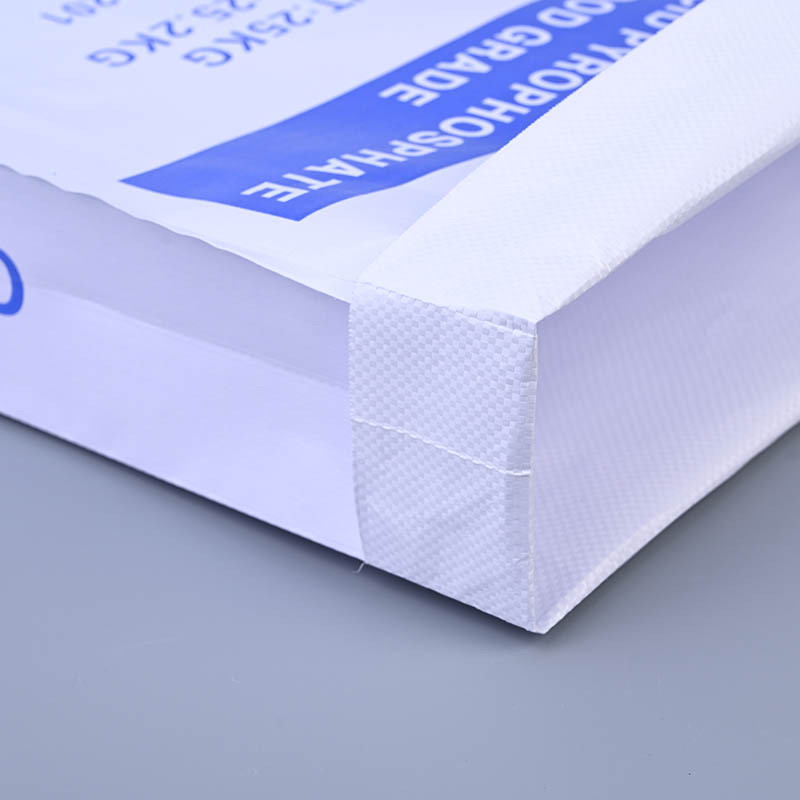
Custom Printed Woven Bags are an indispensable part of the packaging industry, offering a unique blend of durability, functionality, and brand visibility. Whether for industrial packaging, agricultural use, or retail applications, these bags cater to diverse needs by allowing customization in both design and functionality. As consumer demands evolve, businesses are turning to Custom Printed Woven Sacks to not only enhance product visibility but also meet specific requirements in terms of strength, size, and environmental sustainability.
The Popularity of Printed Woven Bags
In the global packaging market, Printed Woven Bags—especially Printed BOPP Woven Bags—are a popular choice due to their strength, versatility, and customization options. For companies looking to differentiate their products, the option to have custom prints on woven bags has become a powerful marketing tool. These bags are primarily made from polypropylene (PP), a material known for its robust properties, which makes them suitable for carrying heavy loads while maintaining structural integrity during transportation and storage.
If you’re looking for more detailed insights into the Custom Printed Woven Bags or Printed Woven Bags and their applications, this article covers how woven bags meet the latest packaging standards.
Common Printing Methods for Woven Bags
When it comes to printing Printed PP Bags and Printed BOPP Woven Bags, there are several techniques available to suit various designs and durability requirements. The most commonly used methods include:
- Flexographic Printing: This is one of the most widely used techniques for printing on woven bags. It involves transferring ink onto the surface of the bag using flexible printing plates. This method is ideal for large volume runs and works well for both simple and intricate designs.
- Rotogravure Printing: Known for its high-quality print and precision, rotogravure printing is perfect for detailed images or color-rich designs. It works by engraving the design onto cylinders and using them to transfer the ink onto the material. This method is often used for Printed BOPP Woven Bags.
- Screen Printing: While not as commonly used for large runs, screen printing offers a great solution for high-impact visuals. The ink is pushed through a mesh screen onto the bag material, making it a good option for smaller batches of custom prints with fewer colors.
- Offset Printing: Often used for high-quality, photographic prints, offset printing is a method where the design is transferred to a rubber blanket and then onto the woven bag. This allows for sharper images and fine detail, though it can be more costly for small runs.
- Digital Printing: A relatively newer technology in the woven bag industry, digital printing is gaining popularity for its ability to print high-resolution images directly onto bags without the need for printing plates. This method is best suited for smaller orders and customized designs with a variety of colors.
Customization Options to Meet Market Demands
As industries continue to evolve, so do the needs for packaging solutions. To ensure that Custom Printed Woven Bags meet the requirements of different markets, manufacturers offer a range of customization options. Below, we explore some of the most popular features that businesses choose to customize for their woven bags:
Customization Option | Description |
---|---|
Custom Valve Bags | Woven bags with a valve or spout for easy filling and secure sealing, often used in the agricultural and chemical industries. |
Custom Handles | Adding handles to bags increases their usability, making them easier to carry, ideal for retail or consumer products. |
Custom Openings | Custom openings allow for specialized packaging needs, such as bags with larger or smaller top openings for specific product types. |
Custom Sizes and Shapes | Tailoring the size and shape of the bags ensures compatibility with packaging systems or specific product requirements. |
Custom Thickness | Adjusting the thickness of the woven fabric ensures that the bags can withstand varying weight loads, perfect for bulk packaging. |
Custom Printed Patterns | Customized print designs, including logos, graphics, and brand names, help businesses create a distinct brand identity. |
Custom Materials | Different materials like BOPP laminates or kraft paper layers can be used for additional strength or for a sustainable alternative. |
Custom Valve Bags
Custom Valve Bags are a popular choice for products like fertilizers, grains, and chemicals. These bags feature a valve for easy filling and a secure seal to protect the contents. Manufacturers can customize the size and shape of the valve, as well as the material used for the bag itself, making them ideal for heavy-duty packaging.
Custom Handles
For retail products or consumer goods, Custom Handles provide convenience and ease of use. Handles can be added to Printed Woven Sacks to make them more user-friendly for consumers. These handles are often made from the same PP material or from a reinforced version to ensure durability during handling and transportation.
Custom Openings
Another important customization option is the size and shape of the bag’s opening. Custom Openings can be tailored to the specific product that is being packaged, such as larger openings for bulkier items or smaller openings for fine-grain products. This feature ensures that the bag is functional for its intended purpose while maintaining the strength and integrity of the woven fabric.
Custom Sizes and Shapes
Adjusting the Custom Size and Shape of woven bags is crucial for ensuring compatibility with packaging systems and product sizes. Whether you need a long, cylindrical bag for certain food products or a square-shaped bag for better stacking, manufacturers can customize the dimensions to suit your needs. Customizing the shape and size of the bag allows businesses to maximize space efficiency and reduce material waste during shipping.
Custom Thickness
The thickness of a bag plays a significant role in determining its strength. A Custom Thickness option allows businesses to tailor the woven bag to the weight of the product being packaged. Heavier products, such as chemicals or construction materials, require thicker bags to ensure that they do not tear or break during transport. On the other hand, lighter products can use thinner bags to optimize material costs without compromising durability.
Custom Printed Patterns
For businesses seeking to enhance their brand visibility, Custom Printed Patterns are a powerful tool. By customizing the print design, businesses can add logos, graphics, and branding elements to their woven sacks. This not only helps in establishing a unique identity but also makes the bags more visually appealing to customers. Digital printing and screen printing methods are often used to achieve high-quality, vibrant designs.
Custom Materials
Woven bags are typically made from polypropylene, but businesses may opt for Custom Materials like BOPP laminates or kraft paper. For eco-conscious companies, laminated options provide additional strength and protection while maintaining an environmentally friendly image. Additionally, different materials can be combined to meet specific functional needs, such as moisture resistance or UV protection.
Meeting Market Demands with Customized Woven Bags
The versatility of Printed Woven Bags allows businesses to meet the specific demands of various industries. From agriculture and construction to retail and food packaging, customized woven sacks provide a tailored solution that enhances both functionality and brand image.
By offering these customization options, businesses can align their packaging with the unique needs of their products and market requirements. With the ability to customize everything from bag size and thickness to printing design and material composition, manufacturers ensure that their packaging solutions provide both protection and promotion.
For businesses in search of high-quality Printed Woven Bags or seeking more information on customization options, this article offers a comprehensive guide on the advanced manufacturing processes available.