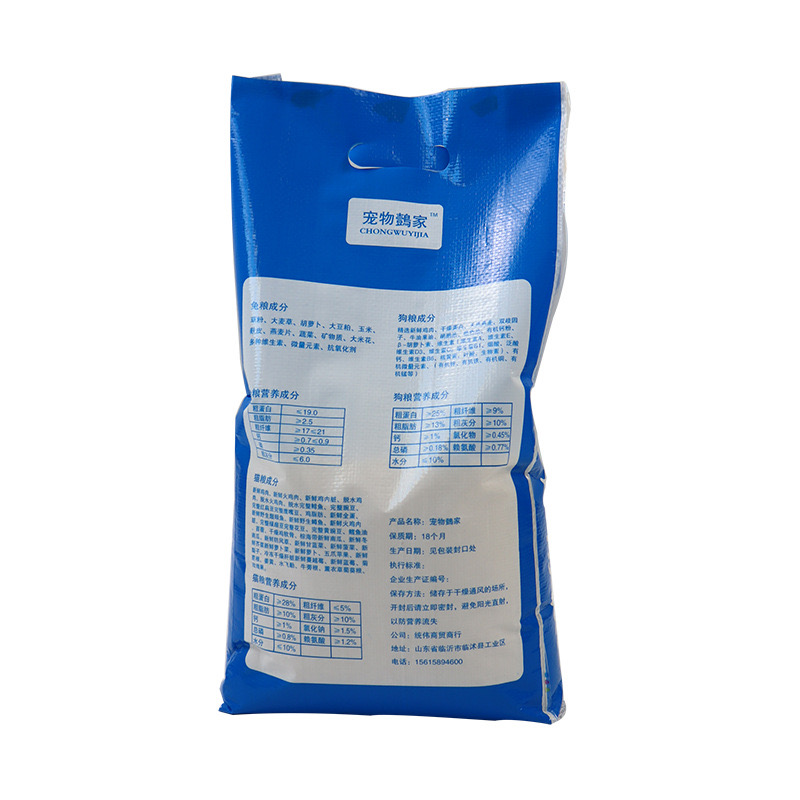
- What Are Transparent Woven Bags?
- The Role of Drawing Technology in Bag Durability and Flexibility
- Automation and Efficiency in Production
- Table: Key Product Parameters for Transparent Woven Bags
- Advantages of HDPE and Polypropylene in Woven Bags
- The Impact of Starlinger and W&H Equipment on Quality Control
- The Global Impact of Transparent Woven Bags and the Future of HDPE Bags
The increasing demand for sustainable packaging solutions has driven the growth of Transparent Woven Bags in various industries. From agriculture to manufacturing, these bags offer clear visibility and high durability, making them an excellent choice for numerous applications. This article will explore the advantages of Transparent Woven Sacks, the impact of drawing technology on the durability and flexibility of these bags, and how the use of high-end equipment from Austrian Starlinger and German W&H ensures superior quality and efficiency in production. Additionally, we will delve into how HDPE Woven Bags are evolving and how these innovations influence the competitive landscape of the woven bag manufacturing industry.
In the manufacturing process, transparent woven bags are produced using advanced technologies, including the HDPE Bags material that offers superior strength and transparency. The efficiency of the production process is highly influenced by the equipment used, with automation and advanced drawing processes being key to improving performance. The collaboration between Starlinger and W&H provides the backbone of these innovations, with their equipment offering automated solutions that achieve speeds of over 200 meters per minute, ensuring not only high-quality products but also maximum efficiency.
What Are Transparent Woven Bags?
Transparent Woven Bags are made from high-density polyethylene (HDPE) or polypropylene (PP), woven into a fabric structure that is both strong and lightweight. These bags offer several advantages over traditional packaging options. Their transparency allows for the easy identification of contents, making them ideal for applications such as packaging agricultural products, grains, seeds, and retail items. Additionally, these bags are highly resistant to tearing, punctures, and environmental factors like UV exposure, which makes them a durable choice for various industrial applications.
These bags are primarily used in industries where product visibility is important for consumer confidence and efficient inventory management. For instance, HDPE Woven Bags are widely used in the food packaging sector, where it is essential for consumers to see the quality of the product within.
The Role of Drawing Technology in Bag Durability and Flexibility
One of the critical factors in the performance of woven bags is the process known as drawing. The drawing process involves the stretching of the polymer film during manufacturing, which increases the tensile strength and flexibility of the material. This process directly impacts the durability and flexibility of the finished Transparent Woven Bags.
Drawing technology is essential for improving the strength-to-weight ratio of the material. This not only enhances the load-bearing capacity of HDPE Woven Bags but also allows for more sustainable usage of raw materials. As the drawing process aligns the polymer chains, the bags are made more resistant to tearing, punctures, and other stresses that could compromise their structural integrity.
In addition to increasing the mechanical strength of the bags, the drawing process also plays a vital role in improving their elasticity. This allows HDPE Bags to be more flexible and resistant to breaking under pressure, which is a key requirement for many applications where the bags may need to withstand rough handling or transportation over long distances.
Automation and Efficiency in Production
At the heart of this technological evolution in woven bag manufacturing lies the automation provided by leading equipment manufacturers like Starlinger and W&H. These companies have integrated advanced automation systems that ensure precision and efficiency in the production of Transparent Woven Bags. With automated processes, production rates can exceed 200 meters per minute, significantly increasing the efficiency and output of the manufacturing lines.
The use of high-speed machinery in tandem with multi-machine coordination also ensures that production is streamlined and that quality control measures are consistently met. This level of automation minimizes human error, reduces production time, and helps manufacturers meet the growing demand for transparent and durable woven bags. The enhanced capacity to produce large volumes without compromising quality is a major competitive advantage for manufacturers in the global market.
Starlinger’s and W&H’s technology also integrates innovative systems for managing material inputs, ensuring that the bags are made from high-quality raw materials that meet strict international standards. This focus on automation and precision is crucial in maintaining the consistency of bag production and meeting customer demands for customized sizes, printing, and design.
Table: Key Product Parameters for Transparent Woven Bags
Parameter | Transparent Woven Bags |
---|---|
Material | HDPE, PP, or blend of both |
Thickness | 40 – 200 microns (customizable) |
Bag Type | Open-mouth, Valve, Gusseted |
Printing | Multi-color, Customizable |
Strength | 10 – 25 kg (depending on the bag type and size) |
UV Resistance | High |
Transparency | 80% – 100% (depending on customer requirements) |
Heat Resistance | High (suitable for use in extreme environments) |
Bag Capacity | From 5 kg to 1000 kg |
Production Speed | Over 200 meters/minute (high automation) |
As indicated in the table, the production process and the quality of the material significantly impact the end product’s durability, flexibility, and overall performance.
Advantages of HDPE and Polypropylene in Woven Bags
HDPE Woven Bags offer several benefits that make them ideal for various industries. First, their HDPE composition gives them superior strength and resistance to wear, which is crucial when bags are used for heavy-duty applications. The high tensile strength of HDPE Woven Bags ensures that these bags can carry large loads without breaking. Moreover, HDPE Bags are resistant to chemicals and moisture, making them suitable for agricultural, chemical, and construction packaging.
Additionally, HDPE Woven Bags are highly sustainable due to their recyclability. The material can be reused, reducing the environmental footprint of packaging solutions. This sustainability is further enhanced by the use of advanced production techniques, which ensure that the bags are manufactured with minimal waste and energy consumption.
The Impact of Starlinger and W&H Equipment on Quality Control
The precision and reliability of the production process are largely dependent on the equipment used. Both Starlinger and W&H are renowned for their state-of-the-art machinery, which incorporates automated systems for monitoring and adjusting parameters such as tension, temperature, and film thickness during production. This ensures that every Transparent Woven Bag meets the required specifications and maintains a consistent level of quality.
These machines also integrate advanced quality control mechanisms that perform real-time inspections during the manufacturing process. This allows manufacturers to detect any issues early on, reducing the chances of defective bags reaching the customer. Furthermore, these systems help maintain the integrity of the bags’ transparency, strength, and flexibility, ensuring that the final product meets the highest standards.
The combination of high automation, precise control systems, and top-quality raw materials results in Transparent Woven Bags that are both cost-effective and reliable for various industrial applications.
The Global Impact of Transparent Woven Bags and the Future of HDPE Bags
As industries continue to seek more sustainable, efficient, and cost-effective packaging solutions, Transparent Woven Bags and HDPE Woven Bags are expected to play a growing role in the global market. With the increase in environmental awareness, more companies are turning to eco-friendly packaging alternatives, and woven bags offer a sustainable choice without compromising performance.
In the coming years, the demand for transparent woven bags will likely increase as consumers continue to value product transparency, particularly in industries like food packaging and retail. Manufacturers that embrace advanced technologies from Starlinger and W&H will be better positioned to meet these growing demands while maintaining high standards of quality, durability, and efficiency.
For more information on Transparent Woven Bags, please refer to this link. Additionally, to learn more about the performance and benefits of HDPE Woven Bags, visit this article.