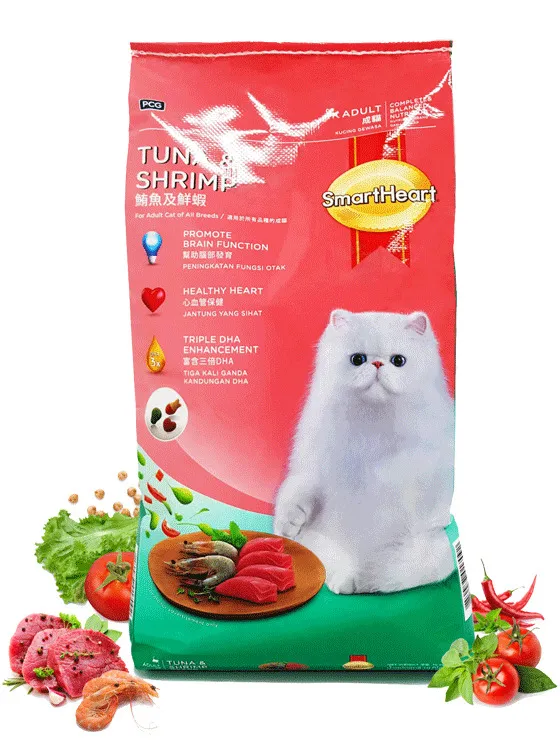
Introduction
In the ever-evolving landscape of packaging, Printed BOPP Woven Bags have carved out a significant niche. Combining the strength of woven polypropylene (PP) with the visual appeal of high-quality printing, these bags serve a multitude of industries—from agriculture to retail. This article explores the historical development of Printed BOPP Woven Sacks, focusing on the technological advancements, material innovations, and cost control strategies that have shaped their production. Additionally, we will look into future trends in automation and technology that promise to revolutionize this sector.
Understanding Printed BOPP Woven Bags
Before diving into the history and future trends, it’s essential to understand what Printed BOPP Woven Bags are and how they differ from traditional woven bags.
- Material Composition: BOPP (Biaxially Oriented Polypropylene) is a type of plastic film that is stretched in both directions to improve its strength and clarity. When laminated onto woven PP fabric, it enhances the bag’s durability and printability.
- Applications: These bags are widely used in packaging agricultural products, food items, chemicals, and consumer goods due to their robustness and aesthetic appeal.
- Visual Appeal: High-resolution printing allows for vibrant colors and detailed images, making these bags not only functional but also effective marketing tools.
Historical Development of Printed BOPP Woven Bags
1. Early Beginnings: The Rise of Polypropylene
The history of BOPP Woven Bags dates back to the 1970s when polypropylene was first commercialized. Initially, woven polypropylene bags were simple, unprinted sacks used mainly for agricultural and industrial applications. However, as the demand for more sophisticated packaging solutions grew, manufacturers began to explore the potential of BOPP film for lamination and printing.
2. Technological Advances in Printing
In the 1980s and 1990s, advances in printing technology dramatically changed the landscape for Printed Woven Bags. Traditional printing methods, like flexography, were enhanced with newer technologies such as gravure and digital printing. These advancements allowed for:
- High-Quality Imagery: The ability to print intricate designs and logos directly onto the bag, increasing brand visibility.
- Color Variety: The incorporation of multiple colors became feasible, appealing to a broader audience.
3. Material Innovation
The introduction of BOPP film marked a significant shift in material science. BOPP is known for its strength, clarity, and resistance to moisture. This film allows for:
- Moisture and Dust Protection: Essential for industries that deal with granular or powdery products.
- Extended Shelf Life: BOPP’s barrier properties help preserve the quality of the contents for longer periods.
4. Cost Control Strategies
As demand for Printed BOPP Woven Sacks increased, manufacturers implemented several cost control measures:
- Bulk Production: Mass production techniques were adopted, reducing the cost per unit.
- Supply Chain Optimization: Collaborating with suppliers to ensure a steady and cost-effective supply of raw materials.
- Waste Reduction: Utilizing advanced machinery that minimizes material waste during the production process.
Current Trends and Future Outlook
1. Automation in Production
With the advent of Industry 4.0, automation is becoming increasingly prevalent in the production of BOPP Woven Bags. Modern manufacturing facilities are integrating:
- Robotic Systems: For tasks such as material handling and packaging, which improves efficiency and reduces labor costs.
- Smart Manufacturing: Utilizing IoT (Internet of Things) devices to monitor production lines, ensuring optimal operation and reducing downtime.
2. Sustainability Concerns
The global shift toward sustainability is influencing the production of Printed Woven Bags. Manufacturers are exploring:
- Recyclable Materials: Developing BOPP films that can be recycled, addressing environmental concerns.
- Eco-Friendly Inks: Utilizing water-based or soy-based inks for printing, reducing the environmental impact.
3. Customization and Flexibility
As consumer preferences become more diverse, the need for customization in Printed BOPP Woven Bags is growing. Manufacturers are:
- Offering Shorter Runs: This enables smaller brands to produce custom-designed bags without incurring excessive costs.
- Enhancing Design Capabilities: Using digital printing technologies that allow for quick changes in designs and branding.
Key Features and Technical Parameters
To better understand the offerings of Printed BOPP Woven Bags, here are some essential technical parameters:
Feature | Description |
---|---|
Material | BOPP laminated woven polypropylene |
Thickness | Typically ranges from 50 to 120 microns |
Printing Quality | High-resolution, full-color printing available |
Strength | Excellent tensile strength, suitable for heavy-duty applications |
Moisture Resistance | BOPP film provides superior protection against moisture and dust |
Customization Options | Variety of sizes, colors, and printing designs available |
Eco-Friendly Options | Recyclable materials and environmentally friendly inks available |
Conclusion
The evolution of Printed BOPP Woven Bags reflects a dynamic interplay of technology, material innovation, and market demand. From their humble beginnings in the 1970s to the sophisticated, highly functional packaging solutions they are today, these bags have undergone significant transformations.
Looking forward, automation and sustainability will play pivotal roles in the future of this industry. As manufacturers strive to meet the challenges of a rapidly changing market, Printed BOPP Woven Bags will continue to evolve, offering consumers a perfect blend of strength, aesthetic appeal, and environmental responsibility.
By embracing these changes, manufacturers can not only enhance their product offerings but also contribute positively to the environment and consumer satisfaction. The journey of BOPP Woven Bags is far from over, and the future promises even greater advancements and innovations in this essential sector of the packaging industry.