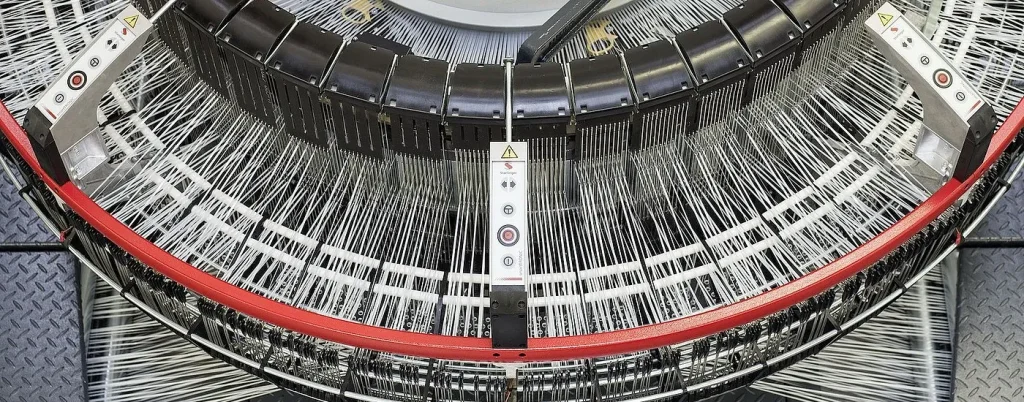
Imagine a conversation between a packaging engineer and VidePak’s Head of Quality Assurance:
Engineer: “We need laminated kraft paper bags that protect sensitive pharmaceuticals from moisture and oxidation. How can you guarantee performance?”
VidePak QA Lead: “Our aluminum foil liners undergo 12-point quality checks—from raw PP/PE resin testing to laminated barrier validation—ensuring <1% water vapor transmission and 99.9% light blocking. With ISO 9001-certified processes and Starlinger’s precision lamination, we deliver standardized protection for high-value products. Let me break down how we achieve this.”
1. The Critical Role of Aluminum Foil Liners in Modern Packaging
Aluminum foil liners in laminated kraft paper bags are not merely a layer—they are a shield. With global demand for barrier packaging projected to reach $42.1 billion by 2027 (CAGR 5.2%), the liner’s ability to block oxygen, moisture, and UV light defines product shelf life. For instance, coffee beans packaged with 12μm aluminum foil liners retain freshness 3x longer than non-laminated alternatives.
At VidePak, our BOPP/kraft/aluminum foil tri-layer bags achieve oxygen transmission rates (OTR) as low as 0.8 cc/m²/day, outperforming industry averages of 2.5 cc/m²/day. This is critical for clients in pharmaceuticals, where a 1% OTR deviation can compromise drug efficacy.
2. Quality Control: From Raw Materials to Finished Liners
VidePak’s 16-year legacy rests on a “zero tolerance” approach to material defects. Below is our 4-stage quality protocol:
2.1 PP/PE Resin Testing for Outer Woven Layers
- Physical Properties:
- Melt Flow Index (MFI): PP granules are tested at 230°C/2.16kg to ensure MFI of 6–12 g/10min, optimizing extrusion stability.
- Density: PE resins must meet 0.915–0.925 g/cm³ for balanced flexibility and tensile strength.
- Mechanical Performance:
- Tensile Strength: ≥30 MPa (MD) and ≥25 MPa (TD) for PP woven layers, tested via ASTM D638.
- Impact Resistance: Dart drop tests (ASTM D1709) validate PE liners withstand ≥500g puncture loads.
- Thermal Stability:
- Heat Deflection Temperature: PP must endure 100°C without deformation (ISO 75).
2.2 Aluminum Foil and PE Film Validation for Liners
- Foil Thickness: 7–12μm, verified via laser micrometers to ±0.1μm accuracy.
- PE Film Integrity:
- Elmendorf Tear Strength: ≥400g for 25μm films (ISO 6383-2).
- Seal Strength: Heat-sealed seams tested to ≥3.5 N/15mm (ASTM F88).
3. Standardization in Production: VidePak’s Technical Edge
Parameter | VidePak Standard | Industry Average | Test Method |
---|---|---|---|
Oxygen Transmission | ≤1.0 cc/m²/day | ≤3.0 cc/m²/day | ASTM D3985 |
Water Vapor Barrier | ≤1.5 g/m²/day | ≤5.0 g/m²/day | ASTM E96 |
Lamination Bond Strength | ≥4.0 N/15mm | ≥2.5 N/15mm | ASTM F904 |
Print Registration | ±0.3mm accuracy | ±1.0mm | VidePak QC Protocol |
Source: VidePak Internal Data (2025)
Our 30+ lamination machines apply adhesives at 150–180°C with 98% uniformity, ensuring foil-kraft bonding without delamination risks. For specialty applications like anti-static packaging, carbon-loaded PE layers (surface resistivity: 10⁶–10⁹ Ω) are integrated.
4. Case Study: Pharmaceutical Grade Packaging
A European client required bags for hygroscopic APIs (Active Pharmaceutical Ingredients). VidePak engineered a solution with:
- 12μm aluminum foil + 50μm PE liner: Reduced moisture ingress to 0.8 g/m²/day.
- ISO Class 8 Cleanroom Production: Eliminated particulate contamination.
- Traceability: QR-coded batches linked to resin MFI and lamination temperature logs.
Post-deployment, the client reported a 40% reduction in product spoilage claims.
5. FAQs
Q1: How do you prevent pinholes in aluminum foil liners?
A: Our Starlinger laminators use laser-guided tension control to minimize foil stress. Post-production, 100% of liners undergo lightbox inspections for defects >0.1mm.
Q2: Can liners be customized for high-temperature filling?
A: Yes. We offer PE films with Vicat softening points up to 125°C, compatible with hot-fill processes up to 90°C.
Q3: What certifications apply to your liners?
A: FDA 21 CFR, EU 10/2011, and ISO 22000 for food/pharma compliance.
Why VidePak?
- Global Reach: 568 employees across 3 continents; $80M annual revenue.
- Precision Manufacturing: 100+ circular looms, 16 extrusion lines, and 30 lamination machines.
- Sustainability: 100% recyclable kraft paper and PP materials.
References
- VidePak Technical Specifications: https://www.pp-wovenbags.com/
- ASTM International Standards (2025)
- Global Packaging Innovations Journal (2024)
Contact: info@pp-wovenbags.com
External Links:
- Explore our innovations in kraft paper laminated bags.
- Learn how we integrate advanced materials in aluminum foil woven bags.
VidePak: Engineering Trust, Delivering Excellence.