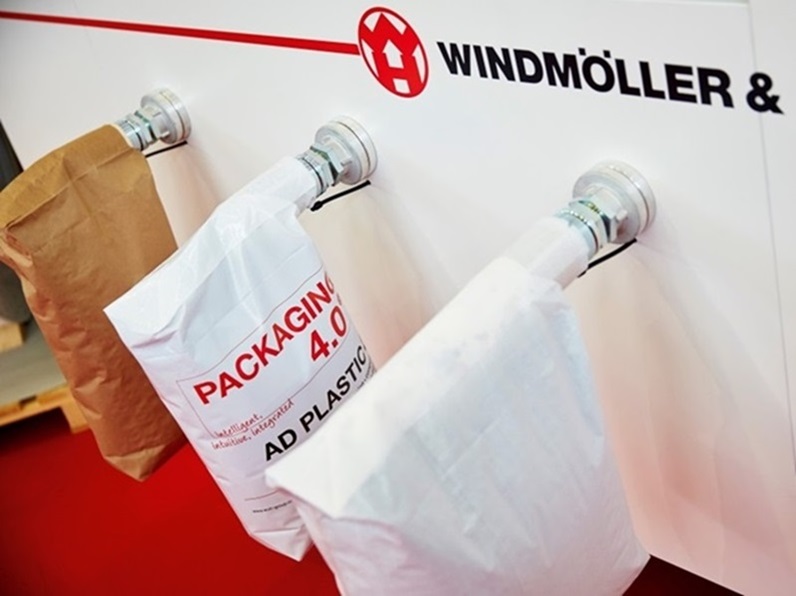
Open Mouth Polypropylene (PP) Bags have become a staple in various industries, from agriculture to construction and even food packaging. Their evolution over the years has been shaped by key advancements in technology, improvements in materials, and a strong focus on cost control. At the same time, sustainability has become a significant priority in production. In this article, we will explore how these bags have evolved, how technology and materials have improved, and how companies like VidePak have embraced sustainable practices in their manufacturing process.
Technological Advancements in Open Mouth PP Bags
The production of Open Mouth PP Bags has greatly benefited from technological improvements. These bags, which are commonly used for packaging grains, fertilizers, and pet food, have become more efficient, durable, and customizable thanks to new machinery and automated systems.
- Automation and Efficiency
Automation has played a crucial role in the evolution of PP bag production. Machines like those from Starlinger have improved the precision of the weaving process, ensuring consistent quality and strength in each bag. These machines allow for faster production, meaning manufacturers can meet growing demand more effectively.
Example: A large pet food company recently upgraded its production line with automated machines, increasing production by 40% while reducing error rates by 30%. This automation has lowered labor costs and increased consistency across products.
- Advanced Sewing Technology
The sewing process that seals the open mouth of PP bags has also evolved. Automatic sewing systems now ensure that bags are sealed uniformly, reducing production errors. These systems also allow for higher production speeds, which is essential for industries like agriculture that require large volumes of bags.
Example: A company in the construction sector introduced high-speed sewing machines that helped them meet deadlines for bulk orders, while maintaining strong bag seams even under heavy load conditions.
Material Innovations and Customization
The materials used to make Open Mouth PP Bags have also seen significant improvements. Initially, basic polypropylene was used, but today’s bags are made with more advanced materials that improve durability, flexibility, and sustainability.
- BOPP Laminates for Enhanced Durability
Biaxially Oriented Polypropylene (BOPP) film is often laminated onto PP bags, which improves their strength and resistance to moisture. This is especially useful for packaging products like pet food, where moisture resistance is crucial. BOPP films also allow for high-quality printing, making the bags more visually appealing for retail markets.
Example: A pet food manufacturer upgraded to BOPP laminated bags to better preserve the freshness of its products. The new bags not only offered better protection from moisture but also allowed for more attractive packaging, helping the brand stand out on store shelves.
- Recycled Polypropylene
With increasing environmental concerns, many manufacturers now incorporate recycled polypropylene in their production. This reduces the need for virgin materials and helps minimize the environmental impact of packaging production.
Example: VidePak, a leading manufacturer, switched to using recycled polypropylene for many of its bags, reducing its carbon footprint and making its products more sustainable without compromising quality.
- Multi-Layer Construction for Extra Protection
Many modern Open Mouth PP Bags are made with multiple layers of material, improving their overall strength, moisture resistance, and ability to handle heavy loads. This construction method makes the bags more suitable for a variety of uses, from storing construction materials to packaging food and chemicals.
Example: A fertilizer company uses multi-layer PP bags for packaging, ensuring that their products stay secure during long-distance shipping, and that the bags hold up under heavy loads without tearing.
Cost Control and Operational Efficiency
In addition to technological and material advancements, controlling costs remains a key priority for manufacturers. Several strategies have been implemented to keep production costs down while maintaining high-quality standards.
- Streamlined Production Processes
The automation of production processes has reduced labor costs significantly. By reducing the number of workers needed on the production line, manufacturers can save money and focus on improving other areas, such as material quality or customer service. - Optimized Material Usage
Advanced production systems allow for more precise material handling, ensuring that only the necessary amount of polypropylene is used for each bag. This reduces waste and helps keep costs down, while also ensuring that the bags remain strong and durable.
Example: VidePak’s use of optimized extrusion systems has reduced material waste by 15%, allowing them to produce more bags with less raw material. This reduction in waste not only lowers costs but also contributes to sustainability efforts by reducing the overall consumption of polypropylene.
- Energy Efficiency
Many manufacturers are also focusing on energy-efficient technologies to lower production costs. For example, LED lighting, energy-efficient machines, and optimized heating systems help reduce overall energy consumption during production.
Example: VidePak installed a 2MW photovoltaic solar power system on their factory roof, which powers a significant portion of their production. This investment has not only cut energy costs but also allowed the company to sell surplus power back to the national grid, generating additional revenue while contributing to cleaner energy production.
Sustainability in Open Mouth PP Bag Production
Sustainability has become a top priority for many companies in the packaging industry, including those producing Open Mouth PP Bags. Companies are adopting renewable energy sources, using recycled materials, and minimizing water and energy usage during production to reduce their environmental footprint.
- Solar Power Integration
VidePak has installed a 2MW solar power system on the roof of their manufacturing facility, which powers the production process. Any excess energy is sold to the national grid, generating revenue and contributing to the country’s renewable energy goals. This system significantly reduces the factory’s carbon footprint and reliance on non-renewable energy sources. - Recycling and Waste Reduction
Many manufacturers now use recycled polypropylene, which not only reduces the need for virgin plastic but also supports the circular economy. Additionally, by reducing material waste through precise production processes, manufacturers help mitigate the environmental impact of plastic packaging.
Example: VidePak’s efforts to incorporate recycled polypropylene have significantly reduced the environmental impact of their production, while still delivering strong and durable bags for their customers.
Key Features and Specifications of Open Mouth PP Bags
Feature | Specification | Benefit |
---|---|---|
Material | Polypropylene, BOPP Laminates, Recycled Polypropylene | Strong, durable, and eco-friendly. |
Strength | Multi-layered construction, high tensile strength | Ideal for heavy-duty applications. |
Customization | Various sizes, printing options, color choices | Meets diverse industry needs and enhances branding. |
Sewing Technology | Automated, high-precision sewing | Consistent quality and faster production speeds. |
Energy Efficiency | Solar-powered production | Reduced energy costs and lower environmental impact. |
FAQs
Q1: How are Open Mouth PP Bags different from other types of PP bags?
Open Mouth PP Bags have an open top, making them easy to fill and seal. They can be customized in size, strength, and material, making them ideal for various applications across industries.
Q2: What are the environmental benefits of Open Mouth PP Bags?
These bags can be made from recycled polypropylene, and manufacturers are increasingly using renewable energy sources, like solar power, to reduce the environmental impact of production.
Q3: Can Open Mouth PP Bags be customized?
Yes, Open Mouth PP Bags can be customized in terms of size, strength, and printing, making them suitable for different industries like agriculture, chemicals, and food packaging.
Conclusion
The development of Open Mouth PP Bags has been driven by advancements in technology, materials, and cost control. With the rise of automation and energy-efficient practices, these bags have become more durable, cost-effective, and sustainable. As the packaging industry continues to evolve, Open Mouth PP Bags offer an efficient, eco-friendly solution for a wide range of applications.
For more on sustainable packaging practices, check out this article on embracing sustainability and the role of industrial woven packaging.