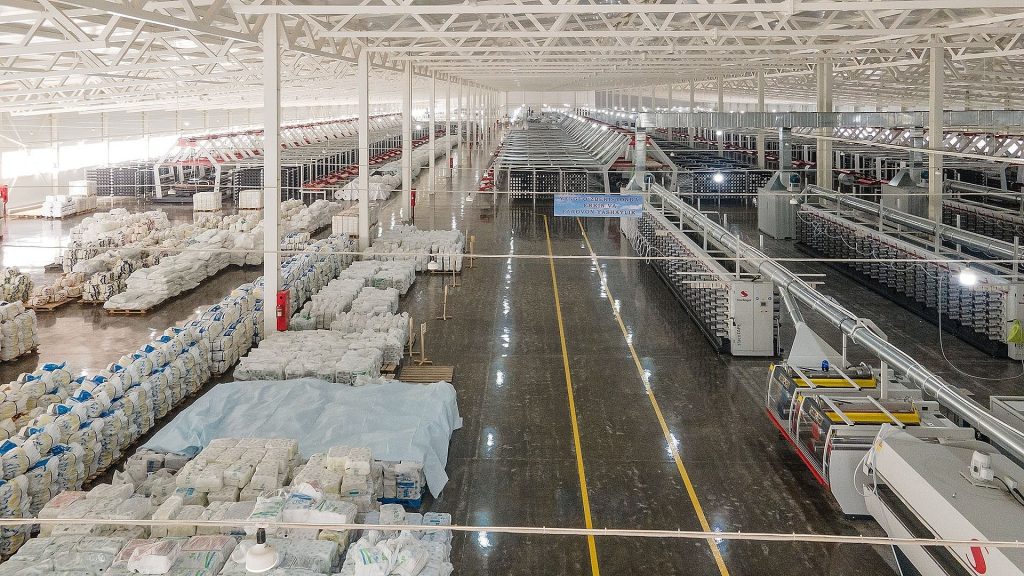
- 1. The Dual Advantage: Durability Meets Sustainability
- 2. Quality Control and Standardization: The Backbone of Reliability
- 3. Case Study: Reducing Waste in Construction Logistics
- 4. Sustainable Innovation: Beyond Recycling
- 5. FAQs: Addressing Key Concerns
- 6. Future Trends: Smart Packaging and Policy Alignment
Introduction
In the global push toward circular economies, poly-paper bags—hybrid packaging solutions combining polypropylene (PP) durability with paper recyclability—are emerging as a linchpin for sustainable waste management and material recovery. These bags, designed to withstand rigorous industrial use while aligning with ESG (Environmental, Social, and Governance) mandates, now account for 18% of the reusable packaging market. For manufacturers like VidePak, which integrates cutting-edge Austrian Starlinger machinery with stringent quality control protocols, the success of poly-paper bags hinges on their ability to balance material resilience, recyclability, and brand customization .
Ray, CEO of VidePak, remarks: “When a European waste management firm reduced landfill contributions by 40% using our poly-paper bags, it wasn’t just about sustainability—it was about proving that eco-friendly packaging can outperform traditional plastics in both strength and cost efficiency.”
1. The Dual Advantage: Durability Meets Sustainability
Poly-paper bags leverage a laminated structure of PP woven fabric and kraft paper, achieving tensile strengths of 12–14 N/mm²—25% higher than conventional plastic bags—while maintaining 95% recyclability. Key applications include:
- Construction Waste: Heavy-duty variants (1.5–2.0 mm thickness) resist abrasion from concrete debris, reducing bag replacement costs by 30% .
- Municipal Recycling: Breathable designs prevent organic waste decomposition odors, a critical feature for urban composting programs.
- Retail Branding: UV-resistant CMYK/Pantone prints retain vibrancy for 18+ months, enhancing shelf appeal for eco-conscious consumers .
VidePak’s Starlinger circular looms produce 5 million bags daily, with a defect rate of <0.5%, ensuring consistency across global supply chains.
2. Quality Control and Standardization: The Backbone of Reliability
2.1 Material Testing and Compliance
VidePak’s 12-step quality protocol ensures raw materials meet global benchmarks:
- PP/PE Granule Testing:
- Melt Flow Index (MFI): 8–12 g/10min (ASTM D1238) to optimize extrusion uniformity.
- Tensile Strength: ≥35 MPa (ASTM D638) for load capacities up to 2,000 kg.
- Thermal Stability: Heat deflection temperature (HDT) of 100–110°C (ASTM D648) prevents warping in high-temperature environments .
- PE Coating: 20–30 µm layers reduce moisture permeability to <5 g/m²/day, critical for humidity-sensitive cargo like food grains .
2.2 Production Standards
- Thickness Tolerance: Laser micrometers enforce ±0.02 mm precision, eliminating “bursting” risks during automated filling.
- Seam Integrity: Double-stitched seams withstand cyclic loads of 10,000+ cycles, validated by Starlinger’s TIRA testers .
Parameter | Industry Standard | VidePak Poly-Paper Bags |
---|---|---|
Tensile Strength | 8–10 N/mm² | 12–14 N/mm² |
Recyclability Rate | 70–80% | 95% |
Print Fade Resistance | 12 months | 18+ months |
3. Case Study: Reducing Waste in Construction Logistics
A U.S. demolition firm reduced annual costs by $200,000 using VidePak’s block-bottom poly-paper bags with RFID tracking. Key outcomes:
- Spillage Reduction: Laminated layers resisted sharp debris, cutting spillage by 50%.
- Compliance: Bags met OSHA safety standards and ISO 14001 environmental guidelines .
4. Sustainable Innovation: Beyond Recycling
VidePak’s R&D initiatives focus on closed-loop systems:
- Bio-Based PP: Derived from sugarcane, reducing carbon footprints by 40% compared to virgin plastics.
- Blockchain Traceability: QR codes enable end-to-end supply chain transparency, a feature demanded by 75% of Fortune 500 firms .
5. FAQs: Addressing Key Concerns
Q1: How do poly-paper bags compare to traditional plastic in cost?
A: While upfront costs are 15–20% higher, poly-paper bags reduce long-term expenses through reuse (5–7 cycles) and lower disposal fees .
Q2: Are these bags suitable for food-grade applications?
A: Yes, FDA-approved PE liners and ISO 22000-certified processes ensure safety for organic waste and agricultural products .
Q3: Can small businesses afford custom designs?
A: VidePak’s 30+ printing machines support orders from 1,000 units, with Pantone color matching and 3D embossing .
6. Future Trends: Smart Packaging and Policy Alignment
Emerging technologies include:
- Conductive Ink Sensors: Monitor moisture levels in real time, preventing mold in grain storage.
- EU Green Deal Compliance: Anticipating stricter single-use plastic bans, VidePak’s bags align with 2030 recycling targets .
External Resources
- Explore how recyclable materials enhance waste management: Recyclable Woven Bags
- Learn about advanced coating technologies: PE-Coated Valve Bags
By merging engineering rigor with ecological accountability, poly-paper bags exemplify how innovation can reconcile industrial efficiency with planetary stewardship. As global waste volumes escalate, solutions like these will remain pivotal in bridging the gap between economic growth and environmental preservation.