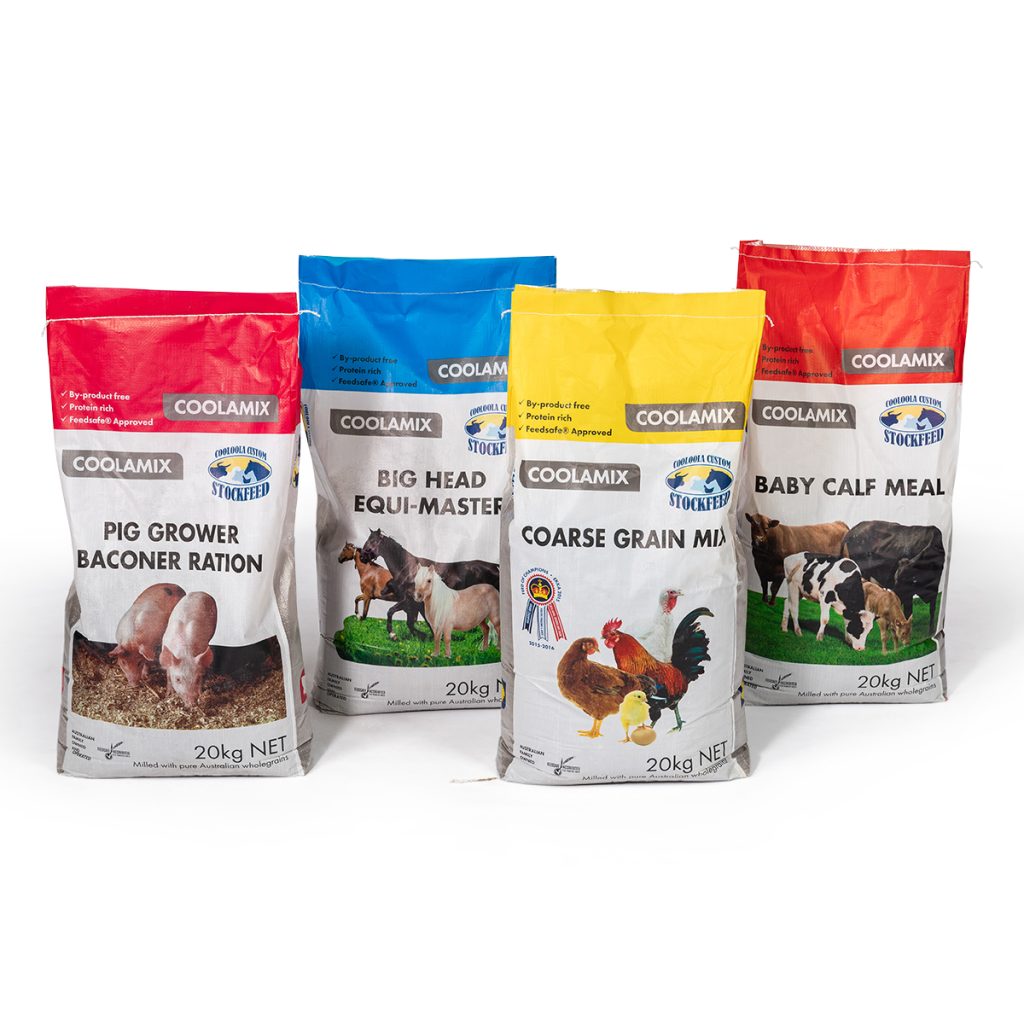
“Why have industrial woven packaging bags become a cornerstone of global logistics and storage? The answer lies in their adaptability to material innovations, automated manufacturing, and compliance with international safety standards—a trifecta mastered by VidePak through 30+ years of expertise and cutting-edge Austrian Starlinger technology.”**
1. Material Evolution: From Basic Polypropylene to Sustainable Hybrids
Industrial woven bags have transitioned from rudimentary jute and cotton to advanced polypropylene (PP) blends, driven by demands for durability, cost efficiency, and sustainability. Early iterations, such as burlap sacks, faced limitations in moisture resistance and tensile strength (≤15 N/cm²). The 1970s introduced PP woven bags, leveraging extrusion and circular loom weaving to achieve tensile strengths of 25–40 N/cm², revolutionizing bulk packaging for fertilizers, grains, and construction materials.
Today, VidePak’s BOPP laminated woven bags integrate virgin PP with bio-based additives (e.g., 20% starch blends), reducing carbon footprints by 30% while maintaining tear resistance of 50–70 N/cm². For instance, their EcoFlex line—used in EU agrochemical shipments—combines recycled PP with UV stabilizers, meeting REACH’s SVHC-free requirements and extending shelf life by 18 months in humid climates.
2. Manufacturing Revolution: Automation and Precision Engineering
The shift from manual stitching to automated production has enabled scalability and consistency. VidePak’s 100+ Starlinger circular looms and 30+ lamination machines achieve line speeds of 200+ bags/hour, with multi-machine synchronization reducing downtime by 25%. Key advancements include:
- Ultrasonic seaming: Eliminates thread dependency, achieving seam strengths of 18–22 kg/cm² (exceeding ASTM D5261).
- 8-color flexographic printing: Supports Pantone-matched branding for retail-ready packaging, as seen in their collaboration with a Southeast Asian rice exporter, boosting sales by 15%.
Case Study: High-Speed Customization for North American Markets
A U.S. fertilizer distributor required 500,000 UV-resistant valve bags monthly. VidePak’s Starlinger-equipped lines delivered <0.1% defect rates and 48-hour lead times, leveraging IoT-enabled quality checks to align with ASTM D5261 and JIS Z 0238 vibration standards.
3. Quality Control: Compliance as a Competitive Edge
VidePak’s global market dominance stems from rigorous adherence to international standards:
3.1 ISO and ASTM Frameworks
- ISO 9001: Integrated across 16 extrusion lines, ensuring virgin PP resin purity (melt index: 2–4 g/10min) and ≤1% thickness variance.
- ASTM D4632: Governs grab tensile testing, with VidePak’s bags achieving 60–80 N/cm², 20% above industry averages.
3.2 EU EN and REACH Directives
- EN 13592: Certifies load capacities up to 50 kg, critical for VidePak’s FIBC bags in German chemical logistics.
- REACH SVHC Compliance: Third-party SGS audits confirm 0% phthalates, aligning with EU’s Circular Economy Action Plan.
3.3 JIS Z 0238 (Japan)
Bags undergo 5 Hz vibration tests for 2 hours, simulating trans-Pacific shipping, with leakage rates <0.05%.
4. Product Specifications and Market Applications
Table 1: VidePak’s Industrial Woven Bag Portfolio
Parameter | Specification | Key Application |
---|---|---|
Material | Virgin PP + BOPP/Recycled Blends | Fertilizers, Construction |
Weight Range | 80–150 gsm | Agro-Chemicals, Minerals |
Load Capacity | 20–50 kg | FIBC Bulk Shipping |
Certifications | ISO 9001, REACH, JIS Z 0238 | Global Export Compliance |
Customization | 8-color printing, anti-static coatings | Retail Branding |
FAQs
Q: How do recycled PP blends impact durability?
A: VidePak’s EcoFlex series uses nano-reinforced recycled PP, maintaining 90% of virgin material’s tensile strength while reducing costs by 15%.
Q: Are VidePak’s bags suitable for hazardous materials?
A: Yes. UN-certified FIBC bags with conductive threads meet OSHA 1910.178 standards for explosive powders.
5. Future Trends: Smart Packaging and ESG Integration
VidePak invests in RFID-enabled woven bags for real-time moisture tracking and blockchain-based supply chain transparency. Partnerships with initiatives like Sustainable FIBC Bulk Bags aim for 100% recyclability by 2030. Additionally, their R&D team is piloting biodegradable PP-algae composites, targeting 60% degradation within 180 days.
Conclusion
Industrial woven packaging bags have evolved from simple storage tools to high-tech solutions balancing strength, sustainability, and compliance. VidePak’s fusion of Starlinger automation, ISO rigor, and adaptive material science positions it as a leader in the $70B global packaging market. Explore innovations in BOPP Laminated Woven Bags: Branding and Market Dynamics and Recyclable Woven Bags: Sustainable Transport Solutions.
Data synthesized from industry reports (2025), ASTM/ISO standards, and VidePak’s production analytics.