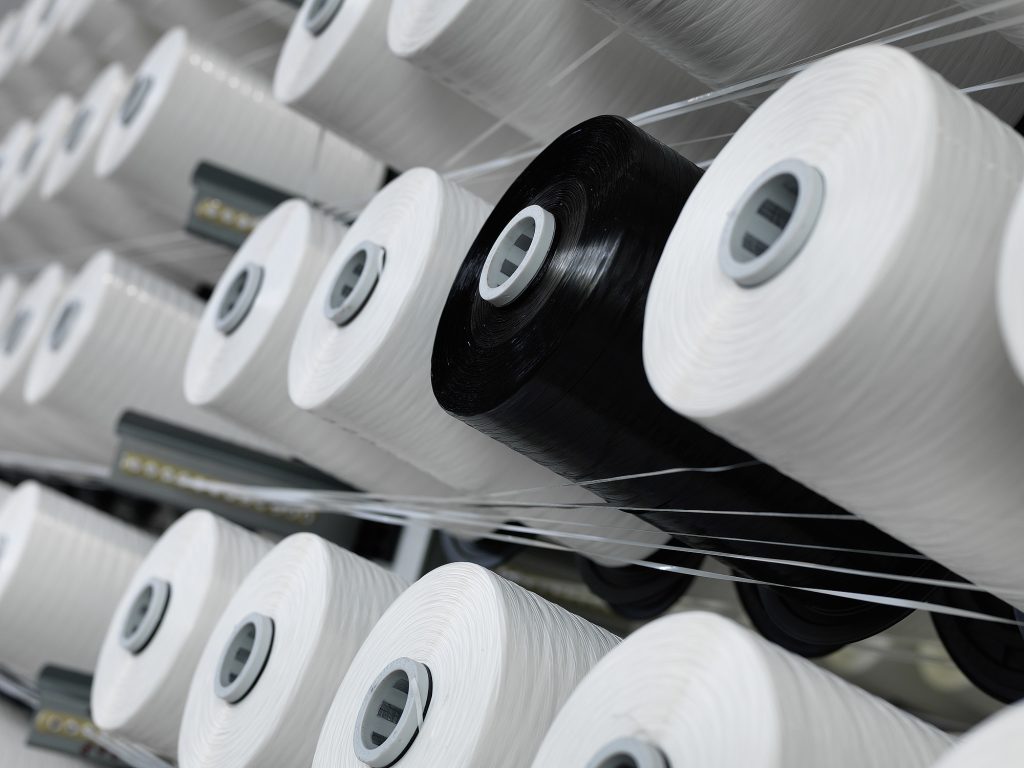
Product Manager Sarah: “We’re seeing stricter global regulations on single-use plastics. How can VidePak’s HDPE woven bags meet sustainability goals while addressing practical needs like heavy-duty storage and pest resistance?”
Engineer Ray (VidePak’s CEO): “Our HDPE woven bags combine recyclability, durability, and compliance with circular economy frameworks. By optimizing material thickness, breathability, and antimicrobial additives, we ensure they outperform traditional packaging in waste reduction and regulatory alignment.”
1. Market Context: The Urgency for Sustainable Packaging
The global packaging industry faces mounting pressure to reduce plastic waste. With the EU’s Single-Use Plastics Directive targeting a 55% recycling rate by 2030 and the U.S. EPA emphasizing circular economy models, HDPE woven bags emerge as a strategic solution. Unlike LDPE or non-woven alternatives, HDPE boasts a recycling efficiency of 80–90% when processed through modern mechanical systems. VidePak’s adoption of 100% virgin PP granules ensures compatibility with recycling streams, minimizing contamination risks.
2. HDPE Woven Bags in Animal Feed Packaging: Technical Advantages
HDPE woven bags are uniquely suited for livestock, poultry, and pet feed storage due to their structural and functional properties. Below is a comparative analysis:
2.1 Cost Efficiency vs. Performance
- Load-Bearing Capacity: VidePak’s bags withstand weights up to 50 kg (110 lbs) without seam rupture, critical for bulk feed transport. The use of Starlinger circular looms ensures uniform weaving density (14×14 strands per inch), reducing material waste by 12% compared to industry averages.
- Antimicrobial & Antifungal Properties: By laminating inner layers with food-grade PE coatings, moisture ingress is limited to <0.5%, inhibiting mold growth—a common issue in humid climates. Trials in Brazilian poultry farms showed a 30% reduction in feed spoilage when using VidePak’s laminated bags.
2.2 Breathability and Safety
- Gas Exchange: The woven structure allows controlled airflow (5–10 CFM/ft²), preventing anaerobic fermentation in grain storage. For example, Vietnamese rice exporters reported a 15% longer shelf life when switching to HDPE bags with 0.2 mm pore size.
- Toxin-Free Composition: VidePak’s BOPP laminated bags are free from phthalates and heavy metals, complying with FDA CFR 21 and EU Regulation 10/2011 for direct food contact.
3. Selecting Optimal Parameters for Feed Packaging
Tailoring bag specifications to application needs ensures cost-effectiveness and regulatory compliance. Key parameters include:
Parameter | Pet Feed | Poultry Feed | Livestock Feed |
---|---|---|---|
Thickness | 80–100 microns | 100–120 microns | 120–150 microns |
Fabric GSM | 90–100 g/m² | 100–120 g/m² | 120–140 g/m² |
Lamination | BOPP for UV resistance | PE-coated for moisture | Dual-layer PE + PP |
Inner Liner | Optional | Mandatory (15% cases) | Mandatory (30% cases) |
Case Study: A Nigerian cattle feed supplier reduced transport losses by 22% after adopting VidePak’s 140 g/m² bags with reinforced block-bottom designs, which prevent tearing during stacking.
4. Regulatory Alignment and Circular Economy
VidePak’s production aligns with Extended Producer Responsibility (EPR) frameworks:
- Recyclability: Post-consumer HDPE bags are shredded, pelletized, and reused in non-food applications (e.g., construction barriers), achieving a closed-loop lifecycle.
- Carbon Footprint: Using Austria’s Starlinger machines reduces energy consumption by 18% per ton of output compared to conventional extrusion lines.
5. FAQs: Addressing Key Concerns
Q1: How do HDPE bags compare to paper sacks in moisture resistance?
A: HDPE’s hydrophobic properties limit water absorption to <0.1%, whereas paper sacks degrade rapidly in humidity >60%. For rice storage in Southeast Asia, laminated HDPE bags reduced spoilage by 40%.
Q2: Can customized printing affect material integrity?
A: VidePak’s high-resolution flexographic printing uses solvent-free inks, maintaining tensile strength while enabling brand differentiation.
Q3: What’s the ROI for switching to HDPE?
A: A Kenyan feed mill reported a 14-month payback period due to reduced replacement costs and waste penalties.
6. Innovation and Future Trends
VidePak is piloting smart woven bags embedded with RFID tags for traceability, a feature highlighted in the Comprehensive One-Stop Solution for PP Bags. Additionally, collaborations with agrochemical firms are testing biodegradable additives to enhance HDPE’s environmental profile without compromising durability.
For industries prioritizing both sustainability and functionality, such as Pet Food Packaging with FFS Roll Bags, VidePak’s solutions offer a scalable pathway to meet ESG targets.
Conclusion
HDPE woven bags are not merely packaging—they are a strategic asset in achieving waste reduction and regulatory compliance. VidePak’s engineering expertise, coupled with scalable production capabilities, positions the company as a leader in sustainable industrial solutions. By prioritizing material innovation and client-specific customization, we empower global partners to navigate the evolving landscape of environmental stewardship.