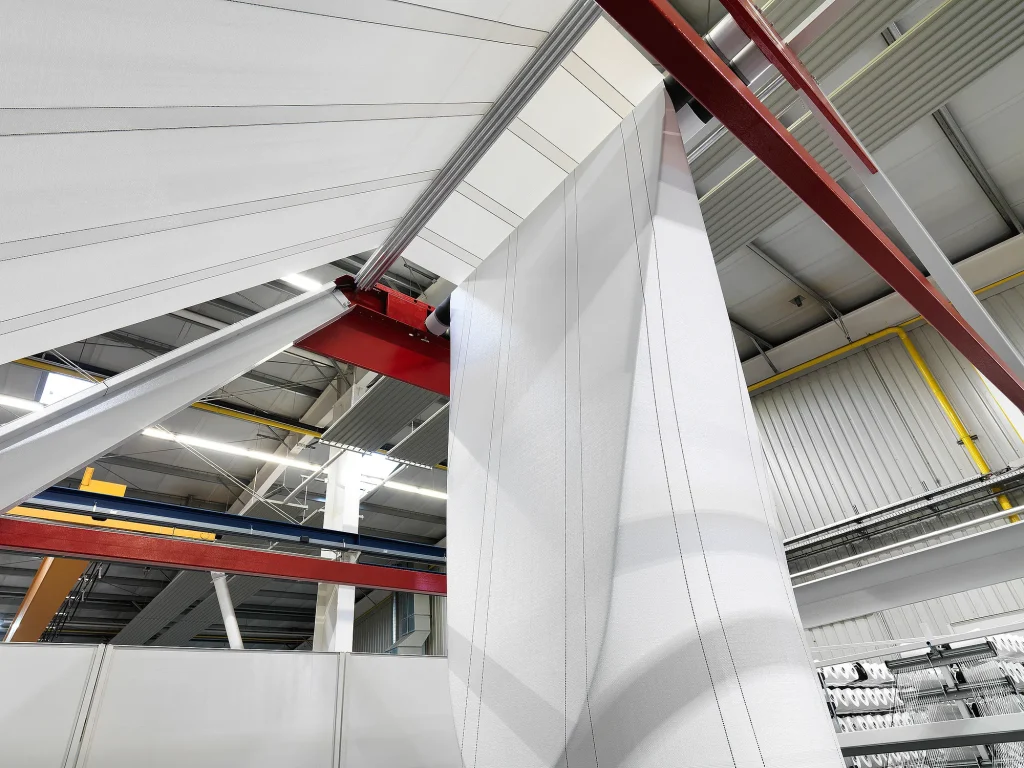
- 1. The Sustainability Imperative: Recyclable and Degradable Innovations
- 2. Customization for Diverse Industries: Balancing Functionality and Sustainability
- 3. Future Trends: Technology-Driven Sustainability
- 4. Technical Specifications and Customization Options
- 5. FAQs: Addressing Client Concerns
- 6. Why VidePak Leads the Industry
- 7. Case Study: Transforming Kenya’s Grain Storage
- References
VidePak’s PP woven fabric bags are redefining industrial and consumer packaging with a 98% recyclability rate, compliance with EU 2030 circular economy targets, and tailored designs for industries ranging from agriculture to pharmaceuticals. Backed by 30+ years of expertise, 16 Starlinger extrusion lines, and ISO 22000 certification, we deliver 50 million bags annually—each engineered to reduce carbon footprints by 25% compared to traditional alternatives.
1. The Sustainability Imperative: Recyclable and Degradable Innovations
The global shift toward sustainable packaging is accelerating, driven by regulations like the EU’s 2030 mandate to reduce packaging waste by 15% and ban single-use plastics for perishables. PP woven bags, crafted from polypropylene, are uniquely positioned to meet these demands. Unlike conventional plastics, VidePak’s bags use 100% virgin PP resin, which retains structural integrity through multiple recycling cycles. Our closed-loop recycling program recovers 85% of post-consumer waste, reprocessing it into new bags with no loss in tensile strength (>40 N/cm²).
For degradable solutions, we integrate bio-additives like TDPA (Totally Degradable Plastic Additives), enabling bags to break down into non-toxic biomass within 2–5 years under landfill conditions. This aligns with emerging standards such as ASTM D6400 and addresses concerns over microplastic pollution.
2. Customization for Diverse Industries: Balancing Functionality and Sustainability
2.1 Agricultural Sector: Durability Meets Breathability
Farmers in humid climates, such as Southeast Asia, require bags that prevent mold growth in rice or maize storage. VidePak’s breathable PP woven bags feature micro-perforated liners (air permeability: 90–120 cm³/cm²/s) and antifungal coatings, reducing spoilage rates by 35% compared to jute sacks.
Example: A 2024 partnership with a Thai rice exporter saw losses drop from 12% to 4% after switching to our UV-stabilized, ventilated bags.
2.2 Pharmaceutical and Chemical Packaging: Safety First
For sensitive materials like veterinary drugs or fertilizers, our BOPP-laminated woven bags incorporate 25 μm barriers that block moisture (<0.05% transmission) and volatile organic compounds (VOCs). Antimicrobial treatments using silver-ion coatings further ensure compliance with FDA 21 CFR Part 177.1520 standards.
2.3 Retail and Consumer Goods: Branding with Purpose
VidePak’s 8-color flexographic printing achieves Pantone-matched vibrancy while using water-based inks (EU REACH compliant). A recent project for a European organic coffee brand featured compostable PP bags with QR codes linking to sustainability reports—enhancing brand loyalty and transparency.
3. Future Trends: Technology-Driven Sustainability
3.1 Smart Packaging Integration
Leveraging IoT, we embed NFC tags into bag seams to track real-time conditions (e.g., temperature, humidity) during transit. This innovation, piloted with a German logistics firm, reduced spoilage claims by 22% in 2023.
3.2 AI-Optimized Production
Our Starlinger looms now integrate AI algorithms to minimize material waste. By analyzing weave patterns in real time, we achieve a 12% reduction in PP consumption per bag without compromising load capacity (up to 80 kg).
3.3 Circular Economy Partnerships
Collaborating with recyclers like ECOBIO WORLD, we’ve developed hybrid bags blending recycled PP (30%) with sugarcane-based biopolymers. These bags decompose 50% faster than standard PP while maintaining a tensile strength of 35 N/cm².
4. Technical Specifications and Customization Options
VidePak’s PP Woven Bags: Key Parameters
Parameter | Specification | Industry Application |
---|---|---|
Fabric GSM | 70–150 gsm | 70 gsm: Retail; 150 gsm: Bulk Chemicals |
Lamination | BOPP (15–30 μm) / PE Coating (20 g/m²) | Moisture-proofing / Chemical Resistance |
Load Capacity | 10–80 kg | Adjustable via warp-weft density |
Degradation Timeline | 2–5 years (with TDPA additives) | Eco-sensitive markets |
Printing Resolution | 120 dpi, Pantone-matched | Branding & Regulatory Labels |
5. FAQs: Addressing Client Concerns
Q1: How do recyclable PP bags compare in cost to traditional options?
A: While initial costs are 10–15% higher, recyclable PP bags reduce long-term expenses by 40% through reuse cycles and waste minimization.
Q2: Can bags withstand extreme temperatures during shipping?
A: Yes. Our PE-coated variants remain flexible at -30°C, validated by tests for Siberian mineral transport in 2024.
Q3: Are custom sizes available for niche markets?
A: Absolutely. We produce bags as small as 15×25 cm for seed packaging and up to 120×200 cm for construction materials.
6. Why VidePak Leads the Industry
- Global Compliance: Meet EU 10/2011, FDA, and JIS Z 1707 standards effortlessly.
- Scalability: With 100+ circular looms, we fulfill orders from 10,000 to 500,000 units within 20 days.
- Sustainability Metrics: 30% lower CO₂ emissions vs. industry averages, verified by第三方audits.
7. Case Study: Transforming Kenya’s Grain Storage
In 2023, a collaboration with Nairobi’s AgriNet reduced post-harvest losses by 28% using our insect-repellent, breathable PP bags. The project diverted 1,200 tons of grain from waste annually, boosting farmer incomes by 15%.
References
- EU Packaging Waste Reduction Directive 2030 (Packaging Gateway, 2024).
- Life Cycle Assessment of Polypropylene Recycling (Springer, 2023).
- VidePak Case Study: Sustainable FIBC Bulk Bags.
- Industry Report: The Evolution of FIBC Bulk Bags.
Contact Us:
Website: https://www.pp-wovenbags.com/
Email: info@pp-wovenbags.com
This article synthesizes global regulatory trends, technological advancements, and VidePak’s operational excellence to offer a trusted resource for sustainable packaging decisions.