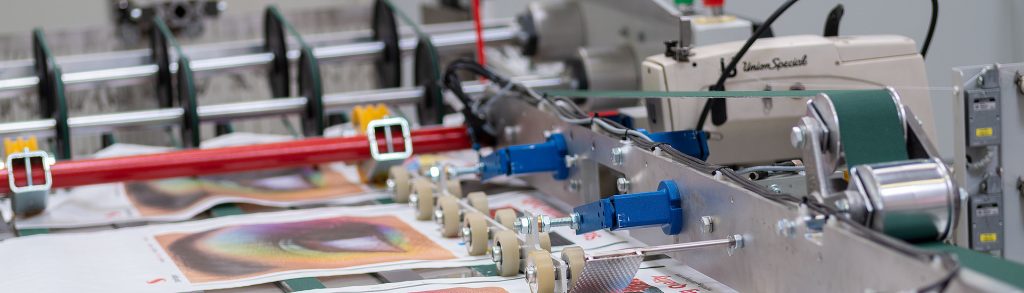
FIBC (Flexible Intermediate Bulk Container) bags, commonly known as bulk bags, have significantly evolved over the past few decades. Originally, these bags were handwoven and labor-intensive, but today, automation and mechanization have completely transformed their production. With advancements in technology, FIBC bags are now stronger, more customizable, and more cost-efficient. This article will explore the role of mechanization and automation in FIBC bag production, as well as the importance of material selection, additives, and customization.
The Shift from Manual to Automated Production
In the early days, FIBC bags were manually woven, a process that was time-consuming and limited in terms of design flexibility and strength. However, with the rise of automation, the entire production process has become faster, more reliable, and cost-effective. Automated machines have greatly increased the efficiency of manufacturing these bags, which means companies can produce large quantities while maintaining consistent quality.
Automation and Mechanization in Modern FIBC Bag Production
Today, FIBC bags are created using automated machinery that speeds up production and improves bag quality. Companies like VidePak have embraced automation with state-of-the-art equipment, such as circular looms, extrusion lines, and lamination machines. These innovations ensure that each bag meets high standards of strength, durability, and functionality.
- Circular Looms: These automated looms can produce large quantities of woven fabric with uniform quality, significantly reducing human error and production time.
- Extrusion Lines: Automated extrusion machines efficiently produce polyethylene (PE) and polypropylene (PP) films, ensuring that the right material is selected for each application.
- Lamination Machines: Lamination adds an extra layer of protection to the bags, whether it’s for UV resistance, moisture protection, or food-grade safety.
Example: Imagine a construction company needing FIBC bags to transport cement. By using circular looms, the manufacturer ensures that the bags are uniform in strength, making them less likely to tear under heavy loads. The automation of these processes ensures the company gets high-quality bags at a fast rate and at a reduced cost.
Material Choices: Polypropylene vs. Polyethylene
When it comes to selecting materials for FIBC bags, two polymers dominate the market: polypropylene (PP) and polyethylene (PE). Each material has unique properties that make it suited to different applications.
- Polypropylene (PP): PP is a strong, durable material with excellent tensile strength. It is highly resistant to wear and tear, making it ideal for heavy-duty applications. PP is also recyclable, which makes it an environmentally friendly option. Example: A chemical manufacturer needs to package fertilizers. PP bags are chosen because of their strength, which ensures that the bags can handle the weight of the product without breaking. PP’s recyclability also ensures the bags are environmentally responsible.
- Polyethylene (PE): PE bags are generally more flexible and have better moisture resistance than PP. They are well-suited for lighter loads and applications where moisture protection is crucial. Example: A food producer might use PE FIBC bags to package grains. The moisture resistance of PE ensures that the contents remain safe and dry, while the bags are light enough for easy handling.
The Role of Additives in FIBC Bags
To enhance the performance of FIBC bags, manufacturers often add various additives during the production process. These additives can improve properties like UV resistance, antioxidant protection, and static control, ensuring that the bags are suited to a wider range of conditions.
- UV Stabilizers: FIBC bags are often used outdoors, and prolonged exposure to sunlight can degrade the material. UV stabilizers protect the bags from sun damage, extending their lifespan. This is particularly important in industries like construction or agriculture where bags are exposed to the elements. Example: A company packaging sand for construction use would add UV stabilizers to their FIBC bags. This ensures that the bags won’t degrade from exposure to sunlight, preventing accidents or leaks.
- Antioxidants: Antioxidants prevent the bags from becoming brittle over time due to oxidation, especially when exposed to heat or chemicals. This helps maintain the strength and flexibility of the bags. Example: FIBC bags used in the agricultural sector for storing fertilizers may be treated with antioxidants. This ensures that the bags stay strong and flexible even in high-temperature environments.
- Anti-Static Additives: These additives are critical for industries that handle flammable materials. Anti-static additives prevent the buildup of static electricity, reducing the risk of sparks that could ignite combustible materials. Example: In the chemical industry, FIBC bags are treated with anti-static additives to safely transport powdered chemicals. This prevents any dangerous sparks during loading and unloading.
Customization and Product Performance
The ability to customize FIBC bags has revolutionized the packaging industry. With automation, manufacturers can now easily produce bags in various sizes, shapes, and specifications. Customization is not just about size; it also involves the choice of materials, design, and added features such as UV protection or lamination. This flexibility allows FIBC bags to meet the needs of specific industries, whether it’s for transporting food, chemicals, or construction materials.
Example: A company specializing in food packaging may require FIBC bags with extra layers for food safety and moisture resistance. Automated machines allow manufacturers to customize the bag’s construction to meet these specific needs, ensuring the product stays fresh and safe during transport.
Key Product Parameters
Here’s a breakdown of key features and performance factors for FIBC bags made from PP and PE:
Parameter | Polypropylene (PP) | Polyethylene (PE) |
---|---|---|
Tensile Strength | High | Moderate |
Durability | Excellent | Moderate |
Moisture Protection | Low | High |
UV Resistance | High (with additives) | Moderate (with additives) |
Cost | Moderate to High | Low |
Recyclability | High | Moderate |
Frequently Asked Questions (FAQs)
1. What’s the difference between PP and PE FIBC bags?
PP bags are stronger and better suited for heavy-duty applications, while PE bags offer better moisture resistance and flexibility, making them ideal for lighter loads or food packaging.
2. Can FIBC bags be customized for different industries?
Yes, FIBC bags can be customized in terms of size, material, and added features like UV protection, lamination, and static control, depending on the specific requirements of the industry.
3. Are FIBC bags eco-friendly?
FIBC bags made from PP are recyclable and can be reused multiple times, making them an eco-friendly choice. Additionally, some manufacturers use biodegradable additives to enhance sustainability.
4. How do UV stabilizers affect FIBC bags?
UV stabilizers prevent degradation caused by sunlight exposure, extending the life of the bags and maintaining their integrity, which is important for outdoor applications.
5. What industries use FIBC bags?
FIBC bags are widely used in industries such as agriculture, chemicals, food packaging, construction, and pharmaceuticals due to their strength, versatility, and cost-effectiveness.
Conclusion
FIBC bags have come a long way from their manual origins, thanks to automation and mechanization. These technological advancements have allowed for stronger, more durable, and customizable bags that meet the needs of a variety of industries. By carefully selecting materials like PP or PE, adding the right additives, and embracing customization options, businesses can ensure they are using the most effective packaging solution for their needs.
For more insights into FIBC bags, check out our article on Industrial Woven Packaging Bags Aligning with Policies and ESG Standards and explore the advancements in BOPP Laminated Woven Bags.