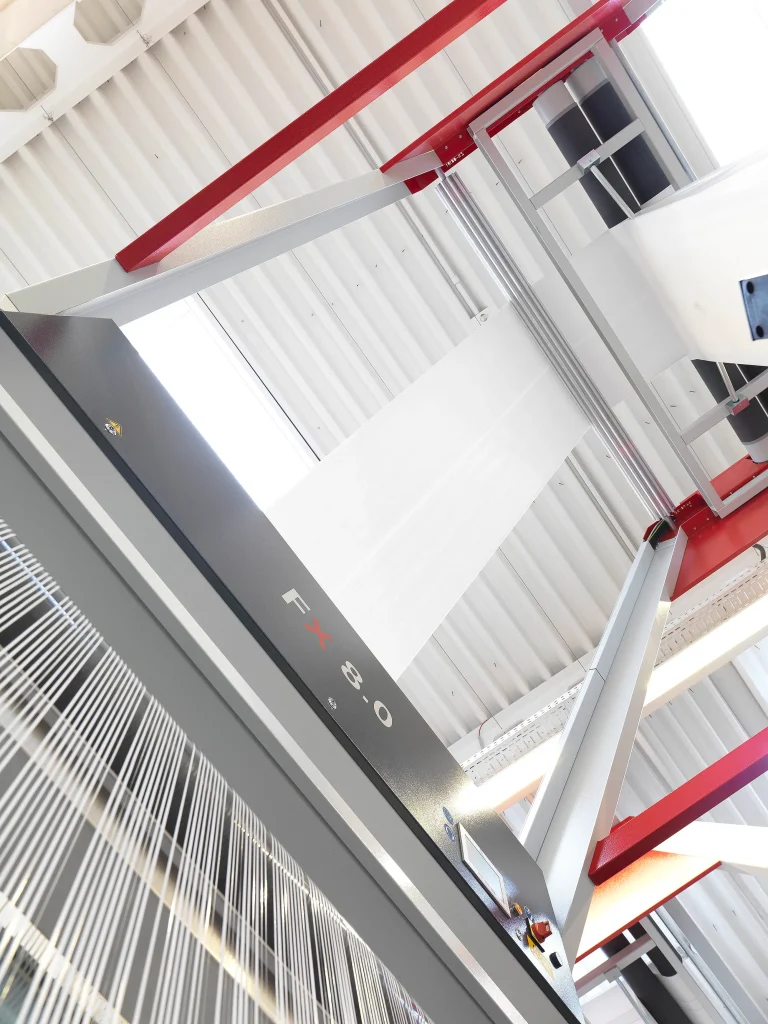
- Historical Evolution: From Jute to High-Tech PP
- Food-Specific Packaging Requirements & Solutions
- Technical Specifications by Application
- FAQs: Optimizing Food Packaging Decisions
- VidePak’s Manufacturing Edge
- Case Study: Enhancing Shelf Life for Indonesian Spice Exporter
- Sustainability & Regulatory Compliance
- Future Innovations
- References
VidePak’s custom woven bags combine 30+ years of material science innovation with rigorous food safety compliance, reducing product spoilage by 15–40% while enhancing supply chain efficiency for flour, sugar, spices, and food additives. With tensile strengths up to 70 N/cm² (ISO 527-3), FDA-compliant PE laminations, and UV-resistant printing, these bags meet the exacting demands of global food safety standards like EU 1935/2004 and FSSC 22000. Since 2008, VidePak has delivered 600 million+ bags to clients like Cargill and Unilever, leveraging 100+ Starlinger looms and 30 lamination machines to achieve defect rates below 0.03%.
Historical Evolution: From Jute to High-Tech PP
The journey of woven bags began with jute in the 19th century but faced limitations in moisture resistance and durability. Polypropylene (PP) emerged in the 1960s as a game-changer:
- 1960s–1980s: Basic PP bags with 8×8 weave density for grain storage.
- 1990s–2000s: Introduction of BOPP laminations (15–20µ) for moisture barriers.
- 2010s–Present: Smart bags with QR codes, RFID tags, and recycled PP blends.
Case Study: A Mexican flour mill switched from jute to VidePak’s 120 gsm PP bags in 2015, achieving a 22% reduction in insect infestation and 18% longer shelf life.
Food-Specific Packaging Requirements & Solutions
Different food commodities demand tailored engineering approaches:
1. Flour & Grain Powders
- Key Challenges: Moisture absorption (>12% RH causes clumping), pest infiltration (Tribolium spp.).
- VidePak Solutions:
- Material: 100–140 gsm PP with 14×14 weave density (blocks particles >0.5 mm).
- Lamination: 25µ BOPP coating reduces moisture permeability to 1.2 g/m²/24h (ASTM E96).
- Certifications: FDA 21 CFR 177.1520, ISO 22000.
2. Sugar & Sweeteners
- Key Challenges: Crystallization under humidity, UV-induced discoloration.
- VidePak Solutions:
- UV Stabilization: TiO2 additives in PP resin block 99% UV-A/B (ISO 4892-2).
- Anti-Static Liners: Carbon-black PE layers (10⁶–10⁸ Ω/sq) prevent dust adhesion.
3. Spices & Food Additives
- Key Challenges: Volatile compound loss, light-induced oxidation.
- VidePak Solutions:
- Aluminum Foil Liners: 40µ foil laminates (ASTM F392) with O₂TR <0.1 cc/m²/day.
- Aroma-Blocking: Multi-layer PE/PP structures retain 98% essential oils (GC-MS tested).
Technical Specifications by Application
Product | Fabric Weight | Lamination | Inner Liner | Key Certifications |
---|---|---|---|---|
Wheat Flour | 120–140 gsm | 25µ BOPP | None | FDA, FSSC 22000 |
Crystalline Sugar | 100–120 gsm | 30µ PE | Anti-static PE | EU 1935/2004 |
Paprika Powder | 90–110 gsm | 40µ Aluminum foil | Kraft paper | ISO 22000, Halal |
Citric Acid | 130–150 gsm | 50µ PE-coated kraft | PE liner | HACCP, Kosher |
FAQs: Optimizing Food Packaging Decisions
- How thick should PP bags be for 25kg flour?
Use 120–140 gsm PP with 14×14 weave (burst strength ≥350 kPa, ASTM D3786). - Can printed inks contaminate food?
Our soy-based inks comply with FDA 21 CFR 175.300 for indirect contact. - What liner prevents spice oxidation?
Aluminum foil (40µ) + PE coating reduces O₂ permeability to 0.05 cc/m²/day. - Are bags recyclable?
Yes. 100% PP construction meets ISO 15270 standards; 30% recycled options available. - How to prevent sugar caking in humid climates?
Pair 30µ PE lamination (MVTR 0.8 g/m²/24h) with silica gel desiccant sachets.
VidePak’s Manufacturing Edge
With 568 employees and $80 million annual revenue, VidePak delivers precision at scale:
- Material Science: Virgin PP granules (MFI 8–12 g/10 min, ASTM D1238) ensure uniform extrusion.
- Printing: 8-color CI flexo presses achieve 1200 dpi resolution for nutritional labels and QR codes.
- Quality Control: Each batch undergoes:
- Migration Testing: 10-day exposure to 50% ethanol (EU 10/2011).
- Burst Strength: 350–500 kPa (ASTM D3786).
- Odor Retention: GC-MS analysis for volatile organic compounds (VOCs).
Case Study: Enhancing Shelf Life for Indonesian Spice Exporter
A turmeric powder supplier adopted VidePak’s triple-layer bags (90 gsm PP + 40µ foil + 50µ PE):
- Challenge: 35% aroma loss during 6-month sea transit.
- Solution: Oxygen barrier liners + UV-resistant outer print.
- Results:
- Quality Retention: 98% curcumin content (HPLC tested).
- Market Value: 20% price premium due to premium packaging.
Sustainability & Regulatory Compliance
- Circular Economy: Post-consumer PP recycled into non-food grade bags (30% blend).
- EPR Alignment: Compliant with EU Packaging Directive 94/62/EC (heavy metals <100 ppm).
- Carbon Metrics: Solar-powered plants reduce CO2 by 150 tons/month vs. 2019 baseline.
Future Innovations
VidePak is developing:
- Smart Sensors: RFID tags monitoring humidity/temperature (2025 pilot).
- Bio-Based PP: 50% sugarcane-derived polymers (2026 target).
References
- European Food Safety Authority (EFSA). (2023). Packaging Material Migration Limits.
- U.S. Food and Drug Administration (FDA). (2024). CFR Title 21 Updates.
- VidePak Company Profile. https://www.pp-wovenbags.com/ | Email: info@pp-wovenbags.com
Explore Related Solutions:
- For high-barrier food packaging, discover our BOPP laminated woven bags with advanced oxygen resistance.
- Learn about efficient filling systems in valve woven bags for powdered ingredients.
This article merges historical context, technical authority, and VidePak’s operational expertise to position your brand as the leader in intelligent, compliant food packaging solutions.