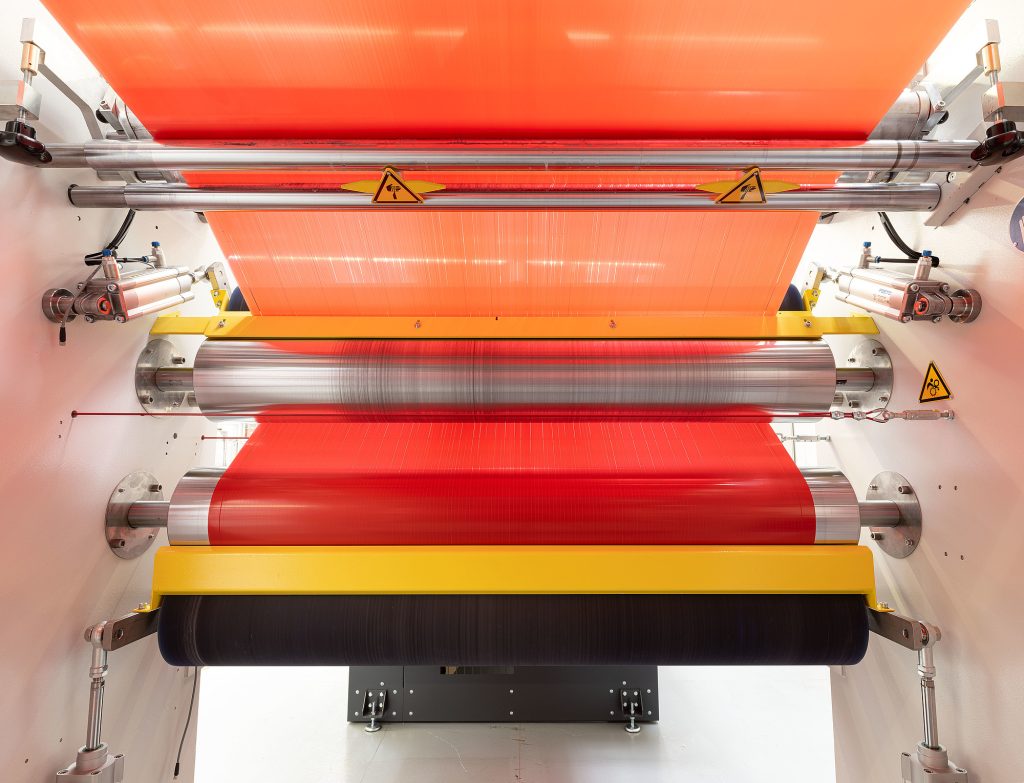
“In the world of industrial packaging, HDPE woven bags are no longer just sacks—they’re engineered solutions that balance strength, sustainability, and smart economics,” asserts Ray, CEO of VidePak, during a factory tour. This report demonstrates how HDPE woven fabric bags, driven by advancements in fine-fiber weaving technology and material science, are revolutionizing chemical, agricultural, and construction logistics while aligning with global cost-efficiency imperatives. By dissecting innovations in high-density weaving, additive engineering, and circular economy practices, we reveal why these bags are pivotal to modern supply chains.
1. Fine-Fiber Weaving Technology: Redefining Structural Integrity
1.1 The Science Behind Fine-Fiber Weaving
Fine-fiber weaving involves extruding high-density polyethylene (HDPE) into ultra-thin filaments (20–30 µm diameter) and weaving them into fabrics with densities up to 16×16 strands per square inch. VidePak’s Starlinger circular looms achieve this precision by maintaining tension at 15–20 N/cm and extrusion temperatures of 200–220°C, ensuring filament uniformity.
Key Advantages:
- Enhanced Tensile Strength: Fine-woven HDPE fabrics achieve tensile strengths of 28–32 N/mm² (ASTM D5035), 30% higher than conventional 8×8 weaves.
- Leakage Prevention: Reduced pore size (<0.1 mm) minimizes particle escape, critical for powders like titanium dioxide or sodium carbonate.
- Aesthetic Refinement: Smoother surfaces enable high-definition printing, boosting brand visibility.
Case Study: A 2024 trial with a Chinese chemical firm showed VidePak’s 16×16 weave bags reduced silica dust leakage by 85%, complying with EU REACH particulate limits.
2. Material Innovations: Balancing Performance and Compliance
2.1 HDPE Resin Selection for Global Markets
HDPE grades are selected based on regional standards:
- ASTM D4976 (U.S.): Requires melt flow index (MFI) of 0.5–1.0 g/10 min and density ≥0.945 g/cm³ for chemical resistance.
- EN ISO 1872-1 (EU): Mandates UV stabilization (≥1,000 hrs xenon arc testing) and oxidative induction time (OIT) >25 min.
- JIS K6745 (Japan): Prioritizes recyclability ≥95% (ISO 15270) and heavy metal content <50 ppm.
VidePak’s virgin HDPE resins incorporate hindered amine light stabilizers (HALS) and phosphite antioxidants, extending outdoor lifespan to 5+ years in harsh climates.
2.2 Additive Engineering for Specialized Applications
Additive Type | Function | Compliance |
---|---|---|
Carbon-Black Masterbatch | Anti-static properties | ANSI/ESD S20.20 |
UV Stabilizers | Prevents polymer degradation | EU REACH, RoHS |
Anti-block Agents | Reduces film adhesion | FDA CFR 21 |
3. Cost Efficiency: Scaling Production with Sustainability
3.1 Advanced Manufacturing at VidePak
With 100+ Starlinger looms and 30 lamination machines, VidePak produces 50 million HDPE bags annually. Key cost-saving strategies include:
- Solar-Powered Production: A 2 MW rooftop solar system reduces energy costs by 40% and CO₂ emissions by 1,200 tons/year.
- Closed-Loop Recycling: Post-consumer HDPE is reprocessed into non-woven geotextiles, diverting 800+ tons of waste annually.
3.2 Economic Analysis: Fine-Weave vs. Conventional Bags
Parameter | Fine-Weave HDPE Bags | Conventional Bags |
---|---|---|
Material Cost | $0.25–$0.35/bag | $0.18–$0.25/bag |
Lifespan | 5 years | 2–3 years |
Leakage-Related Losses | <5% | 15–20% |
ROI (5-year) | 200% | 120% |
4. Regulatory Alignment and Future Trends
4.1 Global Standards and Certification
- EU Circular Economy Package: Requires 55% recycled content in packaging by 2030, driving demand for VidePak’s HDPE-PLA hybrids.
- U.S. EPA Guidelines: Incentivize bags with <1% chemical migration, achievable via HDPE’s inert structure.
4.2 Emerging Technologies
- Smart Bags: RFID tags for real-time moisture/pH monitoring (piloted in VidePak’s ChemGuard series).
- Bio-Based HDPE: Partnerships with biotech firms to develop 30% plant-derived resins, reducing carbon footprint by 25%.
5. FAQs: Addressing Industry Concerns
Q1: How does fine-fiber weaving improve load capacity?
A: Higher strand density distributes stress evenly, enabling 1-ton FIBC jumbo bags to withstand dynamic loads without bulging (tested per ASTM D5264).
Q2: Are recycled HDPE bags viable for corrosive chemicals?
A: VidePak’s virgin-recycled blends retain 90% of virgin HDPE’s chemical resistance (pH 2–12) while meeting EN 13432 compostability standards.
Conclusion
HDPE woven bags exemplify the synergy of technological precision and ecological responsibility. By mastering fine-fiber weaving, optimizing material science, and embracing circular economies, VidePak is redefining industrial packaging as a driver of efficiency and sustainability. As Ray concludes, “Our bags aren’t just containers—they’re blueprints for a smarter, greener supply chain.”
External Links:
- Explore how eco-friendly HDPE bags align with ESG goals for sustainable logistics.
- Learn about polypropylene compliance frameworks to enhance regulatory alignment.
References:
- ASTM International, Standard Specification for Polyethylene Plastics (D4976)
- European Committee for Standardization, Plastics—Polyethylene (PE) Moulding and Extrusion Materials (EN ISO 1872-1)
- Japan Industrial Standards, Polyethylene Pipes (JIS K6745)