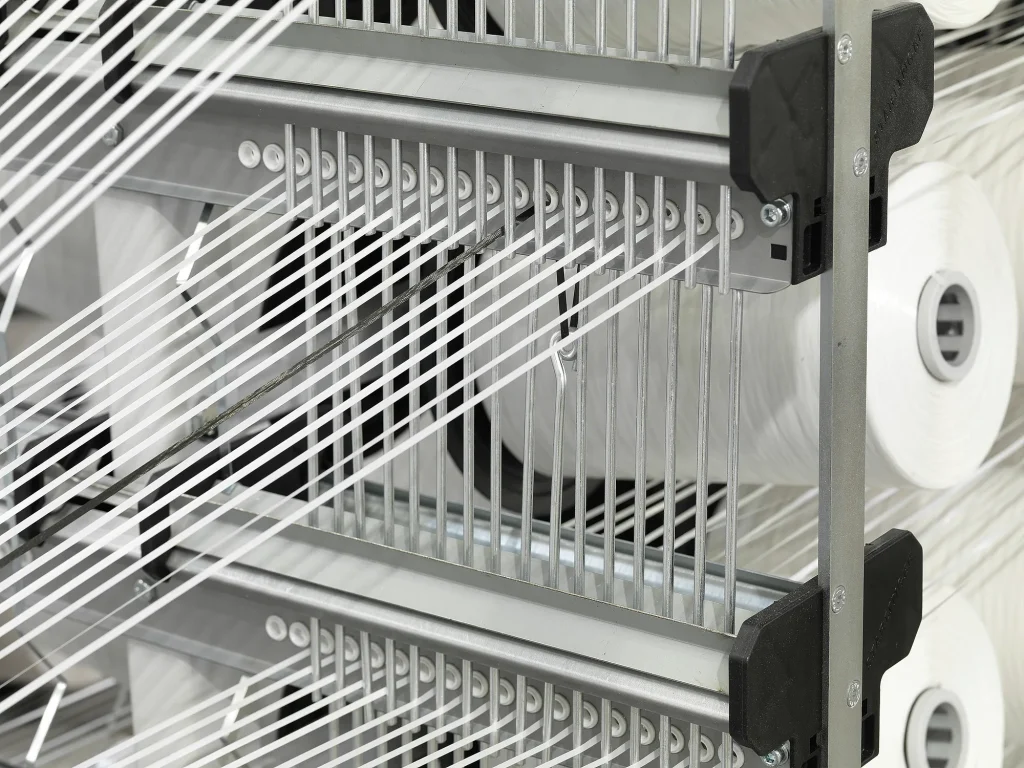
- 1. Historical Evolution: From Utility to Aesthetic Mastery
- 2. Material Engineering: Balancing Strength and Clarity
- 3. Customization: Tailoring Solutions for Diverse Markets
- 4. Functional Advantages Over Traditional Packaging
- 5. FAQs: Addressing Procurement Concerns
- 6. VidePak’s Technological Leadership
- References
Imagine a conversation between a retail packaging manager and a materials engineer:
Manager: “We need packaging that showcases our premium coffee beans while withstanding humid climates. What’s the solution?”
Engineer: “Transparent woven PP bags with UV-resistant lamination are your answer—they offer 92% light transmission for product visibility and reduce moisture ingress by 95%, extending shelf life by 18 months. For instance, VidePak’s 120 g/m² BOPP-laminated bags prevent fungal growth even at 85% humidity, ideal for Southeast Asian markets.”
Manager: “Can we add custom handles for retail convenience?”
Engineer: “VidePak’s 30+ lamination machines integrate reinforced handles and QR codes seamlessly, supporting 8-color HD printing (ΔE <1.5) for brand differentiation. Let’s explore why transparent woven bags redefine modern packaging.”
1. Historical Evolution: From Utility to Aesthetic Mastery
Transparent woven polypropylene (PP) bags emerged in the early 2000s as a hybrid solution, combining the durability of traditional woven sacks with consumer demand for product visibility. Initially used for agricultural bulk storage, advancements in Austrian Starlinger circular loom technology enabled ultra-fine 1.8–2.3 mm filaments, achieving fabric densities of 160 threads/inch for smoother surfaces and enhanced transparency. By 2025, the global transparent packaging market is projected to reach $65 billion, driven by food, retail, and pharmaceutical sectors prioritizing both functionality and aesthetics.
VidePak, leveraging 30+ years of expertise, pioneered BOPP (Biaxially Oriented Polypropylene) lamination in 2015, reducing water vapor transmission rates (WVTR) to <5 g/m²/24h. This innovation transformed transparent bags from simple storage tools into premium branding vehicles, aligning with FDA and EU REACH standards for direct food contact.
2. Material Engineering: Balancing Strength and Clarity
Modern transparent woven bags rely on multi-layer architectures:
- Layer 1: 80 µm BOPP film (UV-resistant, WVTR <2 g/m²/24h).
- Layer 2: Woven PP fabric (1.8–2.3 mm filaments, tensile strength 35–50 N/cm²).
- Layer 3: Anti-static PE liner (surface resistivity <10⁹ Ω, critical for flammable powders).
Case Study: A Chilean coffee exporter reduced spoilage losses by 25% using VidePak’s 5-layer AlOx-coated bags, which block 99% UV radiation while maintaining 90% transparency for retail appeal.
3. Customization: Tailoring Solutions for Diverse Markets
VidePak’s 100+ Starlinger looms and 30 printing machines enable unparalleled customization:
Feature | Technical Specifications | Applications |
---|---|---|
Valve Design | Pneumatic filling ports (ISO 9001-certified) | Industrial powders, pet food |
Handles | Reinforced PP straps (load capacity 15 kg) | Retail-ready consumer goods |
Printing | 8-color HD flexography (Pantone-matched) | Branded pharmaceuticals, luxury items |
Thickness | 0.5–2.0 mm (adjustable per ASTM D5265) | Heavy-duty minerals vs. lightweight grains |
Anti-Microbial | Silver-ion additives (99% E. coli inhibition) | Animal feed, medical supplies |
Example: A European cosmetics brand boosted sales by 30% using VidePak’s pearlized transparent bags with QR codes for traceability, complying with EU Circular Economy mandates.
4. Functional Advantages Over Traditional Packaging
Transparent woven bags outperform alternatives in key metrics:
- Cost Efficiency: 40% lighter than glass containers, reducing shipping costs by 18%.
- Durability: Withstand 1.5-ton stack loads vs. paper bags’ 500 kg limit.
- Sustainability: 20% recycled PP content, decomposing in 3–5 years with oxo-additives.
5. FAQs: Addressing Procurement Concerns
Q1: How do I choose between 90 g/m² and 120 g/m² fabrics?
A: Opt for 90 g/m² for lightweight grains (e.g., rice); 120 g/m² with BOPP lamination suits hygroscopic products like fertilizers.
Q2: Can bags withstand freezer storage (-20°C)?
A: Yes. Copolymer PP blends retain flexibility at -30°C (tested per ASTM D746).
Q3: What’s the MOQ for custom designs?
A: 10,000 units with 15-day lead time, including ISO 22000 compliance testing.
6. VidePak’s Technological Leadership
With 16 extrusion lines and 100+ circular looms, VidePak delivers:
- Precision: ±0.1 mm seam tolerance for hermetic sealing.
- Scalability: 5,000 bags/hour production, serving 50+ countries.
- Innovation: Pilot testing self-healing films with microcapsule technology for puncture resistance.
Explore our customizable valve bags for industrial powders or BOPP laminated designs for retail brilliance.
References
- VidePak Company Profile: https://www.pp-wovenbags.com/
- ASTM International. (2025). Standard Specifications for Polypropylene Films.
- EU Circular Economy Action Plan 2030.
- Contact: info@pp-wovenbags.com
Anchor Links
- Discover our transparent woven bags with custom printing here.
- Learn about heavy-duty valve bag solutions here.
This guide synthesizes decades of industry expertise, cutting-edge engineering, and VidePak’s global leadership to empower your transition to smarter, visually impactful packaging solutions.