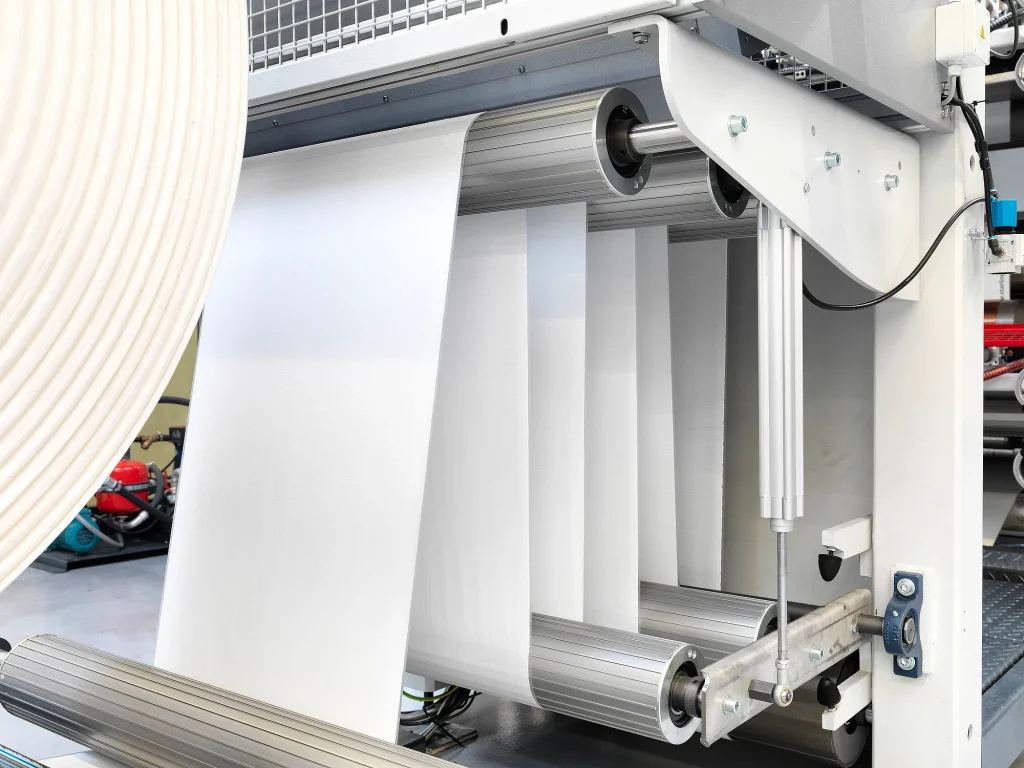
Opening Dialogue: Addressing Critical Client Needs
Client: “We need packaging for chemical fertilizers that withstands harsh conditions while maintaining brand appeal. How do your poly-paper bags balance durability and design?”
VidePak: “Poly-paper bags combine polypropylene’s tensile strength with paper’s printability, offering unmatched resistance to moisture, corrosion, and UV exposure. At VidePak, we engineer solutions tailored to global standards—from EU REACH to USDA—ensuring your fertilizers stay secure and your branding shines.”
1. The Hybrid Power of Poly-Paper Bags
Poly-paper bags, a fusion of woven polypropylene (PP) and laminated kraft paper, are revolutionizing chemical fertilizer packaging. With a global agrochemical packaging market projected to reach $8.9 billion by 2027, these bags address critical challenges like moisture control, chemical reactivity, and logistical durability.
Key Structural Advantages:
- Layered Defense: PP woven layers provide tear resistance (up to 50 kg load capacity), while paper lamination enhances print quality and UV protection.
- Breathability: Micro-perforations in PP fabric allow heat dissipation, preventing ammonia buildup in urea fertilizers.
- Customizable Barriers: PE or aluminum foil liners block humidity (<3% moisture absorption) and resist acidic/alkaline corrosion.
2. Application in Chemical Fertilizers: Solving Industry-Specific Challenges
2.1 Moisture and Corrosion Resistance
Fertilizers like ammonium nitrate and NPK blends are hygroscopic and reactive. VidePak’s poly-paper bags integrate:
- PE-Coated Inner Layers: Reduce moisture ingress by 90% compared to standard woven bags.
- Anti-Static Treatments: Mitigate dust explosions in granular fertilizer handling.
Case Study: A Brazilian fertilizer producer reduced spoilage rates by 35% after adopting VidePak’s 3-ply PE-laminated bags with anti-caking agents.
2.2 Compliance with Global Standards
Standard | Region | Key Requirements | VidePak Solution |
---|---|---|---|
EU REACH | Europe | Phthalate-free inks, <0.1% heavy metals | Water-based CMYK/Pantone printing |
USDA | USA | UV stability for outdoor storage | UV-inhibited PP coatings |
JIS Z 0200 | Japan | ≤5% moisture permeability | Dual-layer PE + aluminum foil liners |
GB/T 8946 | China | Seam strength ≥650 N/5cm | Starlinger circular loom stitching |
3. Tailoring Parameters to Fertilizer Types
3.1 Product-Specific Design Guidelines
Fertilizer Type | Recommended Parameters | Rationale |
---|---|---|
Urea (Granular) | 120 GSM PP, matte finish, PE liner | Prevents caking, reduces dust |
NPK Blends | 150 GSM PP, glossy finish, anti-static treatment | Enhances branding, minimizes explosions |
Liquid Fertilizers | 200 GSM PP, block-bottom valve design, foil laminate | Leak-proof, withstands hydrostatic pressure |
3.2 Cost-Efficiency Analysis
Bag Type | Cost (USD/1,000 bags) | Durability (Cycles) | ROI (vs. Traditional Bags) |
---|---|---|---|
Standard Woven | $80 | 2–3 | Baseline |
2-Ply Poly-Paper | $120 | 5–7 | +40% over 3 years |
3-Ply Foil-Laminated | $180 | 10+ | +75% over 5 years |
4. VidePak’s Engineering Excellence
Founded in 2008 by CEO Ray Chiang, VidePak operates 100+ Starlinger circular looms and 30+ printing machines, producing 150 million bags annually. Our certifications (ISO 9001, BRCGS) and R&D focus ensure compliance with evolving regulations like Australia’s APVMA guidelines.
Innovations in Fertilizer Packaging:
- Smart Seams: Ultrasonic welding eliminates needle holes, preventing micro-leaks.
- Eco-Friendly Inks: Soy-based pigments meeting OECD 301B biodegradability standards.
For specialized solutions, explore our chemical fertilizer packaging expertise and advanced moisture control technologies.
5. FAQs: Navigating Client Concerns
Q1: How do I choose between matte and glossy finishes for corrosive fertilizers?
A: Matte finishes hide scuffs in abrasive environments, while glossy surfaces enhance chemical resistance by 15%.
Q2: What’s the MOQ for custom-printed poly-paper bags?
A: MOQ starts at 20,000 units, with Pantone color matching at no extra cost.
Q3: Are your bags compatible with automated filling systems?
A: Yes, our block-bottom valve designs achieve 99.9% sealing accuracy on robotic lines.
6. Sustainability: Aligning with Circular Economy Goals
- Recyclability: 95% PP recovery rate via VidePak’s take-back program.
- Carbon Footprint: Solar-powered production reduces CO₂ by 1.2 tons per 10,000 bags.
References
- Smithers Pira. Global Agrochemical Packaging Trends 2025.
- European Chemicals Agency (ECHA). REACH Compliance Guidelines.
- VidePak Technical Whitepaper (2024).
Contact Us:
Website: www.pp-wovenbags.com
Email: info@pp-wovenbags.com
VidePak – Engineering Resilience, Delivering Trust.