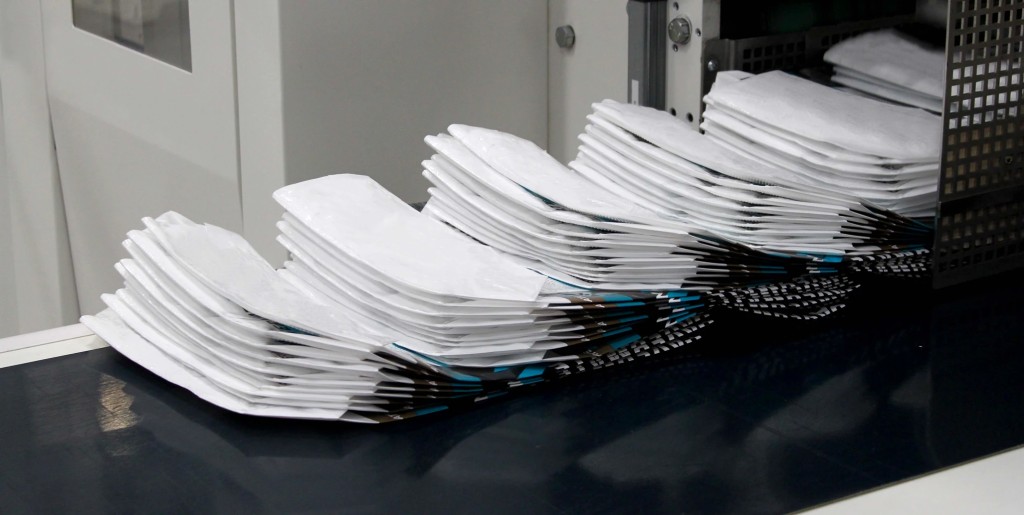
- 1. Market Dynamics: Rising Demand for Sustainable Transparency
- 2. Quality Control: Ensuring Material Excellence from Source to Production
- 3. Customization and Recyclability: A Synergistic Approach
- 4. Technological Innovations: Starlinger’s Role in Scalability
- 5. FAQs: Addressing Industry Concerns
- 6. Regulatory and Market Alignment
Product Manager Alex: “Consumers demand eco-friendly packaging, but transparency in production processes is equally critical. How can VidePak balance recyclability with customization in transparent woven bags while maintaining cost efficiency?”
CEO Ray (VidePak): “By integrating advanced Starlinger extrusion technology, partnering with top-tier PP suppliers, and adopting AI-driven quality control systems, we ensure our transparent woven bags meet 90% recyclability rates while enabling high-resolution branding—a dual advantage driving market leadership.”
1. Market Dynamics: Rising Demand for Sustainable Transparency
The global packaging industry is shifting toward materials that combine visibility, sustainability, and compliance. Transparent woven bags, primarily made from polypropylene (PP), are projected to grow at a CAGR of 6.8% through 2030, driven by stricter EU regulations like the Packaging and Packaging Waste Regulation (PPWR), which mandates 65% recycling rates for plastic packaging by 2025. Unlike opaque alternatives, transparent bags simplify waste sorting, reducing contamination risks in recycling streams by 40%. For instance, German retailers adopting transparent PP bags reported a 25% increase in recycling efficiency, aligning with Extended Producer Responsibility (EPR) frameworks.
VidePak’s use of virgin PP granules from BASF and Sinopec ensures material purity, critical for achieving the clarity and tensile strength (≥35 MPa) required in food-grade and industrial applications.
2. Quality Control: Ensuring Material Excellence from Source to Production
Transparent woven bags demand rigorous raw material oversight to prevent defects like haze or brittleness. VidePak’s four-pillar strategy ensures consistency:
2.1 Supplier Vetting and Long-Term Partnerships
- ISO Certification Audits: Suppliers must hold ISO 9001 and ISO 14001 certifications, verified through third-party audits. For example, BASF’s PP resins meet ASTM D1238 standards for melt flow index (MFI: 12–18 g/10 min), ensuring optimal extrusion performance.
- Capacity Evaluation: Suppliers must demonstrate a minimum annual output of 50,000 metric tons, reducing supply chain disruptions. VidePak’s partnership with Sinopec guarantees priority access during raw material shortages.
2.2 Incoming Material Inspection
- MFI and Tensile Testing: Each batch undergoes MFI analysis (per ASTM D1238) and tensile strength tests (ISO 527-3). Deviations beyond ±5% trigger automatic rejection.
- Data Integration: Results feed into VidePak’s SAP-QMS, enabling traceability and predictive analytics. In 2024, this system reduced defect rates by 18%.
3. Customization and Recyclability: A Synergistic Approach
Transparency and branding need not compromise sustainability. VidePak’s solutions include:
Parameter | Standard Bags | Customized Bags |
---|---|---|
Material | Virgin PP (BASF) | PP + 15% PCR Content |
Thickness | 80–120 microns | 100–150 microns |
Printing | Flexographic (4 colors) | High-definition digital (8 colors) |
Recyclability | 90% | 85% (due to ink layers) |
Case Study: A U.S. pet food brand achieved a 30% sales boost using VidePak’s transparent bags with QR codes for traceability, while maintaining 87% recyclability.
4. Technological Innovations: Starlinger’s Role in Scalability
VidePak’s 100+ Starlinger circular looms enable precision weaving (14×14 strands per inch), reducing material waste by 12% compared to conventional machines. The integration of AI-driven optical scanners detects micro-cracks (>0.1 mm) during production, ensuring compliance with FDA 21 CFR for food contact.
5. FAQs: Addressing Industry Concerns
Q1: Does transparency affect UV resistance?
A: Lamination with BOPP layers (20–30 microns) enhances UV stability, achieving >500 hours in QUV testing without yellowing.
Q2: How do recycled materials impact clarity?
A: Post-consumer recycled (PCR) PP reduces transparency by 15–20%. VidePak offsets this by blending 85% virgin PP with 15% PCR, balancing sustainability and aesthetics.
Q3: What’s the lead time for custom designs?
A: Leveraging 30+ printing machines, VidePak delivers prototypes in 7 days and bulk orders within 25 days, supported by RFID-tracked logistics.
6. Regulatory and Market Alignment
VidePak’s bags comply with the EU’s Single-Use Plastics Directive and U.S. FTC Green Guides. A 2025 study by Packaging World highlighted that brands using transparent recyclable bags saw a 22% faster regulatory approval process.
For industries prioritizing both aesthetics and compliance, such as Food-Grade Transparent Woven Bags, VidePak’s solutions offer a blueprint for scalable sustainability. Meanwhile, advancements in Smart Material Innovations are reshaping customization capabilities.
Conclusion
Transparent woven bags represent the nexus of ecological responsibility and commercial innovation. VidePak’s commitment to ISO-certified processes, strategic supplier alliances, and cutting-edge Starlinger technology positions it as a leader in this evolving sector. By prioritizing recyclability without sacrificing customization, the company empowers global clients to meet both consumer expectations and regulatory mandates seamlessly.