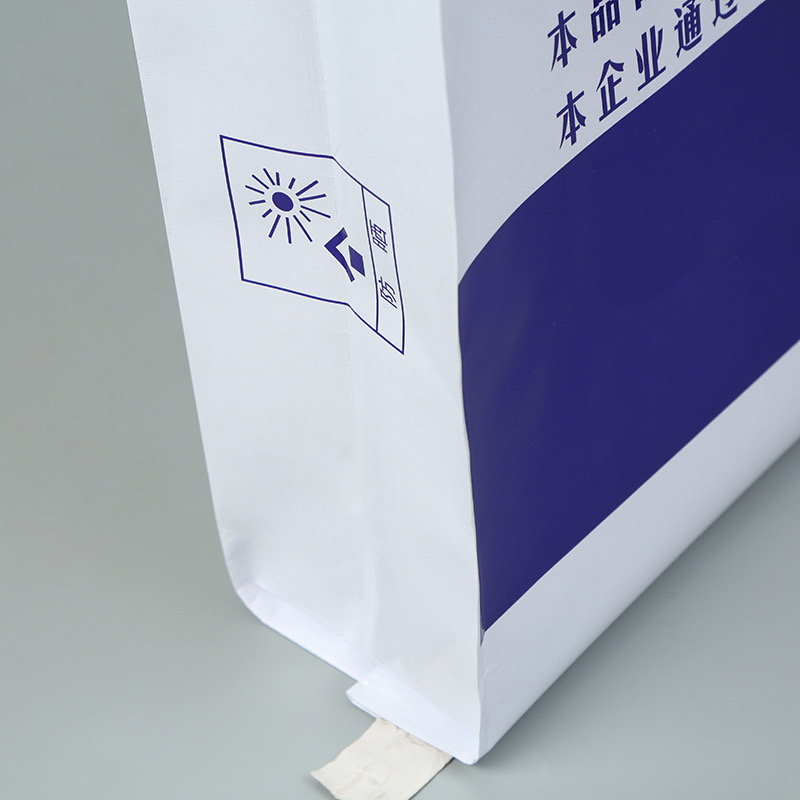
Introduction
The global packaging industry is experiencing rapid evolution, particularly in the area of woven bags. Laminated woven bags and BOPP woven bags have become prominent in various industries due to their durability, customization options, and versatile applications. These bags are made using a multi-layered co-extrusion blown film process, which allows for superior strength, moisture resistance, and print quality, making them ideal for packaging everything from food products to chemicals. In this article, we will explore the intricate manufacturing processes of these bags, the factors influencing bag design, and the selection of appropriate bag-sealing and sewing techniques to optimize performance.
Understanding Laminated Woven Bags and Their Manufacturing Process
Laminated Woven Bags are made by combining woven polypropylene fabric with a layer of Laminated PP bags film, commonly through a process known as multi-layered co-extrusion blown film. This method produces bags that possess a perfect balance of strength, moisture resistance, and visual appeal.
The Multi-Layered Co-Extrusion Blown Film Process
The multi-layered co-extrusion blown film process plays a critical role in ensuring the durability and functionality of Laminated woven sacks. Here’s a breakdown of how the process works:
- Polypropylene Granules: The production starts with high-quality polypropylene (PP) granules. These granules are melted and extruded through a die, forming a thin film.
- Blown Film Extrusion: This molten PP is then blown into a thin film. The co-extrusion technique combines multiple layers of material, typically polypropylene (PP) and biaxially oriented polypropylene (BOPP), each layer serving a specific purpose—strength, clarity, and barrier properties.
- Lamination Process: The film is laminated onto woven fabric, typically polypropylene fabric, which ensures the bag has added strength and resistance. This combination of woven fabric and film layers makes BOPP woven bags ideal for packaging applications requiring high-quality protection and aesthetics.
- Customization: The laminated surface can be printed with custom designs, making Laminated woven bags popular for branding purposes, particularly in industries like food, agriculture, and construction.
This process gives multi-wall woven bags their signature look and feel, enabling them to withstand the rigors of handling, transportation, and exposure to the elements while still offering a high level of product protection.
Choosing the Right Sealing and Sewing Techniques
The production of Laminated Woven Bags goes beyond just the materials. The sealing and sewing techniques used to finish these bags are just as important for their functionality. These processes determine the bag’s strength, durability, and usability.
1. Bottom Seaming: Critical for Durability
The bottom of a woven bag is often subjected to heavy pressure during transport, so the quality of the bottom seam is crucial. Bottom seaming involves folding and sealing the bag’s base using various methods:
- Sewn Bottom: This method involves stitching the fabric together at the bottom, offering strength and durability for heavy-duty applications like bulk material packaging. It’s commonly used in multi-wall woven bags and Laminated woven sacks where robust sealing is required.
- Hot Air Sealing: Often used in bags made of laminated film, this technique involves using hot air to bond the fabric together, ensuring a clean, seamless finish.
2. Heat Sealing: Ensuring Leak Resistance
Heat sealing is one of the most popular methods for closing Laminated Woven Bags, especially when a clean, moisture-resistant seal is needed. The process involves applying heat to both layers of the laminate, causing the polymer to melt and bond the edges of the bag together. The resulting seal is airtight, ensuring that the contents of the bag remain safe from external environmental conditions.
Heat sealing is especially important for BOPP Woven Bags and Laminated PP Bags used for packaging perishable items, as it provides superior moisture protection and leak resistance. Heat sealing also allows for smooth, uniform bag edges that contribute to both the aesthetics and functionality of the product.
3. Ultrasonic Welding: A Modern Innovation
Another cutting-edge sealing technique is ultrasonic welding. This method uses high-frequency ultrasonic sound waves to create an instant bond between the layers of material. It is ideal for applications requiring extremely strong and precise seams, particularly in Laminated woven sacks for sensitive products like food and pharmaceuticals.
Ultrasonic welding is particularly effective for BOPP Woven Bags, as it allows for cleaner, stronger seals without the need for additional adhesives or mechanical fasteners. It’s a faster, more efficient way to ensure high-quality seams while preserving the integrity of the laminated surface.
4. Sewing Material and Stitch Density
The type of sewing material and the density of stitches can significantly impact the strength and quality of the bag. For industrial applications, a stronger thread is needed to ensure the bag can carry heavy loads. Polyester thread is commonly used for Laminated Woven Bags due to its high tensile strength, resistance to abrasion, and low moisture absorption. Additionally, the stitch density—the number of stitches per inch—must be considered to balance flexibility and strength. Higher stitch densities provide stronger seams, ideal for heavy-duty multi-wall woven bags.
5. Various Bag Mouth Designs: Open, Valve, and More
The design of the bag’s opening also plays a critical role in functionality. Different bag mouth designs are employed depending on the contents and intended use:
- Open Mouth: This design is the most common for Laminated Woven Bags and is ideal for loose products. It allows for easy filling but requires a separate closure (such as a drawstring or heat seal) to secure the contents.
- Valve Mouth: A valve mouth is an innovative feature commonly seen in BOPP Woven Bags. It consists of a built-in valve that automatically closes when filled, providing better control over the bag’s sealing process. This is often used for fine powders or granular materials, like cement or animal feed.
- Heat-Sealed Mouth: For products that require more airtight packaging, heat-sealed mouth designs offer a strong, moisture-resistant closure. This is especially important for sensitive products like food and pharmaceuticals.
Key Parameters of Laminated Woven Bags
The performance of Laminated woven bags depends on several critical factors that should be considered before selection. These include:
Parameter | Description | Impact on Bag Performance |
---|---|---|
Material Type | Polypropylene or BOPP Laminated film | Affects strength, durability, and moisture resistance |
Sealing Method | Heat Sealing, Ultrasonic Welding, Sewing | Determines air-tightness, strength, and security |
Bag Design | Open Mouth, Valve, or Heat Sealed | Determines ease of filling and closure |
Stitch Density | High or Low Stitch Density | Affects strength and load capacity |
Print Quality | High-quality graphics printing on the surface | Enhances branding and visibility |
FAQs on Laminated Woven Bags
- What are the main applications for laminated woven bags?
- Laminated woven bags are ideal for packaging bulk materials such as grains, cement, fertilizers, chemicals, and food products. Their durability, resistance to moisture, and excellent printing capability make them versatile across industries.
- Can laminated woven bags be customized?
- Yes, they can be customized in terms of size, shape, color, printing, and bag mouth design. This makes them a great choice for brands seeking to differentiate their products.
- What is the difference between a BOPP woven bag and a laminated woven bag?
- BOPP woven bags are a specific type of Laminated woven bags, where the film layer is made from biaxially oriented polypropylene. This provides added strength and clarity, especially useful in products that require high durability and high-quality printing.
- How do I choose the right sealing method for my woven bag?
- The choice depends on the type of product being packaged and the required sealing strength. Heat sealing works well for moisture-sensitive products, while ultrasonic welding may be preferred for bags that need high strength and clean, precise seams.
Conclusion
The production of Laminated Woven Bags involves complex techniques that merge advanced materials and processes, including the multi-layered co-extrusion blown film process. The selection of appropriate bag-sealing and sewing methods is critical for ensuring the durability, functionality, and quality of these bags. By understanding the various sealing techniques, such as heat sealing, ultrasonic welding, and sewing methods, manufacturers can optimize the performance of BOPP Woven Bags and Laminated woven sacks for a wide range of applications. With continued innovations, these bags will remain a popular choice in global packaging markets.
For further insights on Laminated Woven Bags, explore this link and this link.