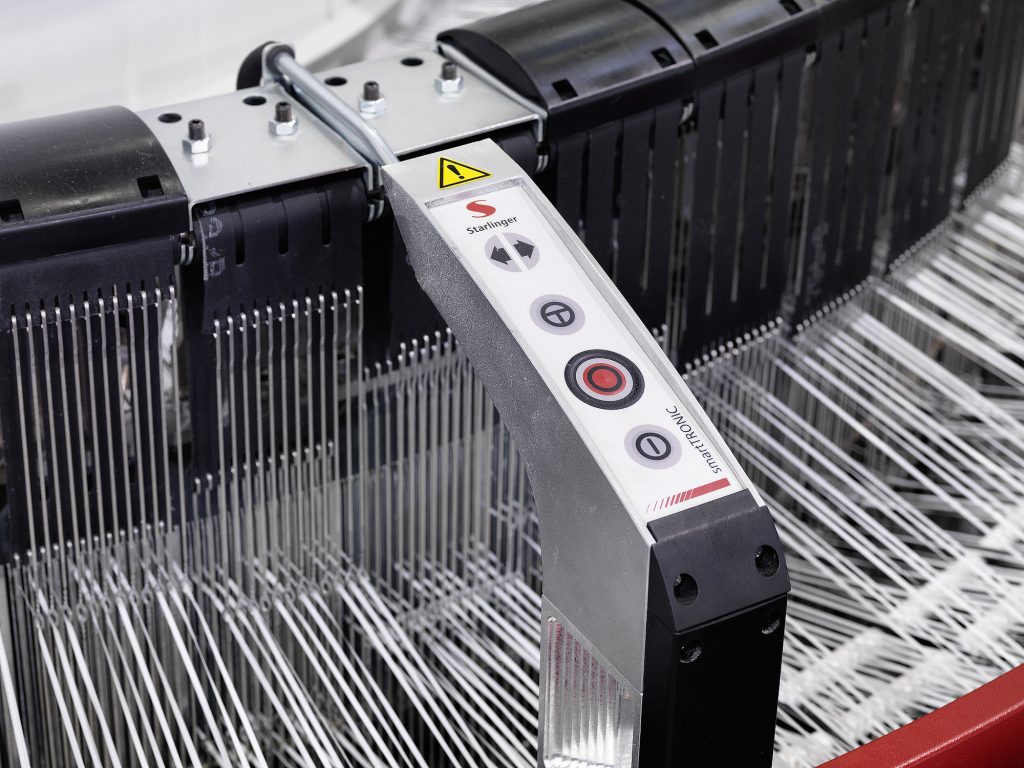
Polypropylene (PP) bags have undergone significant evolution, revolutionizing packaging across industries. The innovative designs, enhanced manufacturing techniques, and customization capabilities of these bags make them indispensable. This article delves into their history, technological advancements, applications, and how they contribute to efficient logistics and sustainability.
Milestones in the Evolution of Polypropylene Bags
- Inception and Adoption (1950s-1980s)
- Material Discovery: Polypropylene polymer was discovered in the 1950s, providing a lightweight and durable material for bags.
- Adoption in Industries: PP bags started replacing traditional jute and paper bags, thanks to their strength and moisture resistance.
- Technological Breakthroughs (1990s-2010s)
- BOPP Film Lamination: Introduced in the 1990s, BOPP (Biaxially Oriented Polypropylene) improved bag aesthetics and printability.
- Valve Bags: Enhanced filling speed and reduced wastage in industrial applications.
- Modern Innovations (2010s-Present)
- Form-Fill-Seal (FFS) Technology: Automated filling processes for tubular PP woven bags, increasing production efficiency.
- Eco-Friendly Options: Transparent woven bags and bio-based polymers address environmental concerns.
Advantages of Modern Polypropylene Bags
Feature | Benefit |
---|---|
Lightweight | Reduces transportation costs. |
Durability | Offers resistance to tears and punctures, ensuring safe transit. |
Custom Printing | Enhances branding opportunities. |
Moisture Resistance | Keeps contents dry and safe, especially in agricultural and chemical applications. |
Eco-Friendliness | Recyclable materials align with sustainability goals. |
Applications of PP Bags in Key Industries
- Agriculture
PP woven bags are widely used for packaging grains, fertilizers, and seeds. Their UV protection ensures product integrity during outdoor storage. - Construction
Valve and moisture-proof bags transport materials like cement and sand efficiently while reducing spillage. - Food Industry
Transparent and breathable PP bags are ideal for flour, sugar, and pet food packaging. - Waste Management
Waterproof and laminated PP bags assist in waste segregation and recycling initiatives.
For a detailed exploration of how PP bags enhance agricultural logistics, visit our insights on FFS roll woven bags in agriculture.
FAQs: Addressing Key Questions
Q1: What are the customization options for PP bags?
- Customization includes size, color, printing designs, lamination, and valve types.
Q2: How are PP bags contributing to sustainability?
- Recyclable designs, reduced use of virgin materials, and bio-degradable variants support sustainability.
Q3: Are PP bags suitable for high-moisture environments?
- Yes, laminated and moisture-resistant variants ensure product safety in wet conditions.
Q4: How does the FFS system improve efficiency?
- By automating filling, sealing, and packaging processes, FFS systems reduce labor and material handling costs.
The Role of Advanced Manufacturing Techniques
- Starlinger Technology
- Advanced looms and lamination machines enhance precision and production speed.
- Fine Yarn Technology
- Enables lightweight yet durable designs, reducing environmental impact.
- Co-Extrusion Blown Film Processes
- Adds multi-layered protection for specialized applications.
For insights into innovative manufacturing methods, explore laminated woven bags with co-extrusion processes.
Future Trends in Polypropylene Bags
- Eco-Friendly Materials
- Increased adoption of biodegradable polymers and recycled PP.
- Smart Packaging
- Incorporation of RFID tags for better inventory management.
- Improved Aesthetics
- Enhanced print technologies for vibrant and detailed designs.
- Global Standards Compliance
- Certifications such as ISO and FSC are becoming essential in export markets.
By embracing these advancements, businesses can optimize packaging efficiency while reducing environmental impact. The evolution of PP bags exemplifies the fusion of innovation, sustainability, and practicality in modern packaging solutions.