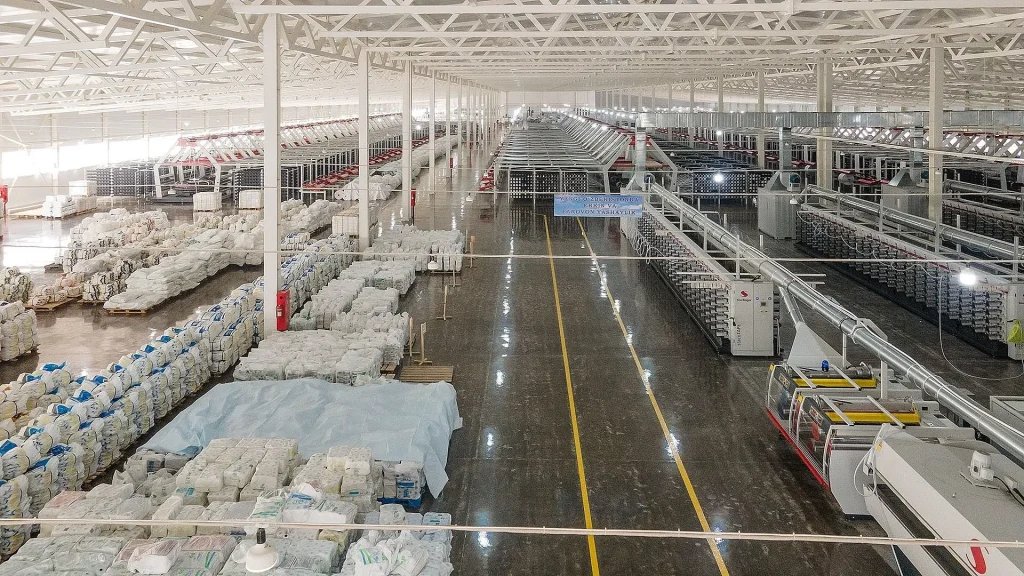
The sewn open mouth PP bag industry has undergone transformative advancements over the past two decades, driven by innovations in weaving technology, material science, and sustainability practices. VidePak, a global leader in woven packaging solutions since 2008, exemplifies this progress with its cutting-edge production capabilities, including 100+ circular looms, 16 extrusion lines, and 30+ lamination machines, enabling the creation of high-performance bags tailored to diverse industrial needs. This article explores the evolution of sewn open mouth PP bags, focusing on technological milestones, material enhancements like matte, pearlescent, and transparent laminated finishes, and emerging trends shaping the future of packaging.
1. Technological Advancements in Sewn Open Mouth PP Bag Production
1.1 Precision Weaving and Fine-Yarn Technology
Modern sewn open mouth PP bags leverage fine-yarn weaving technology, where single-filament widths range between 1.8 mm and 2.3 mm. This precision ensures a smoother fabric surface, enhancing print clarity and tensile strength. VidePak’s adoption of Austrian Starlinger machinery enables the production of 120–150 bags per hour per loom, with fabric densities exceeding 12×12 strands per inch for superior tear resistance.
1.2 Automated Sewing and Quality Control
Automated sewing systems have replaced manual stitching, reducing human error and ensuring uniform seam strength of 30–35 N/cm. VidePak integrates laser-guided alignment systems to achieve ±1 mm stitching accuracy, critical for heavy-duty applications like cement or fertilizer packaging.
2. Material Innovations: Enhancing Functionality and Aesthetics
2.1 Advanced Lamination Techniques
VidePak offers three premium laminated finishes:
- Matte Lamination: Reduces glare for improved label readability, ideal for retail environments.
- Pearlescent Lamination: Adds a metallic sheen, enhancing brand visibility in competitive markets.
- Transparent Lamination: Provides moisture resistance (≤0.05 g/m²/24h) while showcasing product contents.
These laminates are applied using extrusion-coating technology, bonding PP layers at 280–300°C for optimal adhesion.
2.2 Sustainable Material Blends
To align with global eco-friendly demands, VidePak incorporates 30% recycled PP into its fabric matrix without compromising tensile strength (≥1,200 N/5 cm). Additionally, bio-based additives reduce carbon footprints by 15% compared to conventional blends.
3. Future Trends: Smart Packaging and Customization
3.1 RFID Integration and Traceability
Emerging trends include RFID-enabled tags embedded into seams, enabling real-time tracking across supply chains. VidePak’s pilot projects demonstrate a 20% reduction in logistical errors for agricultural exporters using this technology.
3.2 Customizable Design Solutions
Clients demand bespoke printing options, such as 8-color HD flexography, to align with brand aesthetics. VidePak’s 30+ printing machines support gradients, micro-text, and UV-resistant inks, ensuring designs remain vibrant for 5+ years outdoors.
4. VidePak’s Competitive Edge
With 568 employees and annual sales of $80 million, VidePak combines scale with agility. Key strengths include:
- Rapid prototyping: 7-day sample turnaround for custom designs.
- Global compliance: BRCGS, ISO 9001, and FDA certifications.
- Diverse product range: From BOPP laminated bags to kraft-paper hybrids, catering to food, chemicals, and construction sectors.
FAQs: Addressing Client Concerns
Question | Answer |
---|---|
What is the lead time for bulk orders? | 18–25 days for 20,000+ units, depending on customization. |
Are your bags recyclable? | Yes, all products comply with EU REACH and US EPA standards. |
Can you handle multi-material laminates? | We specialize in PP/PE, PP/PET, and PP/aluminum foil combinations. |
References
- VidePak Official Website: www.pp-wovenbags.com
- Email: info@pp-wovenbags.com
- Industry Reports: Global Woven Packaging Market Analysis (2024), Sustainable Materials in Packaging (2023)
For further insights into BOPP laminated woven bags, explore our dedicated resource on BOPP Laminated Woven Bags: Branding and Market Dynamics. To learn about advanced printing techniques, visit Custom Printed Woven Bags: The Art of Print and Precision.
Final Word: The sewn open mouth PP bag sector is poised for exponential growth, driven by sustainability mandates and technological leaps. VidePak’s commitment to R&D, scalability, and client-centric innovation ensures it remains at the forefront of this evolution.