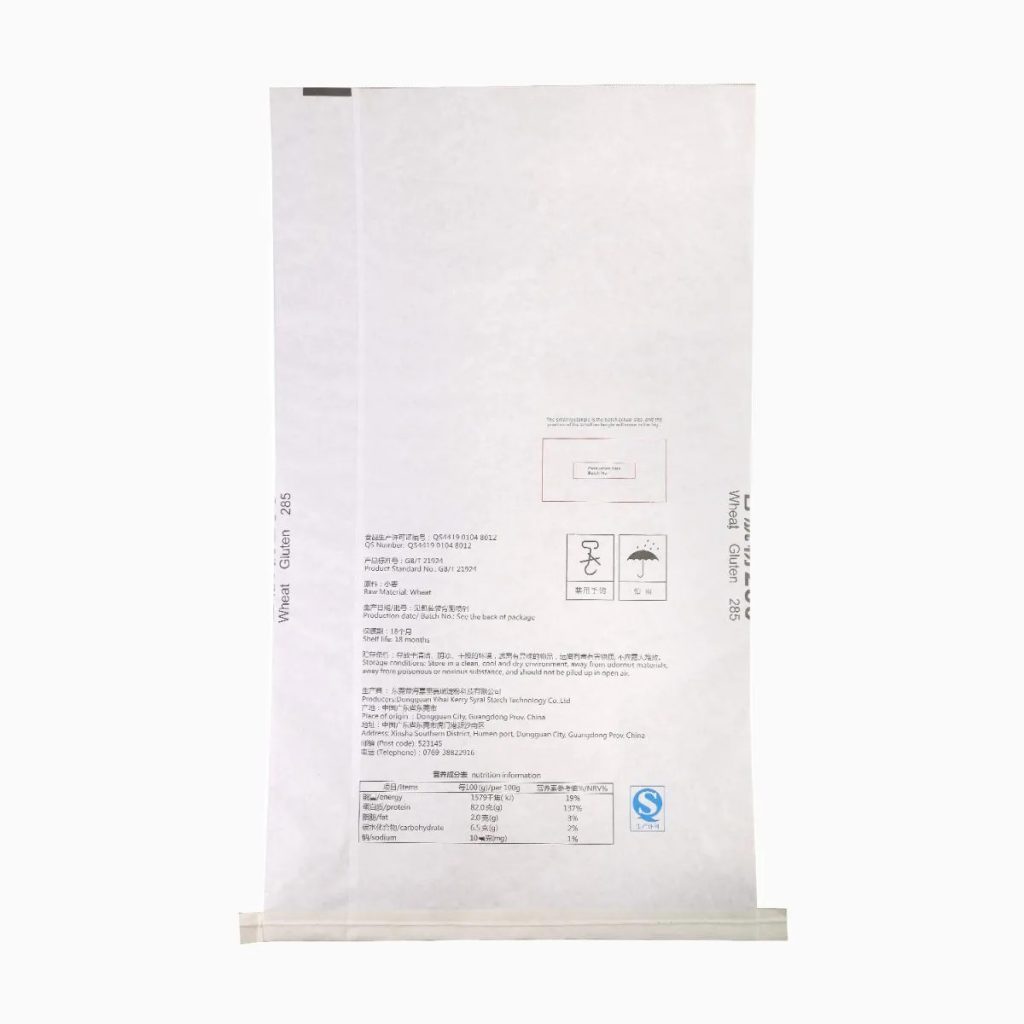
In recent years, there has been a significant shift towards sustainability in the packaging industry, with Recyclable PP bags taking the lead as a prominent eco-friendly solution. These Recyclable PP sacks are being increasingly used in various industries, from agriculture to construction, due to their durable, lightweight, and versatile nature. The focus on Recyclable Woven Bags has intensified, as they present a sustainable alternative to single-use plastics and offer long-lasting utility. Woven Recyclable Bags made from polypropylene (PP) are at the forefront of this revolution, offering a combination of environmental benefits and functional performance.
To achieve high levels of durability and flexibility in PP Woven Bags, one must understand the advanced manufacturing processes behind them. One critical factor in improving the performance of these Recyclable PP bags is the weaving technique, particularly the use of Starlinger and W&H machinery from Austria and Germany, respectively. The integration of these advanced machines has elevated the quality, speed, and efficiency of production, providing a competitive edge to companies like VidePak in the global market.
Key Product Parameters of Recyclable PP Bags
Below is a table showcasing the specifications of the Recyclable PP bags produced using advanced technology:
Parameter | Value |
---|---|
Material | 100% virgin PP (Polypropylene) |
Bag Type | Recyclable PP Sacks |
Weaving Technique | Starlinger Circular Looms |
Bag Sizes | Customizable (10kg to 1000kg) |
Printing Options | Multi-color printing |
Laminate Options | BOPP (Biaxially Oriented Polypropylene) |
Sealing Technology | Ultrasonic Sealing |
UV Resistance | High (UV stabilized) |
Durability | High tensile strength |
Flexibility | High (great flexibility for easy handling) |
Recyclability | 100% recyclable |
The Role of Starlinger and W&H in Manufacturing Excellence
The production of Recyclable PP bags relies heavily on the technology used during the manufacturing process. The Starlinger machines, originating from Austria, play a pivotal role in the weaving of PP fabric, which is the core material for PP Woven Bags. The machines are designed for maximum automation, achieving line speeds of over 200 meters per minute. This high level of automation ensures the consistency and precision of every woven bag produced, while reducing the human error factor and improving overall production efficiency.
On the other hand, the W&H (Windmöller & Hölscher) machines, coming from Germany, focus on advanced printing and lamination technology. These machines enable multi-color printing on the woven fabric, giving the Recyclable Woven Bags vibrant and customizable designs that cater to brand-specific requirements. The integration of high-speed printing technology further enhances the appeal of these bags, making them suitable for a wide range of applications, including retail packaging and bulk transportation.
The precision and efficiency of the Starlinger and W&H machines have significantly raised the standard of Woven Recyclable Bags production, ensuring that the final products not only meet but exceed industry standards for strength, flexibility, and sustainability. As these machines are highly automated and interlinked, production efficiency is maximized, leading to faster turnaround times and lower costs for manufacturers, which ultimately benefits consumers.
How Filament Technology Impacts Durability and Flexibility
A critical component of Recyclable PP bags is the filament technology used in their production. The use of fine yarns in the weaving process allows for greater tensile strength, which directly impacts the durability of the final product. The fine yarns are woven together to form a robust yet flexible fabric, ensuring that the PP Woven Bags can withstand high-pressure conditions, heavy loads, and extended usage without losing their structural integrity.
Additionally, the flexibility of Woven Recyclable Bags is crucial, especially for applications where the bags need to be handled frequently, stacked, or transported. The flexibility of these bags allows them to conform to various shapes and sizes, making them highly adaptable for different industrial applications. This combination of flexibility and strength makes Recyclable PP sacks ideal for diverse industries, including agriculture, construction, food packaging, and more.
Moreover, the fine filament technology, in combination with the state-of-the-art weaving and lamination techniques, ensures that the Recyclable Woven Bags offer resistance to puncturing, abrasion, and tearing. This is particularly important in sectors such as construction, where bags need to endure rough handling and exposure to harsh environments. With high UV resistance, these bags also maintain their strength and flexibility even when exposed to sunlight for extended periods.
The Role of Automation in Production Efficiency
The automation level in PP Woven Bags production, facilitated by the use of advanced Starlinger and W&H machinery, has significantly impacted overall production efficiency. The ability to produce high-quality bags with minimal human intervention not only reduces labor costs but also ensures consistent product quality.
For instance, the machines’ multi-machine coordination allows for faster production speeds without compromising the quality of the bags. The integration of automated cutting, sealing, and printing processes ensures that each Recyclable PP bag is manufactured to precise specifications, meeting the required standards for strength, durability, and environmental compliance.
This level of automation also facilitates flexibility in production. Manufacturers can produce small, medium, and large batches of Recyclable Woven Bags in different sizes and designs, catering to a wide range of market demands. The high-speed production lines are capable of producing over 200 bags per minute, enabling manufacturers to meet the increasing demand for sustainable packaging solutions across various industries.
Global Market Impact and Demand for Recyclable Packaging Solutions
As consumers and businesses alike become more environmentally conscious, the demand for sustainable and recyclable packaging solutions has soared. Recyclable PP bags are at the forefront of this shift, as they offer a combination of durability, versatility, and eco-friendliness that meets the needs of industries ranging from agriculture to retail. By using 100% recyclable materials, these bags contribute to waste reduction and promote circular economy principles.
In particular, PP Woven Bags are gaining popularity in industries that require durable, reusable, and cost-effective packaging. The robust nature of these bags makes them ideal for bulk packaging, particularly in sectors such as food, chemicals, and construction. The growing emphasis on sustainability in packaging design, driven by regulations and consumer preference, positions Recyclable Woven Bags as the preferred choice for eco-conscious businesses.
With the integration of high-end equipment from Starlinger and W&H, manufacturers can meet the increasing demand for Woven Recyclable Bags without compromising on production efficiency. As a result, manufacturers like VidePak can provide high-quality, customizable, and sustainable packaging solutions to a global customer base.
Conclusion
The rise of Recyclable PP bags and PP Woven Bags marks a significant milestone in the quest for sustainable packaging solutions. Thanks to technological advancements in weaving and lamination techniques, alongside the use of high-end machinery from Starlinger and W&H, the production of these bags has reached new heights of efficiency and quality. By combining durability, flexibility, and recyclability, Recyclable Woven Bags are set to play a crucial role in the global shift toward more sustainable packaging practices.
For further information on Recyclable PP bags, check out this article on industrial woven packaging bags, and for a deeper dive into PP Woven Bags, you can explore this page on laminated woven fabric bags.