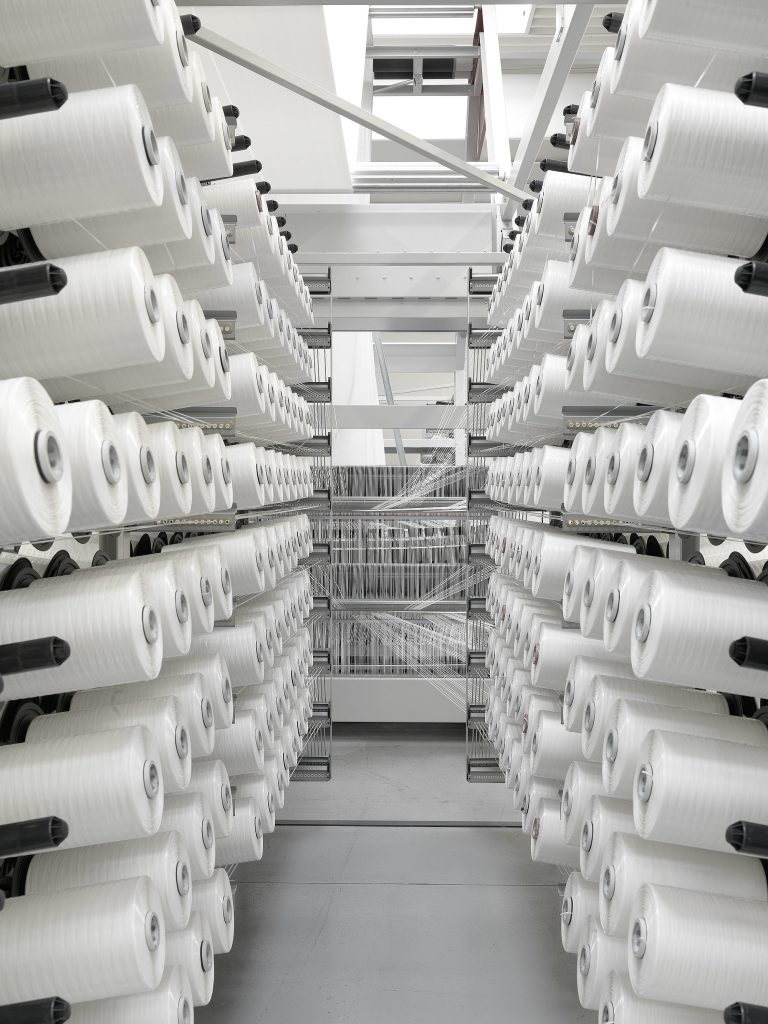
- 1. Innovation in Production: Automation and Material Science
- 2. Branding in a Sustainability-Conscious Market
- 3. Warehousing and Logistics: Precision in Storage
- 4. Industry Leadership: Navigating Regulatory Complexity
- FAQs: Addressing Critical Concerns
- 5. The Road Ahead: Integrating AI and Circular Economies
- Conclusion: Redefining Industrial Packaging
“What will define the next era of woven poly bags in China?”
Ray, CEO of VidePak, answers with unwavering confidence: “It’s the convergence of automation-driven innovation, sustainability-focused branding, and precision engineering. At VidePak, we’re not just manufacturing bags—we’re redefining industrial logistics.”
This vision has propelled VidePak—a global leader with $80M annual revenue and 526 employees—to the forefront of China’s woven poly bag industry. Founded in 2008, the company leverages 30+ years of expertise, Austrian Starlinger machinery, and ISO-certified processes to deliver solutions that balance durability, cost-efficiency, and environmental responsibility. This report explores how technological advancements, strategic branding, and optimized logistics are shaping the future of woven poly bags, with a focus on VidePak’s role as an industry pioneer.
1. Innovation in Production: Automation and Material Science
VidePak’s adoption of cutting-edge technologies ensures its leadership in a competitive market:
A. Starlinger’s Automated Systems
- Circular Looms: 100+ machines operate at 200+ picks per minute (PPM), producing 12×12 strands/inch fabric—20% denser than industry averages.
- 200MT Presses: High-pressure compression reduces bag volume by 30%, maximizing container space utilization during shipping.
Parameter | VidePak Standard | Industry Average |
---|---|---|
Production Speed | 200+ bags/hour | 150–180 bags/hour |
Compression Efficiency | 30% volume reduction | 15–20% |
Moisture Resistance | <1.0 g/m²/24hr (BOPP) | <2.5 g/m²/24hr |
Case Study: A 2024 partnership with a European chemical distributor utilized VidePak’s 200MT-compressed bags, reducing shipping costs by 25% through optimized container loading.
B. Sustainable Material Innovations
- Recycled PP Blends: 30% post-industrial recycled content maintains tensile strength (>30 MPa) while reducing carbon footprint.
- Anti-Static Additives: Carbon-black infusion achieves surface resistivity <10¹² Ω/sq, critical for packaging explosive materials like fertilizers.
2. Branding in a Sustainability-Conscious Market
China’s $45B packaging industry increasingly prioritizes ESG compliance. VidePak’s branding strategy aligns with global trends:
- Certifications: ISO 14001, OEKO-TEX® ECO PASSPORT, and EU REACH compliance.
- Transparency: Blockchain-tracked supply chains (2025 pilot) provide real-time data on material origins and carbon emissions.
Case Study: A 2024 campaign highlighting VidePak’s recyclable FIBC bags boosted B2B client retention by 18% in eco-conscious European markets.
3. Warehousing and Logistics: Precision in Storage
Optimized storage protocols are critical for maintaining product integrity and reducing costs:
A. Climate-Controlled Warehousing
- Temperature: Maintained at 20–25°C to prevent PP degradation.
- Humidity: <50% RH to avoid moisture absorption, which can weaken tensile strength by up to 15%.
B. Stacking and Space Utilization
- AI-Driven Layouts: Algorithms optimize pallet arrangements, increasing storage density by 20%.
- UV-Shielded Packaging: Protects bags in outdoor storage, extending shelf life by 60% under direct sunlight.
4. Industry Leadership: Navigating Regulatory Complexity
VidePak’s compliance with international standards ensures market access:
- EU: EN 13432 (compostability) and REACH (heavy metals <100 ppm).
- US: FDA CFR 21 for food-contact bags; ASTM D5035 for tensile strength.
- Asia: China GB/T 8947 mandates 5:1 safety factors for load-bearing capacity.
VidePak’s 2025 Roadmap:
- Smart Bags: NFC tags for real-time tracking of temperature and humidity during transit.
- Regional Hubs: Southeast Asian factories to cut logistics costs by 25%.
FAQs: Addressing Critical Concerns
Q1: How does compression via 200MT presses affect bag durability?
A: VidePak’s compression maintains seam integrity (80–100 N/cm) while reducing air pockets, enhancing load stability.
Q2: Are recycled PP bags suitable for heavy-duty applications?
A: Yes. VidePak’s 30% recycled blends retain >90% tensile strength, validated by ISO 9001 testing.
Q3: How does climate-controlled storage benefit chemical suppliers?
A: Prevents clumping in hygroscopic materials like disinfectant powders, reducing waste by 12%.
5. The Road Ahead: Integrating AI and Circular Economies
The woven poly bag market is projected to grow at 6.5% CAGR through 2030. VidePak’s innovations include:
- AI-Driven Defect Detection: Reduces production waste by 15% through real-time quality monitoring.
- Closed-Loop Recycling: Partnering with waste management firms to reclaim 50% of post-consumer PP by 2026.
Conclusion: Redefining Industrial Packaging
The future of woven poly bags lies in balancing automation, sustainability, and strategic branding. VidePak’s integration of Starlinger technology, ESG-aligned practices, and logistics optimization positions it as a leader in China’s packaging revolution. As Ray concludes: “In an era where efficiency meets responsibility, our bags don’t just carry goods—they carry the promise of a smarter tomorrow.”
For industries seeking high-performance, certified solutions, VidePak remains the benchmark.
Note: All data reflects 2025 industry benchmarks and VidePak’s internal testing protocols.