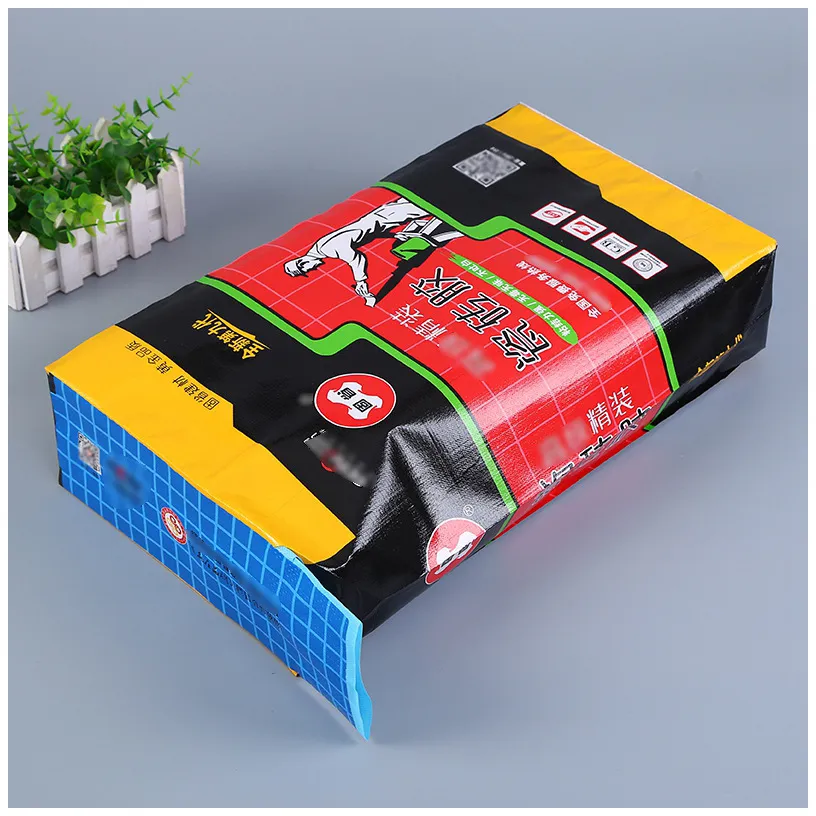
In the packaging industry, particularly for bulk materials such as powders, chemicals, and grains, the use of woven bags has become an essential solution due to their strength, versatility, and cost-effectiveness. Among these, BOPP Valve Woven Bags and BOPP Valve Woven Sacks stand out as a popular choice for a variety of industries. These bags are known for their high durability, efficient use of space, and ability to protect contents from environmental factors. However, what makes these bags even more robust and versatile is the BOPP laminated structure, which enhances their performance in various ways. In this article, we will explore why some BOPP Valve Woven Bags require lamination, the unique characteristics of these bags, and how comprehensive quality control ensures their reliability and safety in packaging.
What are BOPP Laminated Valve Woven Bags?
BOPP (Biaxially Oriented Polypropylene) laminated bags are woven polypropylene bags that are coated with a layer of BOPP film. This film provides several enhancements to the bag’s performance, making it an ideal choice for packaging a wide range of materials, particularly those requiring high levels of protection. BOPP Valve Woven Bags are typically used for packaging dry goods like cement, fertilizers, seeds, and other powdered or granular substances. The valve opening allows easy filling and sealing, ensuring that the contents are securely contained during transportation and storage.
Why Do Some BOPP Valve Woven Bags Require Lamination?
Lamination plays a crucial role in improving the characteristics of Valve PP Bags. Here are some key reasons why lamination is often necessary for certain applications:
- Enhanced Durability and Strength
Lamination strengthens the woven fabric, making it more resistant to wear and tear. The addition of BOPP film reinforces the fabric, providing extra durability during handling and transportation. This makes BOPP Valve Woven Sacks particularly well-suited for heavy-duty applications, where strength is essential. - Protection from Environmental Factors
The lamination layer serves as a protective barrier against moisture, dust, and UV rays. For materials like fertilizers or chemicals that need to remain dry, lamination ensures that the contents are shielded from the elements. Block BOPP Bags, for example, are often used in environments where moisture resistance is critical for maintaining the integrity of the product. - Improved Aesthetic Appeal
The BOPP laminated layer also provides an opportunity for high-quality printing. This allows for branding, labeling, and design options that make the bags more visually appealing. Custom printed BOPP Valve Woven Bags are commonly used in retail packaging where brand recognition and marketing are essential. - Increased Tear Resistance
BOPP Laminated Valve Woven Bags are significantly more resistant to tearing compared to non-laminated bags. This is an important factor in applications where the bags may undergo rough handling, as lamination helps prevent damage that could lead to spillage or contamination. - Chemical Resistance
The lamination layer adds another level of protection against chemicals, which is essential when packaging products like fertilizers or powdered chemicals. The BOPP film acts as a barrier to prevent chemical reactions between the bag material and its contents.
Common Quality Issues with Valve Woven Bags
Like any packaging material, Valve Woven Bags can face quality issues that compromise their performance. In this section, we will explore the most common quality problems associated with these bags and how comprehensive testing ensures that these issues are avoided.
- Thickness Tolerance
One of the most common issues is the inconsistency in the thickness of the material. Bags that are too thin may tear under pressure, while those that are too thick can be unnecessarily heavy and costly. To ensure the right thickness, precise thickness tolerance tests are conducted on BOPP Valve Woven Bags to guarantee that the bags meet industry standards and customer requirements. - Uneven or Ragged Cut Edges
A poorly cut edge can lead to weakness in the bag and increased chances of rupture. It is important for the bag’s edges to be neat and uniform. The cutting process is rigorously checked for precision, and the edges are inspected for any fraying or jaggedness that could weaken the bag’s structural integrity. - Color Discrepancies (Color Matching)
Color consistency is vital, especially for printed BOPP Valve Woven Bags, where branding is a critical part of the packaging. A difference in color from batch to batch can create confusion or a negative perception of the brand. A comprehensive color difference test is conducted to ensure that all batches of bags meet the required color standards, providing uniformity in appearance. - Weight Discrepancy
The weight of a bag is crucial in determining its strength and capacity. Any discrepancy in grammage or weight can lead to issues in packaging and distribution. To ensure this, weight testing is conducted to ensure that each bag meets the required weight specifications. - Stretching and Elongation
For BOPP Valve Woven Sacks, the material needs to have a specific stretching capacity to withstand heavy loads. Bags that lack sufficient elongation may rupture or tear when filled with heavy materials. Tensile strength and elongation tests are crucial to ensure the bag’s ability to stretch without breaking under pressure. - Impact Resistance
Bags that are not resistant to impact may burst or break during handling or transportation. Impact testing is essential to evaluate how well the bags hold up under different types of stress and impact. - UV and Aging Resistance
Exposure to sunlight can weaken woven bags, especially when used outdoors. The UV resistance of Valve Woven Bags is critical, and therefore UV testing is performed to ensure that the bags retain their strength and durability under prolonged exposure to sunlight. Aging tests are also carried out to simulate long-term use and environmental exposure. - Environmental Safety
Sustainability is a growing concern in packaging, and this extends to BOPP Valve Woven Bags. Environmental testing ensures that the bags meet regulatory requirements, including recyclability and non-toxicity. Eco-friendly testing ensures that the materials used in manufacturing the bags meet environmental standards, supporting sustainability efforts.
Comprehensive Testing and Quality Control at VidePak
At VidePak, we understand the importance of maintaining the highest standards for packaging materials. This is why we employ a comprehensive quality control system that includes multiple testing points throughout the manufacturing process. From BOPP laminated valve woven bags to Block BOPP Bags, we ensure that each product meets our rigorous standards before reaching our customers.
Our testing parameters include:
Test | Purpose |
---|---|
Thickness Tolerance | To ensure the bag meets the required thickness specifications. |
Edge Quality and Neatness | To ensure the edges are clean and free from fraying. |
Color Difference | To ensure consistent color matching across batches. |
Weight Consistency | To ensure the bags meet the required weight specifications. |
Tensile Strength and Elongation | To ensure the bags can handle the required load without tearing. |
Impact Resistance | To ensure the bags can withstand impacts during handling. |
UV Resistance | To ensure the bags can withstand UV rays and outdoor use. |
Environmental Testing | To ensure the bags meet eco-friendly and sustainability standards. |
Our attention to detail ensures that every Valve PP Bag we produce is capable of handling the most demanding applications while meeting the diverse needs of our clients. Whether you’re looking for a BOPP Valve Woven Bag with high UV resistance or BOPP Valve Woven Sacks that can handle heavy-duty applications, we guarantee the best quality.
For more information about our products and comprehensive quality management system, check out our articles on BOPP Valve Woven Bags, BOPP Valve Woven Sacks, and Valve PP Bags.
With VidePak’s commitment to quality, we continue to lead the way in the packaging industry, providing durable, reliable, and sustainable solutions for our customers worldwide.