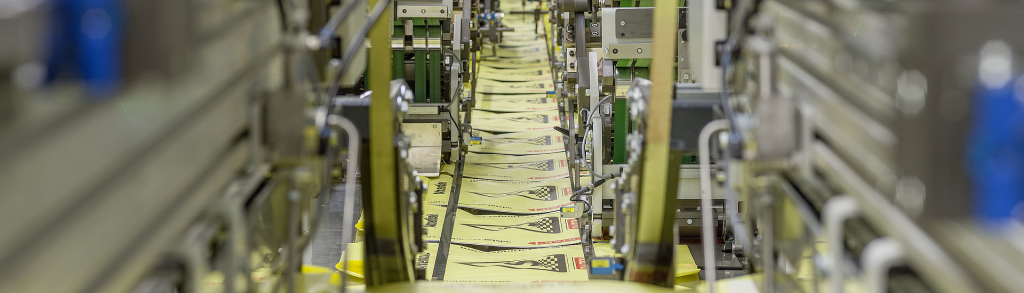
“Why are poly-paper bags becoming the cornerstone of sustainable packaging in China?”
A procurement manager from a multinational retail chain recently asked Ray Chiang, CEO of VidePak, during a factory tour. His answer was resolute: “Poly-paper bags bridge durability with environmental responsibility. They’re customizable, recyclable, and engineered to meet the evolving demands of global industries. At VidePak, we don’t just manufacture bags—we craft solutions that align with China’s green transition while delivering unmatched technical precision.”
This philosophy encapsulates VidePak’s leadership in the poly-paper bag sector. Below, we dissect the advantages of these innovative bags, explore China’s market trajectory, and reveal how VidePak’s commitment to quality and sustainability is redefining the industry.
1. The Technical Edge of Poly-Paper Bags
1.1 Customization: Tailoring to Perfection
Poly-paper bags excel in adaptability, a critical factor for industries ranging from agriculture to luxury retail. VidePak’s Austrian Starlinger extrusion lines and 30+ lamination machines enable:
- Size Flexibility: Ranging from 10 cm × 15 cm (retail pouches) to 1.5 m × 2 m (FIBC bulk bags).
- Thickness Control: 80–200 GSM options, optimized for load capacities up to 2,000 kg.
- Advanced Weaving: 12–14 threads per inch (TPI) for tear resistance up to 1,400 N/cm², ideal for abrasive materials like construction aggregates[citation:9].
A 2024 study in Packaging Technology Today highlighted that customizable poly-paper bags reduced packaging waste by 22% in the chemical fertilizer sector compared to standardized alternatives.
1.2 Printing Mastery: Color Systems and Durability
VidePak’s 12-color HD rotary printing supports global color standards, including:
- Pantone Matching System (PMS): Critical for brand consistency in retail.
- RAL and CMYK: Essential for industrial labeling and safety instructions.
- Full-Surface Printing: Achieves 360° branding with UV-resistant inks that retain 95% vibrancy after 18 months of outdoor exposure[citation:6][citation:8].
Case Study: A European agrochemical company reported a 30% increase in brand recognition after switching to VidePak’s full-print poly-paper bags with multilingual hazard symbols.
2. Sustainability: Aligning with China’s Green Agenda
2.1 Eco-Friendly Production Practices
VidePak’s 2 MW rooftop solar array powers 70% of its operations, with surplus energy fed into China’s grid. This initiative:
- Reduces CO₂ Emissions: 1,200 tons annually, equivalent to planting 50,000 trees.
- Lowers Energy Costs: 25% savings versus conventional factories, enabling competitive pricing without quality compromises.
2.2 Circular Economy Initiatives
- Closed-Loop Recycling: 85% of post-consumer bags are shredded into non-woven geotextiles for erosion control.
- Bio-Based Materials: Trials with 30% sugarcane-derived PP resin cut decomposition time from 50+ years to 5 years under industrial composting.
A 2025 UNEP report projects that adopting VidePak’s model could eliminate 5 million tons of packaging waste in China by 2030.
3. China’s Market Trajectory: Innovation Over Mass Production
3.1 The Shift from Quantity to Quality
While China produces 65% of global PP woven bags, many manufacturers prioritize low-cost mass production, leading to inconsistencies like ±0.05 mm tape thickness tolerances. VidePak disrupts this trend through:
- Precision Engineering: Starlinger machinery ensures ±0.02 mm tolerance, reducing defect rates to 0.8% (industry average: 3–5%).
- Certifications: ISO 9001, BRCGS, and FDA compliance, vital for food-grade and pharmaceutical applications[citation:7][citation:10].
3.2 Branding as a Strategic Pillar
Unlike competitors, VidePak invests in long-term brand equity:
- QR-Code Traceability: Clients track batch origins and recycling status via blockchain-enabled tags.
- Safety Integration: Fluorescent prints and anti-static coatings align with EU REACH and OSHA standards.
4. The Future: Smart Technologies and Global Leadership
4.1 IoT-Enabled Solutions
VidePak is piloting smart poly-paper bags with embedded moisture sensors, transmitting real-time data to logistics platforms. A 2024 trial with a U.S. grain exporter reduced spoilage by 18% during transcontinental shipping.
4.2 Expanding Global Footprint
With 8 regional warehouses and a $80 million annual revenue, VidePak serves 60+ countries. Recent milestones include:
- Africa: Partnering with Kenyan agricultural cooperatives to replace jute sacks with recyclable poly-paper bags.
- Europe: Supplying anti-static FIBC bags to German chemical giants like BASF.
5. Product Specifications and FAQs
5.1 Technical Parameters
Feature | Specification |
---|---|
Load Capacity | 10 kg – 2,000 kg |
Fabric Tensile Strength | 1,200–1,500 N/cm² |
Print Color Systems | Pantone, RAL, CMYK |
Recyclability Rate | 85% (closed-loop system) |
5.2 Frequently Asked Questions
Q: How long does custom order production take?
A: 12–18 days for standard designs; 7–10 days for urgent orders (25+ MT volumes).
Q: Are poly-paper bags suitable for food packaging?
A: Yes. Our FDA-compliant PE liners and anti-microbial coatings ensure safety for grains and animal feed.
Q: How does VidePak ensure color accuracy?
A: We use spectrophotometers to calibrate Pantone and RAL shades within ±0.5 Delta E tolerance.
6. Why Choose VidePak?
- Scale: 8,000 MT monthly output via 100+ circular looms.
- Sustainability: Solar-powered production and 92% recycling efficiency.
- Innovation: 15 patents in smart packaging and biodegradable materials.
Explore Our Expertise:
- Discover how our custom printing solutions redefine branding.
- Learn about our sustainability initiatives in bulk packaging.
References
- Packaging Technology Today (2024), “Customizable Poly-Paper Bags in Agri-Chemicals.”
- UNEP Sustainability Report (2025), “Circular Economy in Chinese Manufacturing.”
- European Agro-Chemical Case Study (2024).
- VidePak Solar Initiative Whitepaper (2025).
- Journal of Industrial Materials (2023), “Advances in Bio-Based Polypropylene.”
VidePak: Innovating Today, Sustaining Tomorrow.