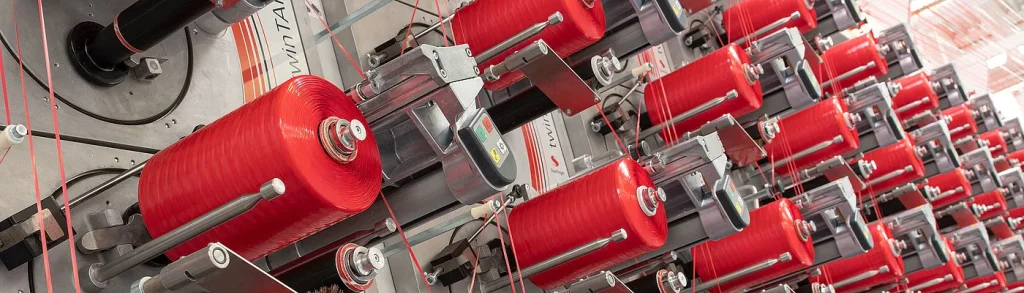
Imagine a conversation between a packaging engineer and a procurement manager:
Procurement Manager: “We need durable, cost-effective bags for our fertilizer exports. What’s the best solution?”
Engineer: “Open mouth PP woven bags are the answer—they’ve evolved from basic sacks in the 1960s to high-tech solutions today. But choosing the right polypropylene (PP) grade and additives is critical. For example, UV-resistant PP with antioxidants ensures longevity under harsh sunlight, aligning with ASTM D7191 standards for U.S. markets.”
Procurement Manager: “How do we balance compliance and cost?”
Engineer: “VidePak’s 30+ years of expertise in global standards ensures tailored solutions. Their Starlinger equipment produces 100 million bags annually, meeting EU REACH, JIS Z 1539, and GB/T 8946 certifications. Let’s dive deeper.”
1. Historical Evolution: From Simplicity to Sophistication
Open mouth PP woven bags emerged in the 1960s as a lightweight alternative to jute and paper sacks. Their key innovation lay in polypropylene’s high tensile strength (30–40 g/denier) and moisture resistance. By the 1980s, advancements in extrusion and circular loom technology enabled mass production, with global demand surging to 12 million metric tons annually by 2025.
VidePak, founded in 2008, capitalized on this growth. Leveraging CEO Ray Chiang’s 30-year industry experience, the company integrated Austrian Starlinger machines to achieve precision in weaving (120–160 threads/inch) and lamination (20–100 µm thickness), ensuring compliance with ISO 9001 and FDA standards for food-grade packaging.
2. Selecting PP Grades: Aligning with International Standards
Choosing the right PP resin is pivotal. Below is a comparative analysis of global standards:
Standard | Region | Key Requirements | Recommended PP Grade |
---|---|---|---|
ASTM D7191 | USA | UV stability, tear resistance | Homopolymer PP (MFI 4–8 g/10min) |
EN 15534 | EU | Recyclability, elongation >400% | Copolymer PP (MFI 2–4 g/10min) |
JIS Z 1539 | Japan | Heat resistance, low odor | Nucleated PP (MFI 6–10 g/10min) |
GB/T 8946 | China | Tensile strength >35 N/cm² | High-crystallinity PP |
Why It Matters:
- Homopolymer PP (e.g., ExxonMobil PP1105K) offers rigidity for stacking, ideal for 25–50 kg agricultural products.
- Copolymer PP (e.g., Borealis BCP 7725) enhances flexibility for fragile goods like ceramics, complying with EU’s circular economy mandates.
- Additives:
- UV inhibitors (e.g., HALS) extend lifespan by 50% in tropical climates.
- Antioxidants (e.g., Irganox 1010) prevent thermal degradation during extrusion (180–240°C).
VidePak uses 100% virgin PP to avoid contaminants, critical for FDA-compliant food packaging. Their R&D team tailers formulations to regional climates—e.g., adding 1.5% carbon black for Middle Eastern clients to block UV radiation.
3. Modern Applications: Versatility Meets Innovation
Open mouth PP bags now serve industries from agriculture to pharmaceuticals:
- Agriculture: 50 kg laminated bags with anti-slip coating for rice exports (moisture barrier: <5 g/m²/24h).
- Chemicals: PE-lined bags with static dissipation (<10⁹ Ω) for flammable powders.
- Retail: 5–10 kg bags with 8-color HD printing for branding.
Case Study: A Chilean fertilizer producer reduced transport losses by 20% after switching to VidePak’s BOPP-laminated bags (burst strength >45 psi), certified to ISO 22000 for hazardous materials.
4. FAQs: Addressing Procurement Concerns
Q1: How does VidePak ensure compliance with multiple standards?
A: Our labs test every batch for MFI, tensile strength, and UV resistance. Certificates include UKCA, CE, and RoHS.
Q2: Can bags withstand maritime shipping?
A: Yes. Our anti-UV PP retains 90% strength after 1,000 hours of QUV testing, exceeding ASTM G154.
Q3: What customization options exist?
A: Choose from 30+ Pantone colors, PE/PP liners, and sizes up to 100 cm × 120 cm.
5. VidePak’s Technological Edge
With 100+ circular looms and 30+ lamination machines, VidePak achieves:
- High throughput: 5,000 bags/hour per production line.
- Precision printing: Flexographic presses with ≤0.1 mm registration error.
- Sustainability: 20% recycled PP in eco-lines, reducing carbon footprint by 15%.
Explore our FIBC bulk bags for heavy-duty logistics or custom-printed valve bags for niche markets.
References
- VidePak Company Profile: https://www.pp-wovenbags.com/
- ASTM International. (2023). Standard Specification for Polypropylene Films.
- European Committee for Standardization. (2022). EN 15534: Composites Made from Cellulose-Based Materials.
- Contact: info@pp-wovenbags.com
Anchor Links
This article synthesizes technical expertise, market insights, and VidePak’s operational excellence to position your brand as a leader in PP packaging solutions.