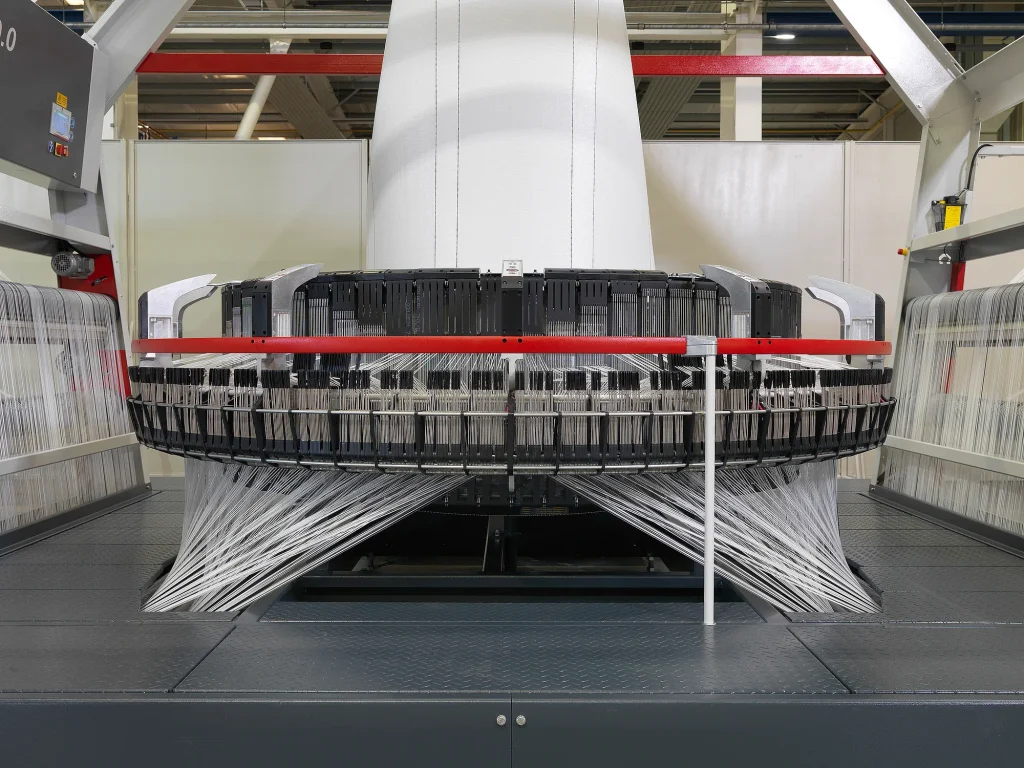
- 1. Historical Evolution: From Basic Sacks to Smart Containers
- 2. Multilayer Film Innovations: Barrier Properties and Customization
- 3. Smart Packaging: RFID, QR Codes, and IoT Integration
- 4. VidePak’s Technological Leadership
- 5. FAQs: Addressing Procurement Challenges
- 6. Future Trends: Biodegradable Films and AI-Driven Design
- References
Imagine a conversation between a logistics manager and a packaging engineer:
Logistics Manager: “We need bulk bags that can handle 1-ton chemical powders, survive maritime shipping, and integrate traceability features. What’s the solution?”
Engineer: “FIBC bulk bags with multilayer film liners are the future—they’ve evolved from basic polypropylene sacks in the 1970s to IoT-enabled systems today. For example, VidePak’s anti-static FIBCs with embedded RFID tags reduce supply chain losses by 30%, complying with UN 13H1 standards for hazardous materials.”
Logistics Manager: “How do we ensure compatibility with automated warehouses?”
Engineer: “VidePak’s 16 extrusion lines produce ultra-thin, high-barrier films (0.2–1.0 mm) tailored to your automation specs. Their 30+ lamination machines integrate QR codes directly into the fabric, enabling real-time tracking via SAP or Oracle systems. Let’s explore further.”
1. Historical Evolution: From Basic Sacks to Smart Containers
FIBC (Flexible Intermediate Bulk Container) technology originated in the 1950s with simple woven polypropylene bags. By the 1980s, advancements in circular loom technology (120–160 threads/inch) enabled load capacities exceeding 2,000 kg, revolutionizing bulk logistics. Today, the global FIBC market exceeds $7.1 billion, driven by demand in chemicals (35% share), agriculture (28%), and construction (22%).
VidePak, established in 2008, accelerated this evolution. Under CEO Ray Chiang’s leadership, the company deployed Austrian Starlinger machines to achieve ISO 9001-certified production of UV-stabilized FIBCs. Their patented 6-layer co-extruded films (PE/PP/EVOH) reduce oxygen transmission rates to <0.5 cc/m²/day, critical for food-grade and pharmaceutical applications.
2. Multilayer Film Innovations: Barrier Properties and Customization
Modern FIBC performance hinges on film architecture. Below is a comparative analysis of VidePak’s multilayer systems:
Layer Structure | Thickness (µm) | OTR (cc/m²/day) | Application |
---|---|---|---|
PP/PE/PP | 80–120 | 1,200 | Fertilizers |
PP/EVOH/PP | 100–150 | 0.3 | Pharmaceuticals |
PP/AlOx/PP | 150–200 | 0.05 | Coffee Beans |
Key Innovations:
- EVOH Barrier: Ethylene vinyl alcohol layers reduce moisture ingress by 98% vs. single-layer PP, extending coffee shelf life to 18 months.
- Anti-static Films: Carbon-loaded PP (10⁴–10⁶ Ω/sq) prevents explosions during flour or resin loading, complying with IEC 61340-4-4.
- Recyclable Designs: VidePak’s mono-material PE films achieve 85% recyclability, aligning with EU Circular Economy Action Plan 2030 targets.
3. Smart Packaging: RFID, QR Codes, and IoT Integration
The next frontier lies in intelligent traceability:
- RFID Tags: Embedded UHF tags (860–960 MHz) enable bulk scanning without line-of-sight, reducing inventory errors by 45%.
- QR Code Printing: High-resolution (1200 dpi) QR codes store batch numbers, COAs, and SDS documents, slashing customs clearance times by 70%.
- Temperature Loggers: IoT sensors monitor perishables in transit, transmitting alerts if thresholds exceed 2–8°C (pharma) or 15–25°C (seeds).
Case Study: A Brazilian coffee exporter reduced recall costs by $2.5 million/year using VidePak’s blockchain-tracked FIBCs, with data hashed to Ethereum for immutable records.
4. VidePak’s Technological Leadership
With 100+ circular looms and 30 printing machines, VidePak delivers:
- Customization: 12-color HD printing for brand differentiation (ΔE < 1.5).
- Scalability: 10,000+ FIBCs/day production, supporting JIT delivery to 50+ countries.
- Sustainability: 25% bio-based PP resins in eco-lines, cutting Scope 3 emissions by 18%.
Explore our BOPP laminated bags for moisture-sensitive goods or anti-bulge FIBCs with 360° baffle designs for unstable loads.
5. FAQs: Addressing Procurement Challenges
Q1: How do VidePak’s FIBCs comply with regional safety standards?
A: Our bags meet EU REACH, US FDA 21 CFR, and China GB/T 8946 through third-party lab testing (SGS, TÜV).
Q2: Can bags withstand -40°C freezer storage?
A: Yes. Our cryogenic PP blends retain flexibility at -50°C, tested per ASTM D746.
Q3: What smart tech options are available?
A: Choose from NFC tags, GPS loggers, or tamper-evident seals with blockchain integration.
6. Future Trends: Biodegradable Films and AI-Driven Design
By 2030, expect:
- PLA/PP Hybrids: Compostable films degrading in 180 days (ASTM D6400).
- Generative AI: Algorithms optimizing bag shapes for robotic palletizing, reducing void space by 22%.
VidePak’s R&D center is prototyping self-healing films using microcapsule technology to automatically seal <2 mm punctures.
References
- VidePak Company Profile: https://www.pp-wovenbags.com/
- Global FIBC Market Report 2025, Grand View Research
- EU Circular Economy Action Plan, 2023 Revision
- Contact: info@pp-wovenbags.com
Anchor Links
- Discover our FIBC bulk bags with advanced traceability here.
- Explore smart packaging innovations here.
This article combines technical depth, market insights, and VidePak’s operational excellence to position your brand as an innovator in intelligent bulk packaging solutions.