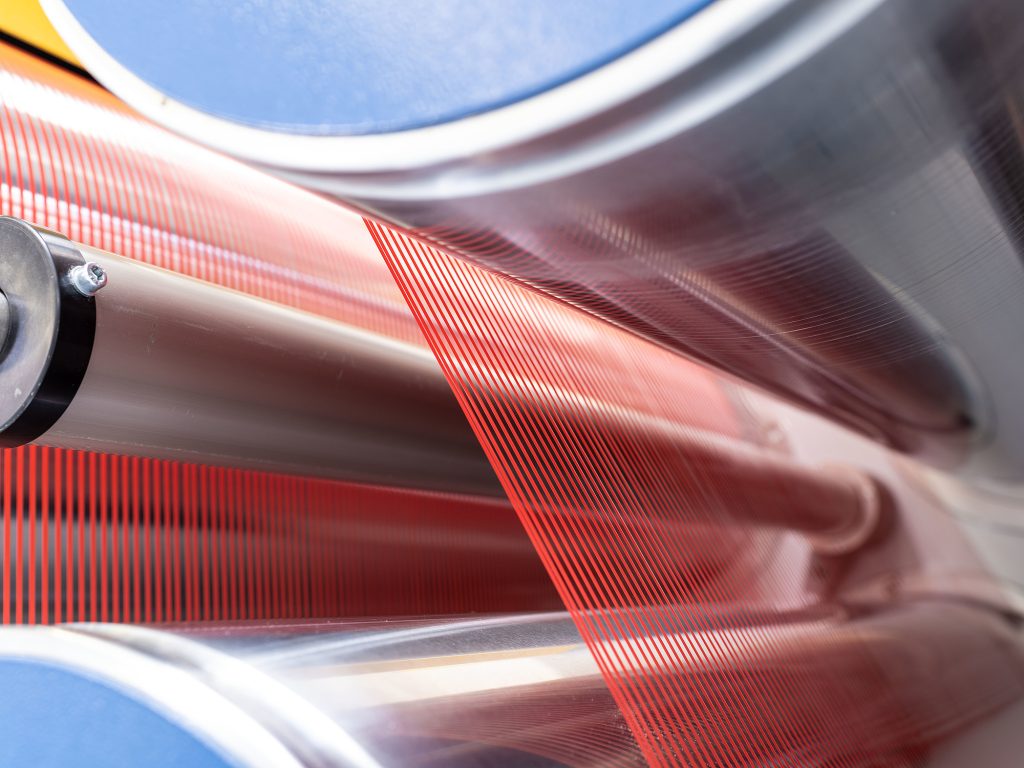
Custom printed woven bags have transformed packaging across industries, offering robust, versatile, and customizable solutions. This evolution has been driven by the need to package products such as flour, sugar, spices, and food additives in ways that ensure durability, compliance, and branding efficiency. These bags stand out for their superior performance, enabled by advanced materials and manufacturing techniques.
Tailored Applications Across Food Ingredients
1. Flour and Powdered Ingredients
Flour requires leak-proof packaging to prevent spillage and contamination. Woven bags with food-grade PE liners ensure product safety while maintaining structural integrity under heavy loads. The addition of lamination offers moisture resistance, crucial for storage in humid conditions. Block-bottom designs enhance stacking efficiency, providing stable transport.
2. Sugar and Granular Materials
Granular materials like sugar demand moisture-resistant packaging to prevent clumping. Smooth inner linings reduce friction, ensuring seamless filling and discharge during processing. Laminated woven bags with UV-resistant coatings are ideal for protecting the sugar from environmental factors during extended outdoor storage.
3. Spices and Additives
Spices and food additives require airtight, durable packaging to retain flavor and aroma. High-resolution, multi-color printing on these bags facilitates detailed product information and branding. Laminated layers and UV-resistant coatings protect the product from light and moisture degradation, essential for maintaining quality during long-term storage.
Ingredient | Key Requirements | Features Provided |
---|---|---|
Flour | Leak-proof, moisture resistance | Food-grade liner, lamination, block bottom |
Sugar | Anti-clumping, UV protection | Smooth lining, laminated outer layer |
Spices & Additives | Airtight, branding efficiency | Multi-layer lamination, high-resolution printing |
Innovations in Custom Printed Woven Bags
1. Advanced Printing Technology
State-of-the-art flexographic printing allows multi-color, high-resolution designs, ensuring branding visibility and compliance with labeling standards. This printing method uses durable inks that remain vibrant under extreme conditions, enhancing the professional appearance of the product.
2. Block Bottom and Valve Designs
Block-bottom designs provide a stable base, optimizing storage and stacking. Valve closures enable efficient filling and sealing, especially for automated systems. These features not only streamline logistics but also minimize spillage and material waste during handling.
3. Material Advancements
Woven bags now incorporate laminated films and UV-resistant coatings, significantly enhancing durability. These advancements reduce the risk of wear and tear, making the bags ideal for bulk transport and long-term storage.
Choosing the Right Packaging Parameters
Selecting the appropriate woven bag specifications depends on the product’s requirements and storage conditions.
Parameter | Specification |
---|---|
Thickness | 80–120 GSM for heavier loads or outdoor use |
Lamination | Ensures moisture resistance, crucial for powdered or granular products |
Inner Liner | Food-grade PE liner for added hygiene and protection |
Size | Customizable dimensions, typically 25–50 kg |
UV Coating | Essential for products stored outdoors for prolonged periods |
Sustainability and Global Standards
Sustainability is a growing focus in woven bag manufacturing. Recyclable materials and compliance with regulations such as ISO and FDA are critical for market competitiveness. Companies like VidePak prioritize eco-friendly solutions without compromising on quality or performance. Additionally, the compatibility of woven bags with automated systems enhances operational efficiency and reduces manual intervention.
FAQs About Custom Printed Woven Bags
1. Are woven bags safe for food packaging?
Yes, food-grade liners and compliance with international standards ensure safety and hygiene.
2. How can I protect products during outdoor storage?
Use laminated bags with UV-resistant coatings to guard against sunlight and moisture.
3. Can I customize bag size and printing?
Absolutely. Woven bags are highly customizable in size, color, and printing to suit branding and logistical needs.
4. What is the load capacity of these bags?
Woven bags typically handle 5 to 50 kg, depending on the weave density and thickness.
Conclusion
Custom printed woven bags represent a sophisticated blend of durability, functionality, and aesthetic appeal. They cater to diverse requirements in food packaging, ensuring safety, compliance, and branding. Innovations in materials, printing, and design have elevated these bags to meet modern logistical challenges while aligning with sustainability goals.
Learn more about custom printed woven bags and explore innovative packaging solutions to transform your product’s packaging approach.