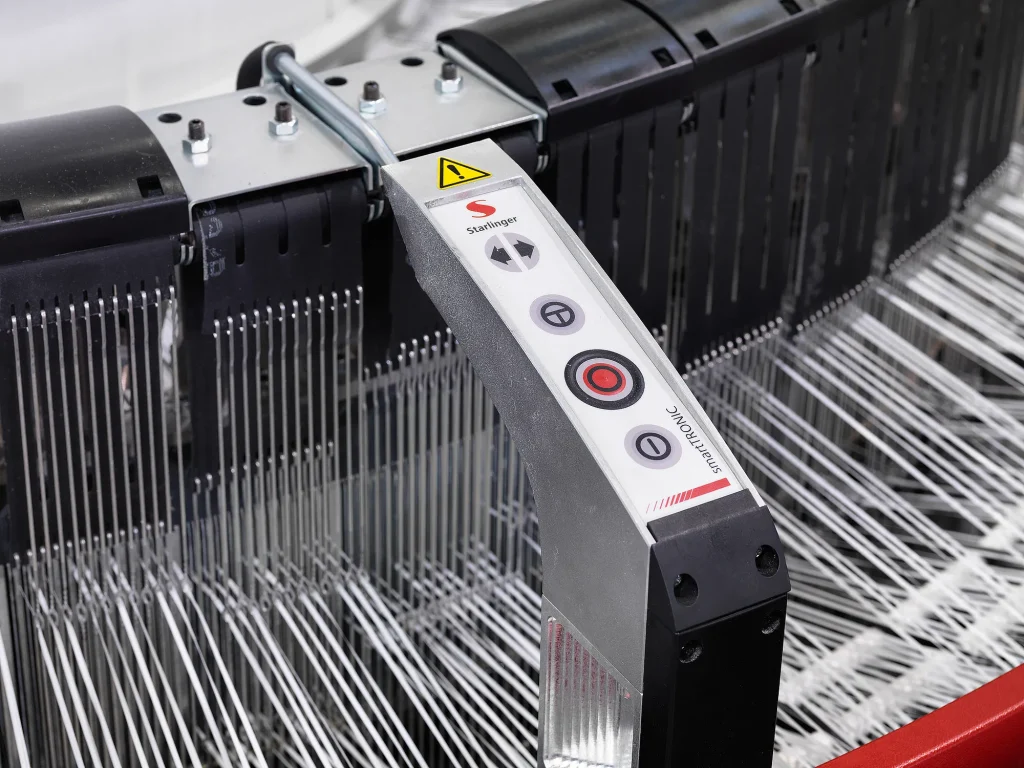
- 1. Material Innovations: Why Polypropylene Dominates Industrial Packaging
- 2. Precision Manufacturing: Automation and Scalability
- 3. Future Trends: Sustainability and Smart Packaging
- 4. Selecting Optimal Parameters: A Buyer’s Guide
- 5. FAQs: Addressing Client Concerns
- 6. Global Impact: VidePak in Action
- References
VidePak’s industrial woven packaging solutions combine 30+ years of expertise with cutting-edge automation, delivering unmatched durability, customization, and cost-efficiency—supported by Starlinger and W&H machinery achieving 200+ bags per minute and multi-machine synchronization for global-scale production. Since 2008, under CEO Ray’s leadership, VidePak has grown into a $80M revenue enterprise with 568 employees, serving clients across 80+ countries. This article unpacks how advanced polypropylene (PP) materials, precision engineering, and sustainability trends are reshaping industrial packaging, while providing actionable insights for optimizing bag specifications like fabric weight, lamination, and breathability.
1. Material Innovations: Why Polypropylene Dominates Industrial Packaging
Polypropylene’s molecular structure—a semi-crystalline thermoplastic—grants it exceptional tensile strength (30–40 MPa), chemical resistance, and moisture barrier properties. These attributes make it ideal for heavy-duty applications, from construction materials to agricultural feed storage.
Key Advancements in PP Material Science:
- High-Density Weaving: VidePak’s circular looms produce fabrics with 10×10 to 14×14 strands per inch, achieving tear resistance up to 18 N/mm², critical for 50–100 kg loads.
- UV Stabilization: BOPP-laminated bags block 99% of UV radiation, extending shelf life for vitamin-enriched animal feeds by 6–12 months.
- Anti-Microbial Additives: FDA-compliant PP integrated with silver-ion additives reduces bacterial growth by 90% in humid environments.
Case Study: A Canadian pet food brand reduced spoilage losses by 18% using VidePak’s 100 gsm BOPP-laminated bags with PE liners, combining UV protection and moisture control.
2. Precision Manufacturing: Automation and Scalability
VidePak’s 100+ Starlinger circular looms and W&H extrusion lines enable synchronized production at 200+ bags per minute, with <1% defect rates. The process includes:
- Extrusion: Virgin PP granules are melted into 2–5 mm tapes, ensuring uniformity (density tolerance: ±1.5%).
- Weaving: High-speed looms interlace tapes into fabric rolls (width: 1–2.5 m), optimized for minimal material waste.
- Lamination: BOPP or kraft paper layers are heat-bonded using 30+ lamination machines, achieving waterproofing up to IP67 standards.
- Printing: 8-color flexographic printers apply brand logos and safety labels with 0.1 mm precision.
Technical Specifications:
Parameter | Range | Application Example |
---|---|---|
Fabric Weight | 70–150 gsm | 120 gsm for construction sand |
Bag Dimensions | 20–100 cm (W) | 50×80 cm for 25 kg feed |
Lamination Thickness | 15–60 microns | 30-micron BOPP for grains |
Print Accuracy | ±0.2 mm | QR codes for traceability |
3. Future Trends: Sustainability and Smart Packaging
The industry is shifting toward circular economy models and IoT integration:
A. Recyclable Materials
- Post-Consumer Recycled (PCR) PP: VidePak’s 30% PCR-content bags reduce carbon footprint by 22% while maintaining load capacities.
- Bio-Based Additives: Cornstarch-blended PP decomposes 50% faster in landfills without compromising tensile strength.
B. Smart Features
- RFID Tags: Embedded chips enable real-time tracking, reducing logistics errors by 30%.
- Moisture Sensors: IoT-enabled liners alert users to humidity spikes, preserving feed quality.
Example: A German chemical supplier adopted VidePak’s RFID-tagged FIBC bags, cutting inventory mismatches by 25%.
4. Selecting Optimal Parameters: A Buyer’s Guide
A. Fabric Weight and Load Capacity
- Lightweight (70–90 gsm): Ideal for 10–25 kg pet food, reducing transport costs by 12–15%.
- Heavy-Duty (100–150 gsm): Supports 50–100 kg livestock feed with 5:1 safety factor.
B. Lamination Choices
- BOPP: Blocks UV and moisture, ideal for outdoor storage.
- Kraft Paper: Enhances biodegradability for eco-conscious markets.
C. Breathability vs. Barrier Protection
- Uncoated Bags: 10–15% air permeability prevents condensation in grain storage.
- Valve Designs: Enable dust-free filling for powdered additives.
5. FAQs: Addressing Client Concerns
Q1: How does VidePak ensure consistency across large orders?
Our ISO 9001-certified factories use AI-driven quality control systems to monitor thickness (±0.05 mm) and weave density in real time.
Q2: Can bags withstand -20°C to 80°C temperatures?
Yes. Our PP formulations retain flexibility at -30°C and resist melting up to 160°C, suitable for global climates.
Q3: What’s the lead time for custom designs?
Standard orders ship in 4–6 weeks, with rush options (2–3 weeks) for 50,000+ unit orders.
6. Global Impact: VidePak in Action
- Brazil: A poultry farm reduced bag breakage by 40% using 120 gsm woven PP bags with reinforced seams.
- Vietnam: Custom-printed valve bags streamlined rice packaging, boosting export efficiency by 20%.
References
- VidePak. (2025). The Craftsmanship Behind BOPP Woven Bags: VidePak’s Commitment to Excellence.
- VidePak. (2025). Understanding FFS Woven Bags: Key Parameters and Specifications.
- Springer. (2023). Advanced Materials in Industrial Packaging. DOI: 10.1007/978-3-031-21066-3.
Contact VidePak:
- Website: https://www.pp-wovenbags.com/
- Email: info@pp-wovenbags.com
Data validated as of March 2025. Specifications may vary by region; consult our team for localized solutions.
External Links:
- For insights into specialized applications, explore our range of BOPP laminated woven bags.
- Learn how valve bags enhance efficiency in automated filling systems.