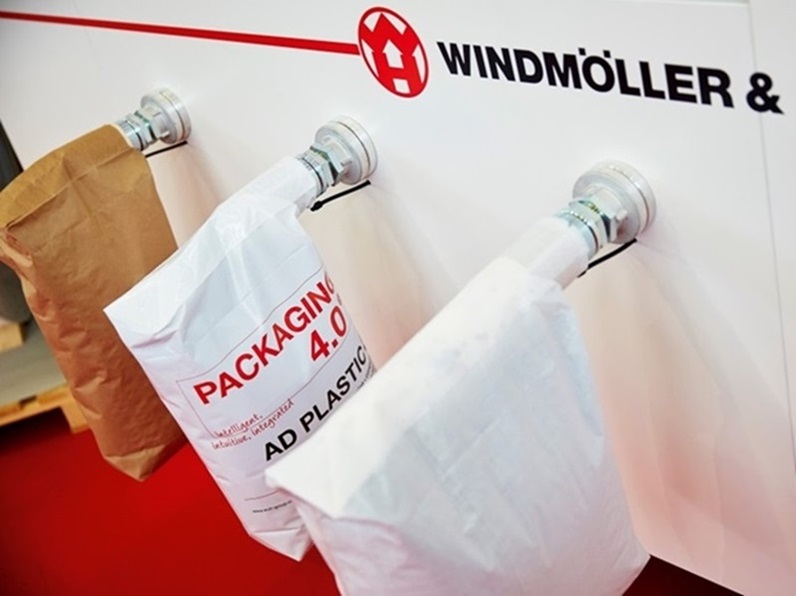
Multi-wall woven bags are essential in today’s packaging world. These durable, versatile bags are used in a wide range of industries, including agriculture, chemicals, and construction. With increasing focus on sustainability and customization, the future of multi-wall woven bags looks promising. This article will explore how multi-wall woven bags are evolving to meet market demands, with a focus on sustainability, customization, and advanced manufacturing techniques.
1. Why Multi-Wall Woven Bags Are Crucial
Multi-wall woven bags are known for their strength and versatility. They are made from several layers of materials, typically polypropylene (PP) or kraft paper, which make them tough enough to hold heavy products like cement, grains, and fertilizers. These bags have become a preferred option for many industries because they are reliable and cost-effective.
With sustainability at the forefront of consumer preferences, businesses are looking for eco-friendly packaging solutions. Multi-wall woven bags stand out because they are made from recyclable materials and are reusable. This makes them a better alternative to single-use plastic bags. For example, in the agricultural industry, bags used for grains and pet food are often recycled, reducing waste.
2. Manufacturing Processes: How to Achieve Durability and Customization
The production process of multi-wall woven bags plays a key role in determining their quality and performance. Companies like VidePak are using advanced technology to improve bag strength, functionality, and customization options. The choice of bag-making techniques, materials, and sealing methods are critical in meeting the diverse needs of customers. Let’s explore these key factors.
2.1 Bag-Making Techniques: Bottom Sewing, Heat Sealing, and Ultrasonic Welding
The sealing method used for a woven bag affects its durability and the type of products it can carry. Here are three common techniques:
- Bottom Sewing: This is the most traditional and cost-effective method, where the bottom of the bag is sewn shut. This technique is ideal for heavier items like cement or sand, where a strong yet basic closure is sufficient. However, it doesn’t provide moisture resistance, which could be a problem for products like food.
- Heat Sealing: Heat sealing involves fusing the layers of the bag with high temperatures, creating an airtight and moisture-resistant seal. This is crucial for packaging products like chemicals or food items that need to be protected from the environment. The heat-sealed bags are stronger and more durable, making them suitable for a wider range of industries.
- Ultrasonic Welding: This advanced method uses sound waves to bond the layers of the bag without any thread or glue. Ultrasonic welding provides an extremely strong, leak-proof seal, ideal for packaging fine powders, pharmaceuticals, or other sensitive products that require extra protection. The advantage of this method is that it offers precision and ensures no leakage.
2.2 Choosing the Right Thread and Stitch Density
The strength of a multi-wall woven bag also depends on the thread used for stitching. Polypropylene (PP) thread is commonly used because it is strong, resistant to UV rays, and does not degrade easily in harsh conditions.
Another important factor is the stitch density—the number of stitches per unit area. A higher stitch density means that the bag is more tightly sewn, making it less likely to tear under pressure. For instance, bags designed for bulk materials like sand or gravel often use a lower stitch density, while bags used for retail packaging might have a higher stitch density to ensure both strength and a neat appearance.
2.3 Customizing the Bag Opening: Open Top, Valve, and Heat Sealed
The design of the bag opening is another area where customization is key. Different types of openings serve different functions:
- Open Top: Open-top bags are simple to fill and are often used for bulk products like grains or pet food. These bags are easy to seal after filling, but they may not be ideal for moisture-sensitive products.
- Valve Bags: Valve bags feature a valve at the top that allows for efficient filling while preventing spillage. These bags are widely used for products like fertilizers or animal feed. The valve provides a secure closure, making the bags less likely to leak.
- Heat Sealed Bags: Heat-sealed bags are used for products that require airtight protection. These bags are sealed at the top, preventing moisture and contaminants from entering. This makes them ideal for food and pharmaceutical packaging, where product integrity is essential.
3. Customization: Meeting Market Demands
As industries become more competitive, the demand for customized packaging has grown. Multi-wall woven bags can be tailored to meet specific requirements, such as material choices, printing, and bag size.
3.1 Material Choices
Multi-wall woven bags can be made from a variety of materials, depending on the needs of the product being packaged. For example, Kraft paper laminated with woven fabric creates a stronger, more durable bag that also has a premium appearance. This combination is often used for packaging pet food or other consumer goods. The laminated material is also moisture-resistant, making it suitable for products that need extra protection during transportation and storage.
3.2 Custom Printing
Another major customization option is printing. With advanced printing technology like flexographic and rotogravure printing, companies can print their logos, product information, and other details directly onto the bags. This allows businesses to improve their branding and ensure compliance with labeling regulations. For instance, a company selling organic grains might print a logo that emphasizes its eco-friendly practices, which helps attract environmentally conscious consumers.
4. Product Parameters and FAQs
Here’s a quick summary of the key parameters for multi-wall woven bags, along with answers to some common questions:
Parameter | Specification |
---|---|
Material | Polypropylene (PP), Kraft Paper |
Sealing Techniques | Bottom Sewing, Heat Sealing, Ultrasonic Welding |
Thread Density | 4-6 for bulk materials, finer for retail |
Bag Opening Types | Open Top, Valve, Heat Sealed |
Custom Printing | Up to 6 colors |
Moisture Resistance | Available with laminated options |
FAQs:
Q1: What are the common uses of multi-wall woven bags?
A1: These bags are commonly used in packaging products like grains, pet food, chemicals, and cement. Their versatility and strength make them suitable for many industries.
Q2: Can multi-wall woven bags be customized?
A2: Yes, these bags can be customized in terms of material, printing, bag design, and sealing methods to suit the specific needs of the product and brand.
Q3: How do I choose the right bag for my product?
A3: The type of bag depends on the nature of the product. For dry bulk materials, open-top or valve bags are a good choice. For moisture-sensitive products, heat-sealed bags provide extra protection.
Conclusion
The future of multi-wall woven bags is bright as businesses continue to embrace sustainability and customization. Through advanced manufacturing techniques and a focus on eco-friendly materials, multi-wall woven bags are evolving to meet the needs of diverse markets. Whether it’s using heat-sealing for moisture resistance or custom printing for branding, these bags offer an ideal solution for companies looking to package products safely, efficiently, and sustainably.
For more information on industrial woven bags and sustainable packaging, check out Industrial Woven Packaging Bags: Aligning with Policies and ESG Standards and Kraft Paper Bags Laminated with Woven Fabric: Advanced Production Processes and VidePak’s Expertise.