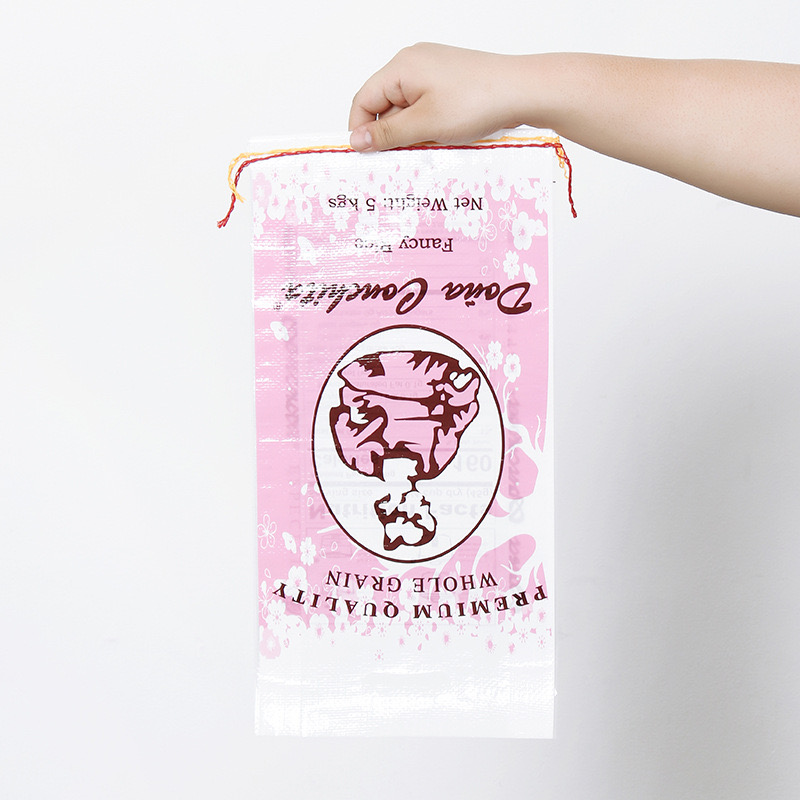
In industries around the world, packaging plays a pivotal role in ensuring that products are securely stored, transported, and delivered. Among the various types of industrial packaging materials, Industrial Woven Bags have proven to be one of the most reliable and cost-effective solutions. These bags, often made from high-density polypropylene (PP), offer a combination of strength, flexibility, and versatility that makes them an ideal choice for a wide range of applications.
With an increasing demand for efficiency in logistics, companies are continuously looking for ways to enhance the design of their packaging solutions. This has led to innovations in Industrial Packaging Bags, focusing on features that simplify handling and optimize storage. Specifically, designs like Valve Bags and Block Bottom Bags have gained significant popularity for their ability to improve the loading and unloading process, thereby increasing operational efficiency.
In this article, we will explore the unique benefits of Industrial PP Bags, Woven Bags, and PP Woven Sacks, and discuss how design innovations such as the Valve, Block Bottom, and other features are reshaping the industrial packaging landscape.
What Are Industrial Woven Packaging Bags?
Industrial Woven Bags are a type of durable packaging material that is woven from polypropylene fibers. These bags are designed to be strong enough to withstand the rigors of heavy-duty use, making them an ideal choice for industries that deal with bulk products. Industrial PP Bags, a subcategory of woven bags, are primarily used for packaging materials like sand, cement, grain, chemicals, and fertilizers.
The woven structure of these bags ensures that they are resistant to tearing, puncturing, and abrasion, while the polypropylene material makes them resistant to moisture, making them suitable for storing a variety of goods in diverse environments. One of the main advantages of these bags is their ability to be tailored to meet the specific needs of various industries, from agriculture to construction.
Industrial Packaging Sacks are another term commonly used to describe these woven bags. They are an essential part of the packaging solutions for bulk handling and storage. Their customizable designs, strong seams, and capacity to hold significant amounts of weight have made them a go-to choice for industrial operations.
For a more in-depth look at the applications and benefits of Industrial Packaging Bags, check out this detailed overview of the industry at Industrial Woven Packaging Bags.
Key Features of Industrial Woven Bags
There are several reasons why Industrial Woven Bags have become a staple in the packaging industry. Here are some of the most notable features:
- Strength and Durability:
The polypropylene material used in these bags makes them durable and resistant to stress, providing excellent protection during transport and storage. - Customizable Designs:
PP Woven Sacks can be tailored to different sizes, colors, and capacities, which allows for customization based on the specific needs of the product being packaged. - Breathability:
The woven design of these bags allows for ventilation, which is crucial for items like grains or seeds that need to breathe during storage. - Sustainability:
Many Industrial Woven Bags are recyclable, contributing to sustainable packaging solutions that align with corporate social responsibility goals. - Cost-Effectiveness:
These bags are an affordable option compared to other types of industrial packaging, offering significant cost savings for businesses that require large quantities of bags. - Environmental Resistance:
Woven bags are designed to withstand various environmental conditions, including exposure to moisture, UV rays, and dust.
These features make Industrial Woven Bags an optimal choice for many businesses, especially those dealing with heavy materials or requiring high-volume packaging solutions.
Design Innovations for Efficient Handling
As industries evolve, so does the demand for more efficient packaging. One of the most notable innovations in Industrial Woven Bags is the integration of features that simplify the loading and unloading process. Two of the most popular designs for this purpose are Valve Bags and Block Bottom Bags. These designs provide solutions that save time, reduce labor, and increase the overall efficiency of the packaging process.
Valve Bags: An Efficient Solution for Bulk Packaging
Valve Bags are a type of woven bag designed with a valve at the top for easy filling. The valve opening allows products to be filled into the bag quickly and securely without the need for additional labor to close the bag. This makes Valve Bags an ideal choice for packaging bulk materials such as flour, cement, fertilizers, and animal feed.
Some of the key benefits of Valve Bags include:
- Faster Filling: The valve system eliminates the need for manual labor in closing the bags, speeding up the packaging process.
- Reduced Product Loss: The tightly sealed valve prevents spills and leakage, ensuring that the contents remain inside the bag.
- Cost Savings: The automation of the filling process leads to significant savings in labor costs.
For an example of how Valve Bags enhance logistics efficiency, explore this article about optimizing packaging efficiency with pasted valve bags.
Block Bottom Bags: Improving Stability and Load Distribution
Block Bottom Bags are another innovation designed to make handling easier and more efficient. These bags have a square-shaped bottom, which allows them to stand upright on their own. This design improves the stability of the bags, making them easier to stack and store, reducing the risk of the bags toppling over during transport or storage.
Key benefits of Block Bottom Bags include:
- Enhanced Stability: The flat bottom ensures that the bag can stand upright, reducing the chances of the bag tipping over.
- Better Load Distribution: The square shape of the bottom allows for an even distribution of weight, making it easier to stack the bags and optimize storage space.
- Increased Storage Efficiency: Because the bags can stand on their own, they can be more efficiently loaded onto trucks or shelves, leading to better space utilization.
Product Specifications: Woven Bags for Diverse Needs
To further understand the capabilities of Industrial Woven Bags, let’s look at some typical product specifications that cater to a variety of industrial needs:
Feature | Standard Specification | Applications |
---|---|---|
Material | Polypropylene (PP) | Suitable for all types of bulk packaging |
Bag Type | Valve, Block Bottom, Open Mouth | Packaging of dry, granular, or powdery products |
Capacity | 10kg – 1000kg | Customizable based on product requirements |
Size | 30cm x 50cm to 90cm x 150cm | Varies depending on volume needs |
Design Customization | Color, Logo Printing, Reinforced Tops | Tailored for branding and durability |
Strength | 500 to 2500 Denier | Optimal for heavy-duty applications |
Environmental Resistance | Moisture Resistant, UV Protected | Long-term storage in various environments |
These specifications highlight the versatility of Woven Bags in meeting diverse industrial packaging needs. Whether you’re dealing with lightweight materials or heavy, bulk products, there is a suitable woven bag design that can handle the load.
Conclusion
The demand for efficient, durable, and sustainable packaging solutions continues to grow across industries. Industrial Woven Bags—especially Industrial PP Bags and PP Woven Sacks—offer a combination of strength, versatility, and customization that make them the preferred choice for many businesses.
Innovations in Valve Bags and Block Bottom Bags have significantly improved the efficiency of packaging, enabling faster filling and easier storage. With their ability to be tailored to various industries’ needs, these bags help companies reduce costs and improve the overall logistics process.
As industries evolve and face new challenges, Industrial Woven Bags continue to adapt, ensuring that businesses can meet growing demands while maintaining high standards of efficiency, sustainability, and cost-effectiveness.