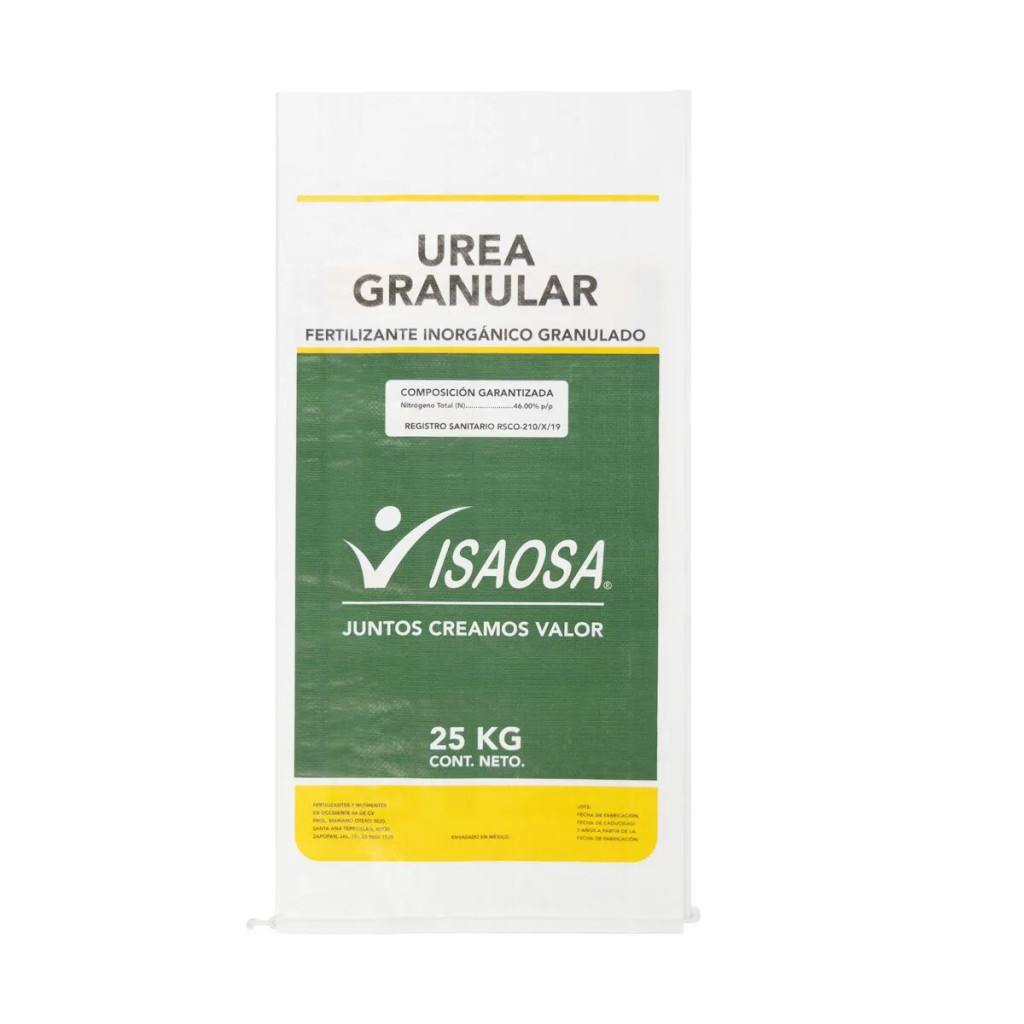
- Introduction
- Why Quality Testing Matters for Industrial Woven Bags
- Core Quality Tests for PP Granules in Industrial Woven Packaging Bags
- Specialized Testing for PE Liners in Industrial Packaging Sacks
- Technical Parameters of PP/PE Granules for Industrial Woven Bags
- Case Study: How Quality Testing Saved a Mining Giant $1.2M Annually
- Challenges in Raw Material Testing
- FAQs: Addressing Industry Concerns
- The Future: Automation in Quality Testing
- Conclusion
Key Answer: Rigorous quality testing of PP/PE raw materials—including physical, mechanical, thermal, and visual inspections—is essential to ensure the durability and compliance of industrial woven packaging bags.
Introduction
Industrial woven packaging bags, such as Industrial PP bags and PP woven sacks, are foundational to global logistics, agriculture, and construction. However, their performance hinges on the quality of raw materials—specifically polypropylene (PP) and polyethylene (PE) granules. This report analyzes the mandatory quality tests for PP/PE granules used in industrial woven bags, supported by data, case studies, and technical benchmarks.
Why Quality Testing Matters for Industrial Woven Bags
Industrial packaging sacks must withstand extreme conditions, from heavy loads in construction sites to prolonged UV exposure in agricultural fields. Substandard PP/PE granules lead to bag failures, costing industries millions annually. For example, a 2023 study by the International Packaging Institute found that 22% of woven bag supply chain disruptions stemmed from inconsistent raw material quality.
Dialogue:
Q: Why test PP granules before producing woven bags?
A: Industrial PP bags require uniform polymer properties to ensure tensile strength and UV resistance. Without testing, bags may tear during transport, risking product loss.
Core Quality Tests for PP Granules in Industrial Woven Packaging Bags
1. Basic Physical Property Testing
- Melt Flow Index (MFI): Measures polymer viscosity. For PP woven sacks, an MFI of 2–4 g/10 min (ASTM D1238) ensures optimal weaving machine compatibility.
Example: A Vietnamese manufacturer reduced production downtime by 35% after standardizing MFI for industrial PP bags. - Density: PP granules must have a density of 0.905–0.925 g/cm³. Higher density improves rigidity, critical for industrial packaging sacks carrying construction debris.
2. Mechanical Performance Testing
- Tensile Strength & Elongation: ASTM D638 tests reveal if PP films can endure stretching during weaving. For woven bags, tensile strength ≥30 MPa and elongation ≥500% are mandatory.
Case Study: A Colombian coffee exporter eliminated 15% of transport damage by switching to PP granules with 32 MPa tensile strength. - Impact Resistance: ASTM D256 tests ensure bags resist punctures. PP woven sacks storing sharp-edged minerals require impact strength ≥8 kJ/m².
3. Thermal Property Testing
- Heat Deflection Temperature (HDT): PP granules for industrial woven bags exposed to heat (e.g., Middle Eastern logistics) need HDT ≥100°C (ISO 75).
- Crystallization Temperature: Affects weaving efficiency. Optimal PP crystallization at 120–130°C minimizes fiber breakage.
4. Visual & Contaminant Inspection
- Color Consistency: Discolored PP granules lead to uneven dyeing in custom woven bags, harming brand aesthetics.
- Foreign Particles: X-ray fluorescence (XRF) scanners detect metal traces. In 2022, a Chinese supplier recalled 10,000 PP woven sacks due to iron contaminants damaging looms.
Specialized Testing for PE Liners in Industrial Packaging Sacks
PE liners in woven bags require additional tests:
- Film Impact Resistance: ASTM D1709 measures puncture resistance. PE liners for chemical powders need ≥400 g/mil impact strength.
Example: A Kenyan fertilizer company reduced leakage by 50% using PE films tested at 450 g/mil.
Technical Parameters of PP/PE Granules for Industrial Woven Bags
Parameter | PP Granules | PE Liners |
---|---|---|
Melt Flow Index (MFI) | 2–4 g/10 min | 0.2–2 g/10 min |
Tensile Strength | ≥30 MPa | ≥20 MPa |
Impact Resistance | ≥8 kJ/m² | ≥400 g/mil |
Heat Deflection Temperature | ≥100°C | ≥80°C |
Case Study: How Quality Testing Saved a Mining Giant $1.2M Annually
A Canadian mining company faced frequent ruptures in PP woven sacks transporting copper ore. After implementing ISO-compliant PP testing (focusing on MFI and tensile strength), bag failure rates dropped from 12% to 2%, saving $1.2M in replacement costs.
Challenges in Raw Material Testing
- Cost of Advanced Equipment: High-precision MFI testers cost $50,000–$100,000.
Solution: Partnerships with labs like SGS allow SMEs to outsource testing. - Inconsistent Global Standards: ASTM and ISO norms vary, complicating exports.
Example: A Thai woven bag exporter lost a EU contract due to non-compliant HDT ratings.
FAQs: Addressing Industry Concerns
Q1: How often should PP/PE granules be tested?
A: Batch testing is ideal. For high-volume producers like industrial PP bags manufacturers, weekly audits are recommended.
Q2: Can recycled PP granules meet industrial standards?
A: Yes, but only if MFI and tensile tests are enforced. VidePak’s 2024 trial achieved 28 MPa tensile strength using 30% recycled PP.
Q3: What happens if PE liners fail film impact tests?
A: Liners may rupture during filling. A Nigerian agrochemical firm reported 8% product loss due to untested PE films.
The Future: Automation in Quality Testing
AI-powered spectrometers and real-time MFI analyzers are revolutionizing PP/PE testing. For instance, VidePak’s automated system reduced testing time for industrial woven packaging bags by 60% in 2023.
Conclusion
Quality testing of PP/PE granules is non-negotiable for producing reliable industrial woven bags. By adhering to ASTM/ISO protocols and leveraging automation, manufacturers can mitigate risks, enhance compliance, and dominate markets demanding high-performance PP woven sacks.
External Links:
- Explore how Industrial PP Bags ensure compliance in construction waste management here.
- Learn about rigorous material control for Industrial Packaging Bags here.
This report cites methodologies from ASTM International, ISO standards, and case studies by the International Packaging Institute (2023).