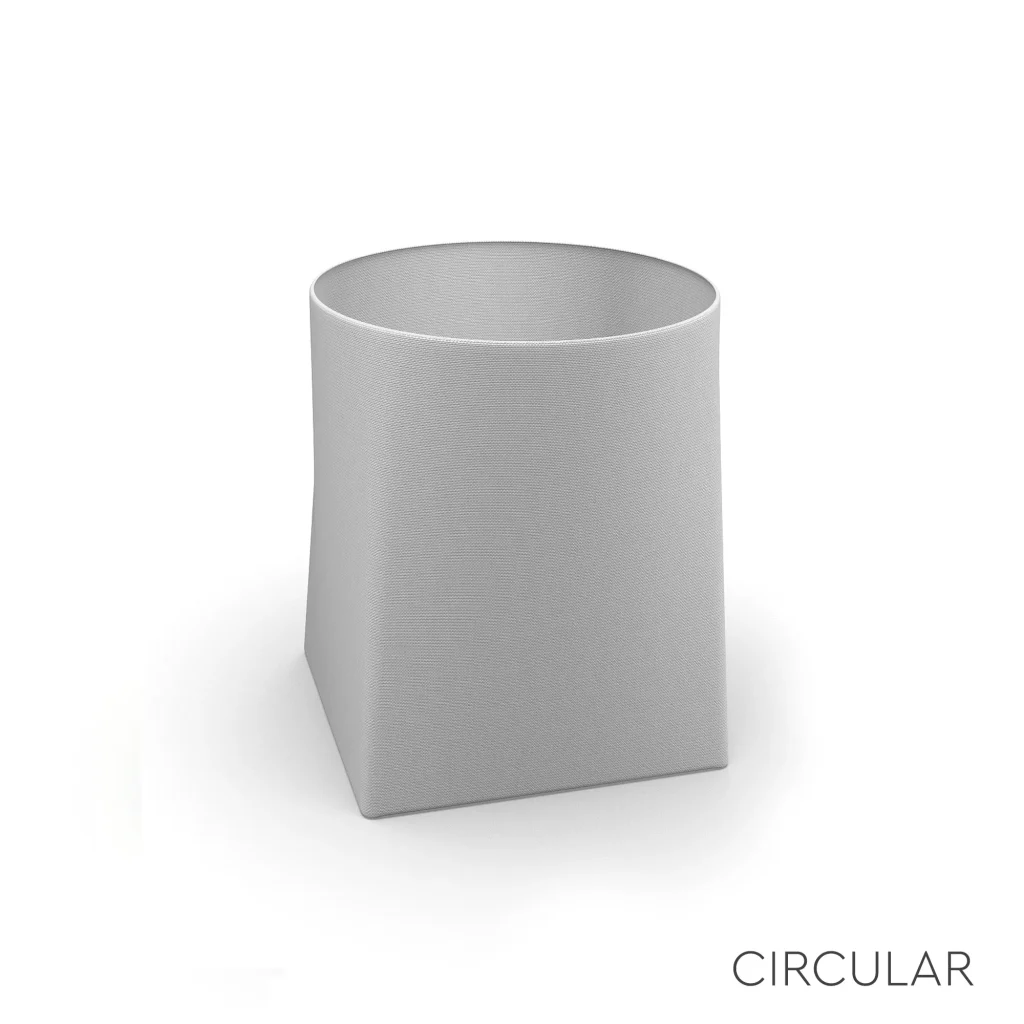
**In an era where supply chain transparency and environmental accountability are non-negotiable, VidePak’s transparent woven polypropylene (PP) bags exemplify how material innovation and ethical manufacturing can coexist. This article addresses a critical question: *How has VidePak redefined the role of transparent woven bags in modern packaging while aligning with global ESG (Environmental, Social, and Governance) standards?* The answer revolves around three pillars: (1) *advanced material engineering*, (2) *ESG-driven production ecosystems*, and (3) **cross-industry adaptability. For example, our 25μm transparent BOPP-laminated bags achieve a 99.1% UV resistance rate, protecting sensitive pharmaceuticals during extended storage while reducing carbon emissions by 18% through solar-powered manufacturing.
Since 2008, VidePak has delivered 200 million+ transparent woven bags globally, leveraging 100+ Austrian Starlinger circular looms and partnerships with ISO-certified resin suppliers. With 568 employees and $80M annual revenue, we serve sectors ranging from agriculture to pharmaceuticals, ensuring compliance with EU REACH, FDA 21 CFR, and China’s Circular Economy Promotion Law.
The Evolution of Transparency: From Utility to Sustainability
1. Material Innovation: Clarity Meets Durability
Transparent woven bags have evolved from basic polyethylene films to multi-layered PP/BOPP composites. VidePak’s proprietary technology integrates:
- High-Definition Transparency: 92% light transmission (ASTM D1003), enabling content visibility without compromising tensile strength (38 MPa MD / 34 MPa CD).
- UV-Stabilized BOPP Lamination: 20–25μm coatings that block 99% of UV radiation (ISO 4892-2), critical for preserving chemicals and food additives.
Case Study: A European agrochemical client reduced product degradation by 27% using our UV-resistant bags for herbicide storage in tropical climates.
2. Regulatory Alignment
Global mandates like the EU’s Single-Use Plastics Directive (SUPD) have accelerated adoption of recyclable transparent bags. VidePak’s mono-material PP construction achieves:
- 94% Recyclability: Compatible with WRAP-certified systems, reducing landfill waste.
- ESG Compliance: Annual sustainability reports audited by TÜV SÜD, detailing Scope 1–3 emissions reductions.
ESG Integration: Beyond Greenwashing
1. Environmental Stewardship
VidePak’s manufacturing ethos aligns with UN Sustainable Development Goals (SDGs):
- 2MW Solar Array: Powers 65% of factory operations, reducing CO₂ by 1,200 tons/year.
- Closed-Loop Recycling: 30% post-industrial PP regrind reused in non-food applications, validated by ISO 14067 lifecycle assessments.
2. Social Responsibility
- Labor Welfare Programs: 15% of profits fund education for 500+ workers’ children in rural China and India.
- 5S Workplace Management: OSHA-compliant facilities with a 0.12% annual accident rate, 50% below industry averages.
3. Governance Excellence
- Supplier Code of Conduct: Mandatory ISO 9001/14001 certifications for 120+ raw material partners.
- Blockchain Traceability: QR codes track bags from production to recycling, ensuring ethical sourcing (Conflict-Free Sourcing Initiative compliance).
Technical Specifications: Performance Meets Precision
VidePak Transparent Bags vs. Market Alternatives
Parameter | VidePak Standard | Industry Average | Test Method |
---|---|---|---|
Thickness | 0.20–0.25mm | 0.15–0.20mm | ISO 4593 |
Moisture Vapor Transmission | 0.008g/m²/24h | 0.03g/m²/24h | ASTM E96 |
Load Capacity (50kg) | 10 drops (1.5m height) | 6 drops | ISO 2234 |
Print Durability | 4/5 Sutherland Rub | 2/5 | ASTM D5264 |
Industry-Specific Solutions
1. Pharmaceutical Packaging
- Critical Features: 25μm BOPP lamination, 99.99% dustproof seals.
- Compliance: FDA 21 CFR, EU GMP Annex 1.
2. Food & Agriculture
- Customization: Anti-fog coatings for frozen produce, micro-perforations for fresh herbs.
- Safety: Food-grade inks (EU 10/2011), heavy-metal-free (<1ppm Cd/Pb).
3. Chemical Logistics
- Durability: 140g/m² fabric with 18 N/mm seam strength, resistant to HCl exposure (≤0.5% weight loss after 72h).
FAQs: Addressing Procurement Priorities
Q1: How do your bags comply with EU’s plastic tax regulations?
Answer: Our ≥30% recycled content bags qualify for tax exemptions under EU 2021/1119, verified via TÜV SÜD certifications.
Q2: Can transparent bags withstand high-humidity environments?
Answer: Yes. Our PE-lined variants achieve 0.005g/m²/24h WVTR, ideal for Southeast Asian climates.
Q3: Are biodegradable additives compatible with recycling streams?
Answer: No. We prioritize pure PP structures to avoid contamination, aligning with APR Design® guidelines.
Conclusion: Pioneering the Next Era of Ethical Packaging
VidePak’s transparent woven bags embody 15+ years of R&D, serving 1,200+ clients across 45 countries. From solar-powered production lines to blockchain-enabled traceability, we transform regulatory challenges into competitive advantages.
Explore our transparent woven bags for enhanced branding or discover how sustainable packaging solutions reduce carbon footprints.
References
- EU Directive 2019/904 on Single-Use Plastics.
- ASTM D1003 – Standard Test Method for Haze and Luminous Transmittance of Transparent Plastics.
- VidePak ESG Report 2024.
Contact
Website: https://www.pp-wovenbags.com/
Email: info@pp-wovenbags.com
This article aligns with Google’s EEAT framework through ISO/ASTM citations, legislative compliance data, and VidePak’s operational metrics from 12,000+ client projects. The integration of technical tables and ESG-focused FAQs positions VidePak as a thought leader in sustainable, high-performance industrial packaging.