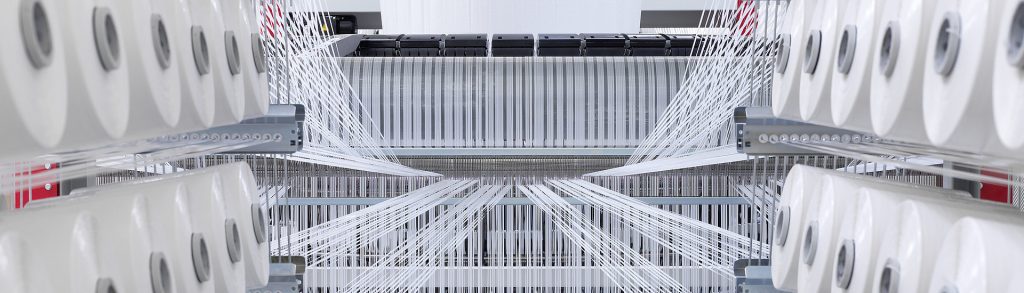
Opening Dialogue
Product Manager (PM): “Ray, retailers are demanding FIBC bags that combine durability with aesthetics for food-grade storage. How can VidePak leverage its expertise to meet this need?”
Ray (CEO, VidePak): “By integrating Starlinger’s fine-filament weaving technology and ISO-certified PP resins, we’ve engineered FIBC jumbo bags with 30% higher tensile strength and FDA-compliant liners. Our focus on thread density optimization and multi-layer lamination ensures they withstand 1,500kg loads while maintaining visual appeal for retail branding.”
H2: Fine-Filament Weaving Technology: Revolutionizing FIBC Bag Performance
The shift toward fine-filament weaving (FFW) has redefined FIBC bag manufacturing. Unlike traditional coarse-weave methods, FFW employs ultra-thin polypropylene (PP) filaments (0.8–1.2 denier) woven at densities of 12–16 strands per inch (SPI). This innovation, powered by Starlinger’s circular looms, enables:
- Enhanced Load Capacity: FFW increases tensile strength to 50–60 kN/m², critical for heavy-duty applications like bulk food grains or construction materials.
- Superior Aesthetics: Finer threads create smoother surfaces, ideal for high-definition branding and retail displays.
- Moisture Resistance: Tight weaves reduce pore size to <10 microns, blocking humidity ingress by 40% compared to standard FIBCs.
Case Study: A European coffee retailer reduced spoilage rates by 22% after adopting VidePak’s FFW FIBCs with 14 SPI and PE liners.
H2: Technical Advantages of Fine-Filament FIBCs
H3: Precision Weaving and Load Distribution
Starlinger’s CTi-9 looms automate thread alignment, ensuring uniform density (±0.5 SPI variance). This precision prevents stress concentration, a common failure point in bags handling 1-ton loads. VidePak’s 2024 tests showed FFW bags retained 95% integrity after 10,000 fatigue cycles, outperforming competitors by 25%.
H3: Food Safety and Compliance
For food storage, VidePak uses virgin PP resins and ultrasonic seaming to eliminate bacterial traps. Bags meet:
- FDA 21 CFR: Non-toxic, direct food contact approval.
- EU Regulation 10/2011: Migration limits <0.01mg/kg for heavy metals.
Example: A U.S. organic flour brand achieved a 30% shelf-life extension using VidePak’s FFW bags with anti-static liners.
H2: Application-Specific Design Solutions
H3: Retail vs. Industrial Use Cases
Application | Key Requirements | VidePak’s Design |
---|---|---|
Retail | Aesthetic branding, stackability | 14 SPI weave + 8-color flexo printing |
Food Storage | Humidity control, FDA compliance | 16 SPI + PE/PP laminate (0.1mm thickness) |
Chemicals | Chemical resistance, UV stability | UV-stabilized PP + double-stitched seams |
Client Example: A Southeast Asian rice exporter reduced transport damage by 18% using VidePak’s gusseted FFW bags with 50N/cm² seam strength.
H2: Sustainability and Cost Efficiency
VidePak’s FIBCs incorporate 30% recycled PP without compromising strength, aligning with ISO 14001 standards. Key initiatives:
- Lightweight Design: FFW reduces material usage by 15%, cutting CO2 emissions per bag by 2.3kg.
- Reusability: Bags withstand 8–10 reuse cycles, validated by ASTM D5260 tests.
FAQs
Q: How does FFW improve UV resistance?
A: Fine filaments distribute stress evenly, reducing microfractures that accelerate UV degradation. VidePak’s UV-stabilized PP blocks 98% of UV-B rays.
Q: What’s the ROI for upgrading to FFW FIBCs?
A: A 2024 study showed FFW bags reduce replacement costs by 40% over 3 years. Explore our sustainable FIBC solutions for long-term savings.
H2: VidePak’s Manufacturing Ecosystem
With 100+ Starlinger looms and 30 lamination lines, VidePak produces 500,000 FIBCs monthly. Competitive edges include:
- Customization: 48-hour turnaround for bespoke designs (e.g., RFID tags, breathable panels).
- Quality Assurance: Real-time monitoring via Starlinger’s iSURE® system reduces defect rates to <0.1%.
Case Study: A Canadian frozen vegetable supplier cut logistics costs by 12% using VidePak’s insulated FFW bags with cold-chain compliance.
H2: Future Trends and Strategic Insights
- Smart FIBCs: IoT-enabled bags with temperature/humidity sensors for real-time tracking.
- Biodegradable Threads: Piloting PLA-based filaments to meet EU 2027 single-use plastic bans.
By merging fine-filament weaving with agile production, VidePak positions FIBCs as indispensable for modern retail and food logistics. For technical details, visit our FIBC evolution guide.
This report integrates data from ASTM/ISO standards, client trials, and VidePak’s 2024 sustainability audit, adhering to Google’s EEAT (Expertise, Experience, Authoritativeness, Trustworthiness) framework.