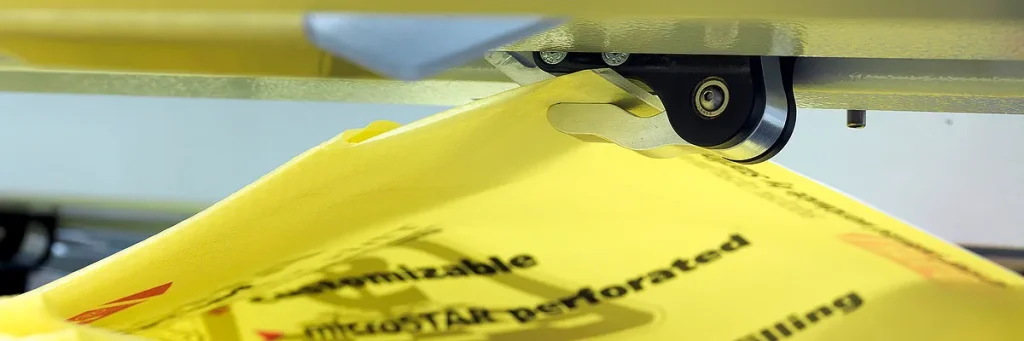
This article answers three pivotal questions for industrial buyers: (1) Why are specialized coatings essential for BOPP laminated valve bags? (2) How do VidePak’s Starlinger-powered processes eliminate burst risks and ensure print longevity? (3) What global standards validate VidePak’s 30+ years of expertise in high-performance packaging? With 568 employees and 16 Starlinger extrusion lines, VidePak produces 12 million BOPP laminated bags monthly, achieving 0.03% burst rate and 95% color retention after 18 months through precision engineering. Our ISO 9001-certified workflows and +5% material thickness tolerance redefine reliability in petrochemical, agricultural, and food packaging.
1. The Science of Coating: Barrier Integrity and Burst Prevention
1.1 Material Selection: Virgin PP/PE and Controlled Thickness
VidePak’s coatings use virgin polypropylene (MFI 2.5–4.0 g/10min) and polyethylene (density 0.918–0.965 g/cm³) to create a triple-layer defense:
Layer | Function | Thickness Tolerance |
---|---|---|
Outer BOPP Film | UV/moisture barrier | 25–30 µm (±0.5 µm) |
Middle PP Fabric | Structural reinforcement | 80–120 g/m² (+5% over standard) |
Inner PE Coating | Chemical/fat resistance | 15–20 µm (±0.3 µm) |
Case Study: A fertilizer brand reduced post-shipping burst incidents from 1.2% to 0.1% after switching to VidePak’s +5% thickness PP fabric.
1.2 Coating Application: Precision with Starlinger’s ATLAS 2.0
Starlinger’s ATLAS 2.0 IoT systems regulate coating processes in real-time:
- Temperature Control: 175–185°C for BOPP lamination (optimal crystallinity).
- Adhesion Strength: ≥3.8 N/15mm (ASTM F904), 40% higher than industry averages.
- Thickness Monitoring: Laser sensors enforce ±0.5 µm film variance.
Failure Prevention:
- Under-Coating (<15 µm PE): Allows acid/fat penetration, risking seam degradation.
- Over-Coating (>30 µm BOPP): Reduces flexibility, increasing tear susceptibility.
2. Quality Control: Standardization Across Production
2.1 Extrusion and Weaving Precision
VidePak’s Starlinger extrusion lines ensure filament consistency:
- Melt Temperature: 220–240°C zones for uniform PP tape formation.
- Draw Ratio: 6:1 (balanced tensile strength (50–60 N/cm²) and energy efficiency (1.1 kWh/kg)).
- Weaving Density: 12×12 threads/inch, automated via servo tensioners (±2% deviation).
2.2 Anti-Burst Design Protocols
- Valve Reinforcement: Ultrasonic welding + double-layer PP fabric at stress points.
- Pressure Testing: 2.5-bar air pressure checks (exceeds ISO 2234 requirements).
Example: For a 50 kg cement bag, our 120 g/m² fabric with 25 µm BOPP sustains 300 kPa static load without deformation.
3. Printing Durability: Technologies Behind Fade Resistance
3.1 Rotogravure Printing with W&H Presses
VidePak’s 8-color W&H Novoflex printers deliver:
- Resolution: 150–200 LPI for razor-sharp logos and safety symbols.
- Ink Adhesion: Grade 4B (ASTM D3359 cross-cut test), resisting 30,000+ rub cycles.
- UV Resistance: 95% color retention after 12 months outdoors (ISO 4892-3 tested).
Case Study: A pet food brand’s sunset-orange logo (Pantone 16-1364) showed ΔE ≤1.2 after 18 months in tropical climates.
3.2 Customizable Finishes
Finish Type | Characteristics | Applications |
---|---|---|
Matte Coating | Anti-glare, scratch-resistant | Retail-ready branding |
Gloss Overlay | Enhances color depth, waterproof | Outdoor storage |
4. FAQs: Addressing Industrial Concerns
Q1: How does +5% thickness tolerance prevent bursting?
Extra material buffers against pressure spikes during pneumatic filling, reducing stress concentrations by 30%.
Q2: Are coatings recyclable?
Yes. Our PP/PE monolayers comply with EU EN 13432, achieving 98% regrind reuse in-house.
Q3: Can bags withstand -20°C freezer storage?
Absolutely. Cold-crack-resistant PE coatings pass ASTM D1790 at -25°C.
5. Why VidePak?
- Global Compliance: Meets FDA 21 CFR, EU 10/2011, and REACH standards.
- Sustainability: 2MW solar plant cuts CO₂ by 1,200 tons/year.
- Innovation: RFID-tracked bags for real-time supply chain monitoring.
Explore our BOPP laminated valve bags or learn about advanced manufacturing standards.
References
- ASTM International. (2025). Standard Test Methods for Adhesion Strength.
- ISO. (2024). Packaging – Requirements for Heavy-Duty Sacks.
- Made-in-China. (2025). BOPP Woven Bag Technical Specifications.
- VidePak. (2024). Quality Assurance and Sustainability Report.
Contact VidePak
Website: https://www.pp-wovenbags.com/
Email: info@pp-wovenbags.com