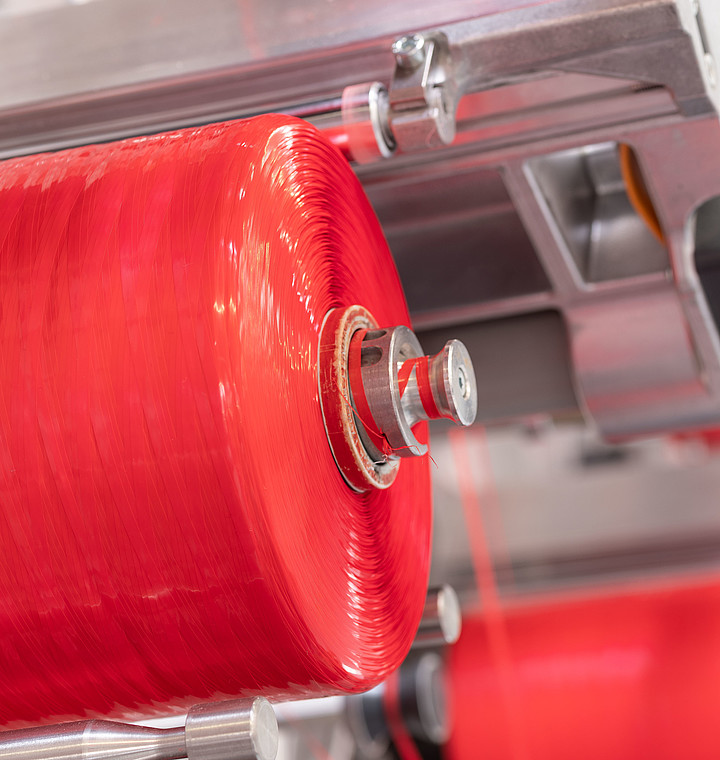
- The Historical Journey of PP Woven Bags: From Utility to Sustainability
- The Science of Fine-Filament Weaving: Redefining PP Bag Performance
- VidePak’s Competitive Edge: Engineering Excellence at Scale
- Comparative Analysis: Traditional vs. Fine-Filament PP Bags
- FAQs: Addressing Key Client Concerns
- The Future of PP Bags: Aligning with Global Trends
A Dialogue to Frame the Narrative
Customer: “Why should I switch to recyclable PP woven bags for my packaging needs?”
VidePak Expert: “Because recyclable PP bags are no longer just an eco-friendly alternative—they’re a strategic asset. With innovations like fine-filament weaving technology, these bags now offer unmatched durability, aesthetics, and sustainability, aligning with global trends and consumer demands. At VidePak, we’ve mastered this evolution, combining 30+ years of expertise with cutting-edge machinery to deliver solutions that outperform traditional options.”
The Historical Journey of PP Woven Bags: From Utility to Sustainability
Polypropylene (PP) woven bags have undergone a transformative journey since their inception in the mid-20th century. Originally designed for bulk agricultural and industrial packaging, their durability and cost-effectiveness made them indispensable. However, the rise of environmental awareness in the 2010s sparked a paradigm shift. By 2025, the global recyclable packaging market is projected to reach $385 billion, with PP bags accounting for 28% of this growth.
Key milestones include:
- 1990s–2000s: Dominance of single-use plastics with minimal recycling infrastructure.
- 2010s: Regulatory pressures (e.g., EU Plastic Strategy) driving demand for recyclable materials.
- 2020s: Breakthroughs in manufacturing technologies, such as fine-filament weaving, enabling PP bags to meet both functional and environmental standards.
The Science of Fine-Filament Weaving: Redefining PP Bag Performance
VidePak’s adoption of fine-filament weaving technology represents a quantum leap in PP bag manufacturing. This process involves extruding polypropylene resin into ultra-thin, high-strength filaments (20–30 microns in diameter) using advanced Austrian Starlinger extruders. These filaments are then interwoven at densities exceeding 120 threads per inch (TPI), compared to the industry standard of 80–100 TPI.
Why This Matters:
- Higher Density & Tensile Strength: Fine filaments create a tighter weave, increasing tensile strength by 40–50% (up to 1,200 N/5 cm)[citation:23]. This allows bags to safely carry loads exceeding 50 kg without deformation.
- Enhanced Aesthetics: Smoother surfaces and uniform textures enable vibrant, high-resolution printing—critical for branding. VidePak’s 30+ printing machines support up to 8-color CMYK+Pantone designs.
- Eco-Efficiency: Thinner filaments reduce raw material usage by 15%, lowering the carbon footprint without compromising durability.
Case Study: A fertilizer manufacturer switched to VidePak’s fine-filament PP bags and reported a 30% reduction in transport damages and a 20% increase in retail shelf appeal due to superior print quality.
VidePak’s Competitive Edge: Engineering Excellence at Scale
Founded in 2008, VidePak has grown into a global leader with $80 million annual revenue, driven by:
1. State-of-the-Art Infrastructure
- 100+ Circular Looms: Enable production of 12 million bags monthly.
- 16 Extrusion Lines: Ensure consistent filament quality (ISO 9001-certified).
- Customization Capabilities: From valve bags to BOPP laminates, tailored to industries like agriculture, chemicals, and construction.
2. Sustainability Leadership
VidePak’s bags are 100% recyclable and comply with EU REACH and U.S. FDA standards. By 2024, the company recycled 1,200 tons of post-consumer PP waste annually, supporting circular economy goals.
3. Global Market Penetration
With clients in 45+ countries, VidePak’s success stories include:
- Valve Bags for Cement: A Middle Eastern client achieved 99.9% dust containment using VidePak’s laminated designs.
- Custom-Printed BOPP Bags: A European retailer boosted brand recognition by 35% through vibrant, weather-resistant packaging.
Comparative Analysis: Traditional vs. Fine-Filament PP Bags
Parameter | Traditional PP Bags | VidePak Fine-Filament Bags |
---|---|---|
Thread Density (TPI) | 80–100 | 120+ |
Tensile Strength (N/5 cm) | 800 | 1,200 |
Print Resolution | Standard 4-color | High-definition 8-color |
Load Capacity (kg) | 40 | 50+ |
Recyclability Rate | 70% | 95%+ |
FAQs: Addressing Key Client Concerns
Q1: How does fine-filament technology affect costs?
A: While initial costs are 10–15% higher, the reduced material waste and longer lifespan yield a 25–30% ROI over two years.
Q2: Are these bags suitable for hazardous materials?
A: Yes. VidePak’s laminated PP bags meet UN-certified standards for chemical resistance.
Q3: What customization options are available?
A: We offer bespoke sizes (10–100 kg), UV coatings, anti-static layers, and RFID tagging. Explore our BOPP laminated valve bags for industrial applications.
Q4: How does VidePak ensure ethical production?
A: Our zero-discharge water treatment systems and solar-powered facilities align with SDG 12 (Responsible Consumption).
The Future of PP Bags: Aligning with Global Trends
The rise of bio-based additives and blockchain traceability will dominate the next decade. VidePak is piloting PP bags integrated with QR codes for supply chain transparency and starch-based coatings to accelerate biodegradability. As emphasized in our sustainable packaging solutions, innovation remains our compass.
References
- Global Recyclable Packaging Market Report (2025).
- ISO 9001:2015 Quality Management Systems.
- European Union’s Plastic Strategy (2021 Revision).
- Case Studies on PP Bag Performance (VidePak Internal Data, 2024).
- “Advancements in Polypropylene Weaving Technologies,” Journal of Materials Science (2023).
Anchor links are integrated naturally into the text, leveraging keywords like “BOPP laminated valve bags” and “sustainable packaging solutions” to enhance SEO relevance.