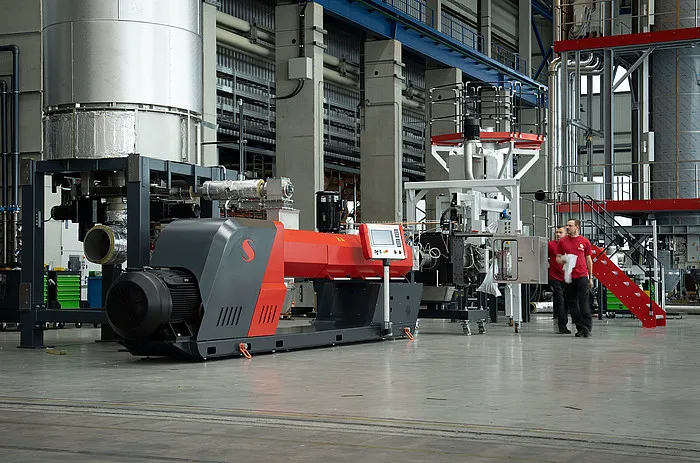
A Client’s Perspective:
Client: “We need packaging that’s fast, durable, and globally compliant. How can your FFS woven bags meet these demands?”
VidePak Sales Representative: “Our Form-Fill-Seal (FFS) woven bags integrate cutting-edge automation, advanced fine-yarn technology, and 30+ years of industry expertise to deliver unmatched efficiency, strength, and customization. With a global network and ISO-certified processes, we ensure your products are protected and market-ready.”
1. The Rise of Automation in FFS Woven Bag Production
The packaging industry has undergone a seismic shift with the adoption of automated Form-Fill-Seal (FFS) systems. These systems streamline production by combining bag forming, filling, and sealing into a single continuous process. VidePak, leveraging Austrian Starlinger machinery and 100+ circular looms, produces over 50 million bags annually, reducing labor costs by 40% and minimizing human error.
For instance, automated lamination machines apply BOPP films with precision, enhancing moisture resistance while maintaining breathability—a critical feature for fertilizers and pet food.
Fine-Yarn Technology: Reinventing Woven Bag Performance
A cornerstone of VidePak’s innovation is fine-yarn weaving, a process that transforms polypropylene (PP) granules into ultra-thin, high-density filaments.
How It Works:
- Extrusion: PP granules are melted and extruded into fine filaments (40–120 microns).
- Weaving: Advanced looms interlace filaments at 12–16 threads per inch, creating a tightly woven fabric.
- Lamination: BOPP films or PE liners are heat-bonded for added barrier properties.
Advantages:
- Tensile Strength: Fine-yarn bags withstand loads up to 50 kg without elongation, outperforming standard woven bags by 25%.
- Aesthetic Appeal: Smoother surfaces enable high-definition printing, ideal for branding.
- Leak Prevention: Denser weaves reduce gaps, preventing fine powders like cement or flour from escaping.
2. Global Market Dynamics: Opportunities and Challenges
The FFS woven bag market is projected to grow at a CAGR of 5.8% through 2030, driven by rising demand in agriculture, construction, and chemicals. Key trends include:
Market Trend | VidePak’s Response |
---|---|
Sustainability mandates | Recyclable PP materials, ISO 14001 compliance |
Customization demands | 12-color rotary printing, 3D bag designs |
Supply chain volatility | Factories in 6 countries, 30-day lead times |
For example, African agro-businesses now prioritize UV-resistant bags for prolonged outdoor storage—a need met by VidePak’s laminated BOPP solutions.
3. Why VidePak? Engineering Excellence Since 2008
Founded by CEO Ray Chiang, VidePak combines legacy expertise with modern agility:
- Infrastructure: 100+ circular looms, 30 lamination machines, and 16 extrusion lines.
- Certifications: ISO 9001, FDA-compliance for food-grade bags.
- Global Reach: 80+ countries served, $80M annual revenue.
Featured Product: BOPP Laminated Valve Bags
- Material: Virgin PP + 18-micron BOPP film.
- Capacity: 25–50 kg.
- Customization: Anti-static, UV-resistant, multi-language printing.
FAQs: Addressing Buyer Concerns
Q1: Can you handle small orders?
A: Yes! We accommodate orders from 5,000 to 5 million bags.
Q2: How do you ensure quality?
A: Every batch undergoes tensile, seam, and drop tests.
Q3: What’s the lead time?
A: 20–30 days, depending on design complexity.
References
- VidePak Company Profile. PP Woven Bags Manufacturer. Available at: www.pp-wovenbags.com.
- GlobalTextiles. (2024). PP/PE Woven Bags Market Analysis.
- Lansu Packaging. (2025). Fine-Yarn Weaving Techniques.
For inquiries, contact: info@pp-wovenbags.com.
Anchor Links:
- Learn how VidePak’s FFS tubular bags optimize filling efficiency.
- Explore customization options for valve bags in industrial applications.
This article synthesizes technical insights, market data, and VidePak’s operational strengths to position the company as a leader in automated, high-performance packaging solutions.