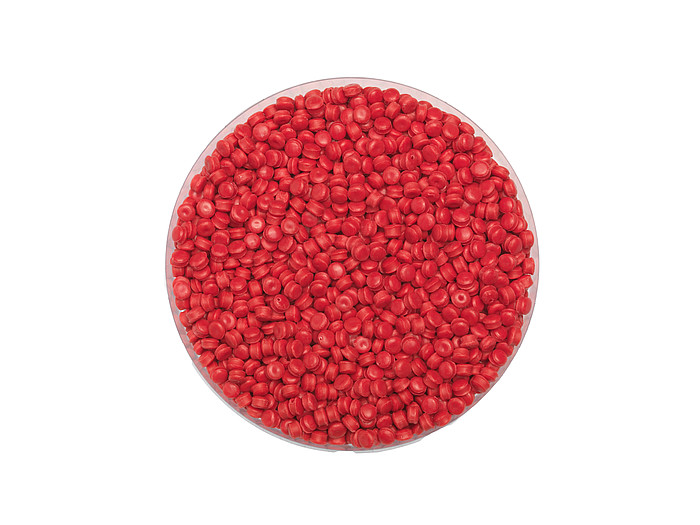
Food-grade woven bags have become essential in the packaging industry, especially for bulk food products like grains, flour, and animal feed. Over the years, these bags have evolved in response to changing consumer demands, regulations, and environmental considerations. VidePak, a leading name in this field, has continually embraced innovation and technology to improve the quality and functionality of food-grade woven bags. This article takes a closer look at the evolution of these bags, the technology behind them, and VidePak’s commitment to excellence.
The Evolution of Food-Grade Woven Bags
In the past, woven bags were mostly made from natural fibers, which provided basic strength but lacked the durability and protection needed for modern food packaging. With the advancement of synthetic fibers like polypropylene (PP), food-grade woven bags have become much stronger, more durable, and resistant to moisture and contamination.
Today, these bags are commonly laminated with an additional layer of material like BOPP (Biaxially Oriented Polypropylene), providing an extra barrier to moisture and dirt. For example, a BOPP laminated woven bag can keep products like flour dry and free from contamination during storage and transport. This is especially crucial for food packaging, where hygiene is a top priority.
Key Manufacturing Techniques for Food-Grade Woven Bags
The way food-grade woven bags are made directly impacts their strength, protection, and usability. Let’s explore the most common manufacturing methods and why they matter.
1. Sealing Methods: Bottom Seam, Heat Seal, and Ultrasonic Welding
A strong seal is essential to keeping food products safe and secure. Different sealing techniques are used, each with its own advantages.
- Bottom Seam: This traditional method involves stitching the bag’s bottom. While it works well for lighter products, it may not be as airtight as other methods. For example, when packaging products like rice or grains, a well-stitched seam ensures that the bag stays intact during transportation.
- Heat Sealing: Heat sealing uses heat to bond the edges of the bag, making it airtight. This method provides a cleaner and more durable seal compared to stitching. It’s ideal for food products that need to be sealed tightly, such as sugar or powdered ingredients, which must stay dry and free from contaminants.
- Ultrasonic Welding: A more advanced technique, ultrasonic welding uses sound waves to create strong, seamless bonds between the bag’s layers. This method eliminates the risk of weak seams and provides a completely sealed package. It is particularly useful for BOPP laminated woven bags, which require superior sealing to protect sensitive food products like flour and spices from moisture and air.
2. Material and Stitching: Quality Matters
The choice of stitching material and the density of the stitches are also key to the bag’s strength. Food-grade bags must be able to withstand the weight and pressure of the product inside without breaking open.
- Stitching Material: Nylon and polyester are commonly used for stitching. Nylon is especially durable and can handle heavy-duty applications, such as packaging animal feed or bulk grains. Polyester, while less durable than nylon, is still a good choice for lighter bags like those used for flour or sugar.
- Stitch Density: The number of stitches per inch also affects the bag’s durability. A higher stitch density means a stronger bag. For instance, a high-stitch-density bag used for grain packaging can handle the weight and friction of bulk handling without tearing.
3. Bag Opening Designs: Open Mouth, Valve, Heat Seal, and Sewn
The design of the bag’s opening is critical in ensuring efficient filling and sealing. Different designs are suited to different types of food products.
- Open Mouth: This is the simplest design, where the bag’s top is open for easy filling. While this design is cost-effective and widely used for dry food items like rice or flour, it often requires additional sealing after filling. For example, after filling an open-mouth bag with sugar, the top needs to be securely sealed to prevent contamination and spillage.
- Valve Bags: These bags have a built-in valve that allows for easy filling and self-sealing. Valve bags are ideal for bulk items like flour and sugar that need to be sealed tightly. They provide a more efficient sealing solution than open-mouth bags, reducing the risk of contamination during transport.
- Heat-Sealed Bags: For products requiring extra protection from moisture and contaminants, heat-sealed bags are ideal. For example, coffee beans or snack foods require airtight seals to preserve freshness, and heat-sealed bags are the best option for this type of packaging.
- Sewn Bags: Sewn openings are common for food bags that don’t need to be completely airtight, like animal feed. The sewing technique ensures that the bag stays intact while allowing some air flow. The strength of the stitching is critical here, as any weak points could cause leaks.
VidePak’s Commitment to Excellence
At VidePak, we prioritize quality, safety, and innovation. By using advanced technologies like ultrasonic welding and heat-sealing, we ensure that our food-grade woven bags provide optimal protection for food products. For instance, our BOPP laminated woven bags offer superior moisture resistance and durability, making them perfect for packaging sensitive products like flour and spices.
Moreover, we understand the importance of sustainability in today’s market. That’s why we offer recycled polypropylene options, ensuring that our food-grade woven bags are not only strong and reliable but also environmentally friendly. Our commitment to eco-friendly solutions reflects the growing demand for sustainable packaging in the food industry.
Key Parameters and FAQs
Feature | Description |
---|---|
Material | Woven polypropylene (PP) and BOPP laminated options |
Strength | High tensile strength with options for heat sealing, ultrasonic welding |
Capacity | Customizable from 5kg to 50kg depending on product needs |
Opening Type | Open mouth, valve, heat-sealed, sewn |
Customization | Available in multiple sizes, colors, and prints |
Sustainability | Recycled PP options available |
FAQs
1. What makes food-grade woven bags different from other types of woven bags?
Food-grade woven bags are made from high-quality PP or BOPP materials that are designed to meet hygiene and safety standards. They are durable, moisture-resistant, and provide an extra layer of protection for food products.
2. What is the best sealing method for food-grade woven bags?
Heat sealing and ultrasonic welding provide the best seals for food-grade bags. These methods ensure airtight seals, reducing the risk of contamination and preserving the quality of the product inside.
3. Can food-grade woven bags be customized?
Yes, food-grade woven bags can be customized to meet your specific requirements, including size, color, and branding. VidePak offers full customization to suit your packaging needs.
4. Are VidePak’s food-grade woven bags environmentally friendly?
Yes, we offer recycled polypropylene options and environmentally friendly coatings, making our food-grade woven bags a sustainable choice for food packaging.
Conclusion
Food-grade woven bags have come a long way, with innovations in materials, manufacturing techniques, and sustainability shaping the future of the packaging industry. VidePak remains at the forefront of these advancements, offering high-quality, durable, and eco-friendly solutions for food packaging. Whether you need a heat-sealed, valve, or BOPP laminated bag, VidePak has the expertise to deliver packaging that ensures the safety and quality of your food products.