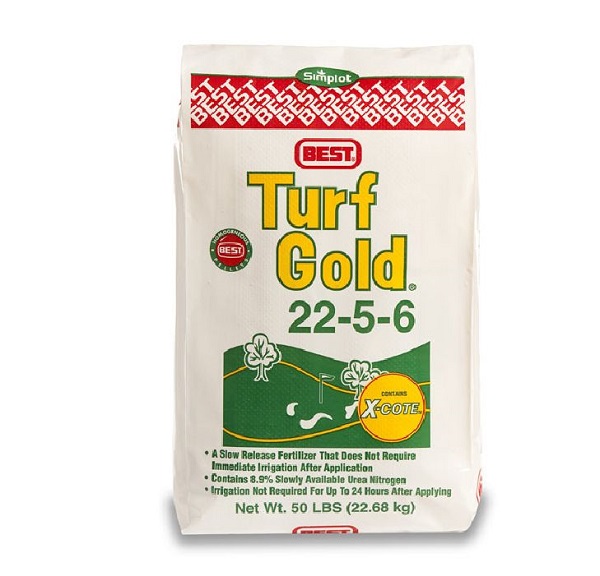
Polypropylene bags, or PP bags, have been at the heart of packaging solutions for a variety of industries due to their remarkable strength, versatility, and cost-effectiveness. With the growing demand for more sustainable and efficient packaging solutions, the polypropylene sacks market has witnessed significant technological advancements in both material science and manufacturing techniques. In this article, we will explore the evolution of PP woven bags, focusing on their technological improvements, material innovations, and the increasing role of automation in reducing costs and enhancing efficiency.
The Rise of Polypropylene Bags
Introduction to Polypropylene Bags
Polypropylene bags are widely used for packaging goods ranging from food products to construction materials, fertilizers, and even pet food. These woven bags are manufactured using polypropylene, a synthetic polymer that offers several advantages such as high tensile strength, resistance to chemicals, and durability under various environmental conditions.
Polypropylene sacks have evolved from simple woven products to advanced, multi-layered packaging solutions. The continuous improvements in materials and technology have helped manufacturers meet the changing needs of industries, particularly in packaging bulk goods.
Key Benefits of Polypropylene Bags
- Durability: Polypropylene woven bags are strong, making them ideal for transporting heavy loads.
- Lightweight: They are much lighter than traditional paper sacks or plastic bags, reducing shipping costs.
- Cost-effective: The production of PP bags is generally inexpensive, making them accessible for industries across the globe.
- Customizable: Manufacturers can offer various customization options, such as printing and sizing, to meet specific packaging needs.
- Sustainability: Many PP woven bags are now made from recycled materials, and the bags themselves are recyclable, making them an eco-friendly option for businesses.
Technological Advancements in Polypropylene Bags
Over the years, significant improvements have been made in the technology used to produce PP woven bags, increasing their strength, versatility, and functionality. Below, we discuss key advancements in material innovation and manufacturing processes.
1. Materials Innovation: Moving Beyond Basic Polypropylene
While standard PP woven bags are made from simple polypropylene fibers, manufacturers have begun using higher-grade materials, including multi-layer films and blends of polypropylene and polyethylene (PE). These innovations improve the bags’ strength and resistance to environmental factors, such as moisture and UV light, which extend their shelf life and usability in various industries.
Multi-Layered Polypropylene Bags
One of the most notable advancements is the introduction of multi-layered PP woven bags, often laminated with polyethylene or kraft paper. This added layer of protection enhances the bags’ ability to hold heavier goods and protects against external environmental conditions like moisture and dust. Additionally, these multi-layered bags offer better print quality and branding opportunities, making them an attractive option for businesses looking to enhance their product packaging.
2. Advanced Manufacturing Techniques: Automation and Precision Engineering
Manufacturing PP woven bags has become more efficient and precise thanks to the implementation of advanced machinery and automation. Key processes such as weaving, extrusion, and lamination have all seen significant improvements in speed and consistency.
- Circular Loom Technology: The introduction of circular looms has allowed manufacturers to produce woven bags at a higher rate and with better consistency. This technology ensures that the bags are uniform in shape, which is important for both load-bearing capacity and aesthetics.
- Extrusion and Lamination: The extrusion process, used to create the base fabric for the bags, has become faster and more energy-efficient. Additionally, laminated woven bags, where the fabric is coated with a protective layer of material, offer enhanced strength and water resistance.
3. Sustainability and Recycling
With the increasing emphasis on sustainability, manufacturers have focused on improving the recyclability of PP bags. Modern woven polypropylene bags are often made from recycled PP pellets, reducing the environmental impact of their production. Furthermore, the bags themselves can be recycled at the end of their life cycle, offering a closed-loop solution that aligns with global environmental goals.
Cost Control and Efficiency in Manufacturing
1. Optimizing Raw Material Usage
Manufacturers of PP woven bags have become more adept at controlling costs by optimizing raw material usage. The move towards fine yarn technology has allowed manufacturers to use less material without sacrificing strength or durability, making production more efficient and cost-effective.
2. Automation in Manufacturing
Automation has played a crucial role in reducing labor costs and improving production efficiency. Through the use of automated machinery, such as robotic arms and conveyors, manufacturers can now produce PP woven bags at a faster pace with fewer defects. Automation has also improved quality control, as machines can be calibrated to ensure that each bag meets precise specifications.
3. Streamlined Production Lines
Modern production lines for PP bags have been designed to integrate multiple manufacturing steps, from weaving to printing and lamination, into a single continuous process. This not only reduces lead times but also minimizes energy consumption and waste, contributing to lower overall production costs.
Future Trends in Polypropylene Bag Manufacturing
As technology continues to advance, the future of PP woven bags looks promising. Some key trends to watch for include:
1. Increased Automation and AI Integration
The integration of artificial intelligence (AI) and machine learning into the production process is expected to further enhance automation. AI-driven systems can predict and adjust production parameters in real-time, reducing waste and ensuring that every PP woven bag is produced to the highest standards.
2. Smart Packaging and RFID Technology
The use of smart packaging embedded with RFID (Radio Frequency Identification) chips is becoming more common. This technology allows businesses to track and manage inventory with greater precision, improving logistics and reducing waste. As PP woven bags continue to evolve, incorporating smart features like RFID could become the norm.
3. Sustainability as a Driving Force
Sustainability will remain a key focus in the future of PP bags. Manufacturers are likely to continue innovating in material science to develop even more environmentally friendly packaging solutions. From biodegradable options to fully recyclable PP woven bags, the industry is moving towards solutions that minimize environmental impact.
4. Customization and Consumer Branding
Customization in terms of design, size, and branding will remain a significant factor in the packaging industry. Advances in printing technology, such as digital and flexographic printing, allow manufacturers to offer highly customized designs on PP woven bags at competitive prices, giving businesses a chance to promote their brand effectively.
Table: Key Specifications of Polypropylene Bags
Specification | Polypropylene Bags | PE Woven Bags |
---|---|---|
Material | 100% Polypropylene | Polyethylene + Woven fabric |
Strength | High tensile strength | Strong but less durable than PP |
Moisture Resistance | Moderate (improvable with lamination) | High (ideal for moisture-prone goods) |
Customization | High (multi-color printing, size options) | Moderate (basic customization options) |
Sustainability | Recyclable, can use recycled PP | Limited recyclability compared to PP |
Cost Efficiency | Cost-effective for bulk packaging | Slightly more expensive due to material |
FAQs
1. What are the key advantages of polypropylene bags?
- Polypropylene bags are durable, lightweight, cost-effective, and customizable. They are widely used in packaging various goods, from food to construction materials, offering excellent protection and reliability.
2. How sustainable are PP woven bags?
- PP woven bags are recyclable, and many manufacturers are now using recycled materials in their production. The bags themselves can be recycled, reducing their environmental impact.
3. What industries use polypropylene sacks?
- Industries such as agriculture, construction, retail, and food processing use polypropylene sacks to package a wide range of products, including grains, fertilizers, and animal feed.
4. How has automation affected PP bags manufacturing?
- Automation has significantly increased the speed and efficiency of PP bags manufacturing, reducing costs and defects while enhancing product quality.
5. What is the future of polypropylene bags?
- The future of PP woven bags lies in further automation, increased sustainability, and integration with smart technologies such as RFID for inventory management.
For more on how Polypropylene Bags are shaping the future of packaging, check out this article on innovations in PP bags and this exploration of the versatility of PP bags.