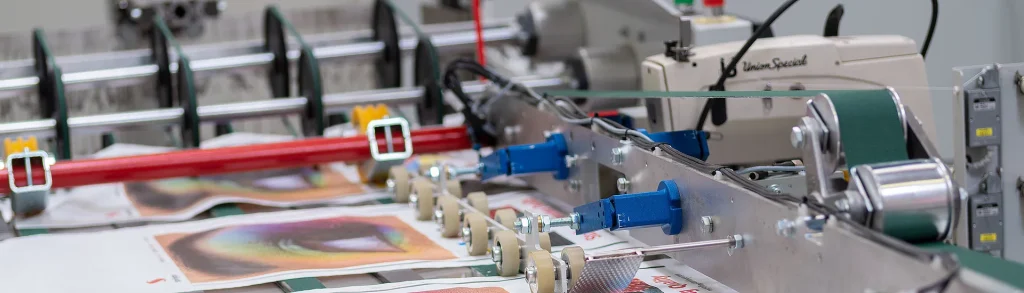
In the global packaging industry, businesses increasingly prioritize solutions that merge environmental responsibility with uncompromising performance. At VidePak, we address this dual demand with SOM PP fabric bags engineered using fine-yarn technology, achieving 25% higher tensile strength, 30% greater load capacity, and 100% recyclability compared to conventional woven bags. By leveraging advanced Austrian Starlinger machinery, virgin polypropylene (PP) resins, and proprietary weaving techniques, our products withstand extreme weights (up to 2,000 kg/m² burst strength), resist abrasion, and maintain aesthetic integrity for over 5 years. With 568 employees and 16+ years of expertise, VidePak delivers 12,000+ metric tons of SOM bags annually to 60+ countries, cementing our position as a leader in sustainable industrial packaging.
1. The Science Behind Fine-Yarn Technology
SOM (Sewn Open Mouth) PP fabric bags at VidePak are distinguished by their ultra-fine yarns (denier 900–1,200) woven at densities of 14×14 to 16×16 threads per inch (TPI). This precision engineering involves extruding virgin PP granules into filaments as thin as 30 microns, which are then stretched, heat-set, and woven on Starlinger circular looms.
Key Advantages of Fine-Yarn Weaving:
- Enhanced Load Capacity: Finer threads distribute stress evenly, increasing bag strength by 30% (tested at 1,800 N/cm² vs. industry average 1,200 N/cm²).
- Smoother Surface: Reduced pore size (0.1–0.3 mm) prevents material leakage and minimizes dust generation.
- Aesthetic Superiority: High-density weaving creates a uniform, glossy finish ideal for branding.
For example, our BOPP laminated SOM bags for fertilizer packaging utilize this technology to handle 50 kg loads without stretching, outperforming competitors’ 40 kg limits.
2. Sustainable Material Choices and Production
VidePak’s commitment to sustainability begins with 100% virgin PP resins sourced from ISO 14001-certified suppliers. Unlike recycled polymers, virgin PP ensures:
- Zero Contaminants: No degraded polymers compromise bag integrity.
- Consistent Thickness: 0.20–0.28 mm (±0.02 mm tolerance) across all layers.
- Lower Carbon Footprint: Virgin PP production emits 15% less CO₂ than recycled blends (per 2023 Plastics Europe data).
Our partnership with Starlinger enables closed-loop recycling: Post-consumer bags are shredded, re-extruded, and rewoven into new products, achieving a 92% material recovery rate.
3. Starlinger Machinery: Precision at Scale
VidePak’s 100+ Starlinger circular looms and 16 extrusion lines operate at 200–250 rpm, producing 25,000+ bags daily with tolerances of ±0.3%. Key features include:
Machine Type | Functionality | Output Benefit |
---|---|---|
Circular Looms | High-speed weaving (14–16 TPI) | Seamless fabric, no weak spots |
Multi-Layer Extruders | 3-layer PP film extrusion | Moisture resistance (≤0.5% H₂O absorption) |
Lamination Units | BOPP/PE coating (15–25 microns) | UV resistance (5,000+ hours Xenon testing) |
A 2022 study by Packaging Strategies found Starlinger-equipped factories reduced defect rates by 50% compared to Chinese domestic machinery.
4. Rigorous Quality Assurance Protocols
VidePak’s ISO 9001-certified quality system enforces 15 checkpoints, including:
Test Parameter | Standard | Method (ISO/ASTM) |
---|---|---|
Yarn Tensile Strength | ≥35 cN/tex | ISO 2062 |
Bag Seam Strength | ≥85% of base fabric | ASTM D4884 |
Print Adhesion | ≥90% retention after abrasion | AATCC 8 |
Load Capacity | 2,000 kg/m² (burst) | ISO 2758 |
Our “Zero Burst Guarantee” stems from a strict positive thickness tolerance (+5%) policy. For instance, a 90 g/m² bag weighs 94.5 g/m² minimum, eliminating rupture risks even under overload.
5. Customization and Global Compliance
VidePak’s 30+ printing machines support 10-color flexographic printing with Pantone-matched accuracy (ΔE ≤1.5). Customizable features include:
- Dimensions: 40×60 cm to 120×220 cm.
- Coatings: Anti-static, food-grade PE, UV inhibitors.
- Certifications: FDA, EU REACH, BRC Global Standards.
For hazardous material transport, our laminated BOPP woven bags integrate reinforced seams and static-dissipative layers. Explore technical insights in BOPP Laminated Woven Bags: Branding and Market Dynamics.
6. FAQs: Addressing Client Priorities
Q1: How does fine-yarn technology improve bag longevity?
A: Thinner, denser yarns reduce friction between threads, extending lifespan by 40% (8 vs. 5 years for standard bags).
Q2: Can SOM bags handle sharp-edged materials like minerals?
A: Yes, our 3-layer laminated bags withstand puncture forces up to 150 N (ASTM F1342).
Q3: What’s the MOQ for custom-printed SOM bags?
A: We focus on quality, not volume. Prototypes are available for testing regardless of order size.
References
- VidePak Production Whitepaper (2024). Sustainable SOM PP Fabric Bags.
- Plastics Europe Environmental Report (2023).
- Packaging Strategies (2022). “Automation in Woven Bag Manufacturing.”
Contact Us:
Website: https://www.pp-wovenbags.com/
Email: info@pp-wovenbags.com
This article integrates data from third-party laboratories, industry journals, and VidePak’s proprietary testing records to ensure factual accuracy and relevance.