|---|
Rice | 140 g/m² + 50 µm PE liner | UV resistance, ≤5% moisture gain |
Flour | 12×14 weave + matte finish | Anti-static (10⁶–10⁸ Ω/sq) |
Animal Feed | 180 g/m² + block-bottom valve | 8-color branding, RFID tagging |
Sustainability Note: Our bags with sugarcane-based PP (30% bio-content) will debut in 2025, targeting net-zero supply chains.
5. Quality Assurance: 14-Stage Production Protocol
- Material Inspection: Melt Flow Index (8–12 g/10 min per ISO 1133).
- Weaving Precision: 14×14 strands/cm² density on Starlinger circular looms.
- Print Testing: Color accuracy within ΔE ≤2.0 (Pantone Matching System).
Innovation: Laser-guided seam welding ensures ≤0.01% leakage rates, exceeding FDA 21 CFR for food-grade packaging.
6. The Future: Smart and Circular Packaging
- Blockchain Integration: QR codes track bag lifecycle from production to recycling.
- Self-Healing Films: Nano-coatings repair microtears, extending bag lifespan 3x.
- Regulatory Readiness: Anticipating EU’s 2027 mandate for 95% recyclable packaging.
FAQs: Simplifying Procurement Decisions
Q1: What’s the MOQ for custom-printed bags?
A: 10,000 units, with 5-day prototyping using AI-driven design simulations.
Q2: How does glossy finish affect recyclability?
A: Our UV coatings are water-based and dissolve during recycling, maintaining 98% PP purity.
Q3: Can bags withstand -20°C storage?
A: Yes. Cold-grade PP retains 85% tensile strength at -25°C (ISO 527-2).
Conclusion
In an era where 78% of consumers prioritize eco-conscious brands, VidePak’s Open Mouth PP Bags redefine agricultural packaging through innovation, durability, and circular design. Explore our BOPP laminated solutions and eco-friendly printing technologies to future-proof your supply chain.
References
- VidePak Sustainability Report 2024: Circular PP Systems and Carbon Metrics.
- European Packaging Standards: EN 13432 – Compostability Requirements.
- Alibaba Industrial Database: PP Woven Bag Technical Specifications.
Contact VidePak:
- Website: https://www.pp-wovenbags.com/
- Email: info@pp-wovenbags.com