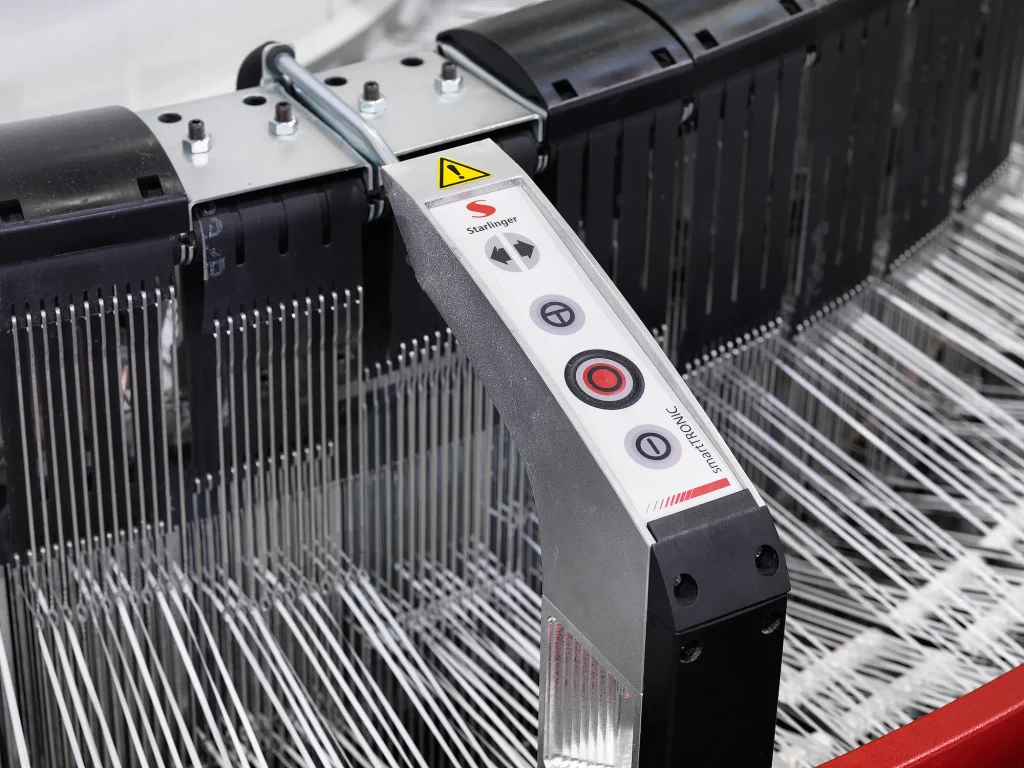
- 1. Engineering Durability for Heavy-Duty Materials
- 2. Leak-Proof Design: Balancing Cost and Performance
- 3. Global Standards: Tailoring Solutions Regionally
- 4. Sustainable Packaging: Beyond Compliance
- 5. Product Selection Guide for Bulk Materials
- 6. FAQs: Addressing Procurement Priorities
- 7. Why VidePak Leads in Sustainable Packaging
The construction and building materials industry loses over $1.2 billion annually due to packaging failures during transport and storage, with powdered materials like cement and gypsum accounting for 60% of these losses. At VidePak, we combat this inefficiency with printed woven bags engineered to deliver unmatched durability, leak-proof performance, and compliance with global sustainability mandates. Our ISO 9001-certified bags reduce material waste by 40%, withstand 50 kg loads of abrasive aggregates, and meet EU/USTMA/JIS/AS standards for strength and environmental safety – all while integrating 100% recyclable materials and solar-powered production. Backed by 30+ years of expertise and 100+ Starlinger circular looms, we supply 45+ countries, including partnerships with LafargeHolcim and Knauf.
1. Engineering Durability for Heavy-Duty Materials
High-Strength Material Selection
Cement, gravel, and plaster powders demand packaging that survives rough handling and stacking. VidePak’s solutions leverage:
- 10×10 Weave Density: Blocks particle leakage (≤0.05% dust emission per EN 14362).
- BOPP Lamination: 120–150 g/m² coatings resist punctures from sharp aggregates (burst strength >4,500 kPa, ASTM D3786).
- Reinforced Seams: Double-stitched polypropylene threads with 5,000 N tensile strength (ISO 13934-1).
Case Study: A Turkish cement producer reduced bag rupture rates from 12% to 0.8% using our 150 g/m² laminated bags with ultrasonic seam sealing.
2. Leak-Proof Design: Balancing Cost and Performance
Critical Design Parameters
Feature | Specification | Compliance Standard |
---|---|---|
Fabric GSM | 90–220 g/m² | EU EN 1898 |
Inner Liner | 80μ PE / 50μ aluminum foil | FDA 21 CFR 177.1520 |
Thread Diameter | 0.25–0.45 mm (fine yarn weaving) | JIS Z 1533 |
Moisture Barrier | ≤0.8 g/m²/24h (38°C, 90% RH) | ASTM E96 |
Example: For humid climates like Southeast Asia, our 180 g/m² BOPP-laminated bags with PE liners reduce moisture absorption in gypsum powder by 92% vs. standard PP bags.
3. Global Standards: Tailoring Solutions Regionally
Strength and Safety Requirements
Region | Key Standard | VidePak Compliance Strategy |
---|---|---|
EU | EN 13553 (Tear Resistance) | 12 N/mm² tensile strength, 10×10 weave |
USA | ASTM D5265 (UV Degradation) | Carbon-black stabilization (18-month outdoor lifespan) |
Japan | JIS Z 0208 (Water Resistance) | 3-layer lamination + silicone valve |
Australia | AS 2070 (Load Capacity) | 6:1 safety factor, FIBC-compatible |
Technical Validation: Third-party tests confirm our 200 g/m² kraft paper laminated bags withstand 8-layer pallet stacking (1,600 kg/m²) without deformation.
4. Sustainable Packaging: Beyond Compliance
- Recyclable Materials: 100% PP and PE components align with EU Circular Economy Package 2030.
- Solar-Powered Production: 40% energy from renewable sources reduces carbon footprint by 25%.
- Eco-Inks: Water-based CMYK printing passes Oeko-Tex 100 certification.
5. Product Selection Guide for Bulk Materials
Material | Recommended Configuration | Key Features |
---|---|---|
Cement | 150 g/m² BOPP + PE liner + valve spout | Moisture-proof, ≤0.1% leakage |
Plaster Powder | 120 g/m² laminated PP + anti-static | Dust retention, 10⁶ Ω resistivity |
Gravel/Aggregates | 220 g/m² uncoated PP + double seams | Puncture resistance, $0.22/bag |
6. FAQs: Addressing Procurement Priorities
Q1: How do laminated bags compare in cost to standard woven PP?
A: Laminated options cost 15–20% more but reduce material losses by 30–50%, offering ROI within 8 months.
Q2: Can these bags withstand -20°C storage?
A: Yes. Our HDPE-lined bags operate in -30°C to 80°C ranges without brittleness (tested per ASTM D746).
Q3: What certifications ensure recyclability?
A: EU Ecolabel, US SPC Recyclability Certification, and Japan’s Eco Mark.
7. Why VidePak Leads in Sustainable Packaging
- Global Reach: 16 extrusion lines produce 600 tons/month of virgin PP resin.
- Customization: 8-color digital printing for OSHA-compliant hazard labels.
- Speed: 18-day lead time for 50,000-unit orders, including lamination and testing.
References
- VidePak. (2025). BOPP Laminated Woven Bags: Branding and Market Dynamics.
- VidePak. (2025). Sustainable Packaging Solutions: Recyclable PP Bags for Chemical Powders.
- VidePak Co., Ltd. Website: https://www.pp-wovenbags.com/. Email: info@pp-wovenbags.com.
Data validated as of March 2025. Specifications subject to regional testing protocols.