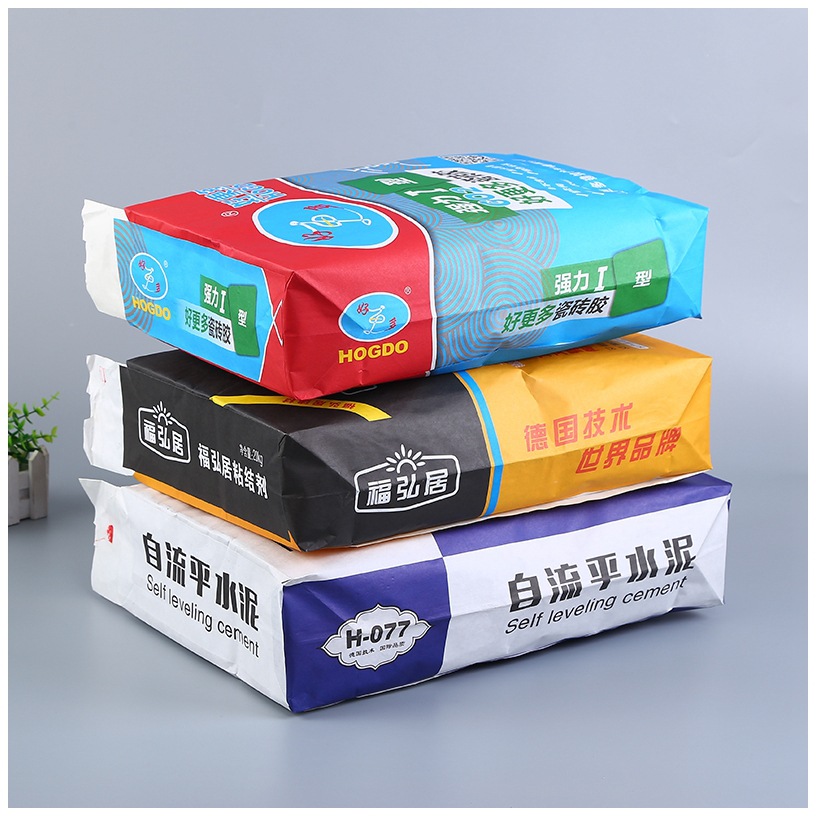
- Key Features of Printed BOPP Woven Bags
- Printed BOPP Woven Sacks in Industry Applications
- Commonly Used Additives
- Fillers in Woven Bags
- 1. What makes Printed BOPP Woven Bags eco-friendly?
- 2. How can I ensure durability for outdoor storage?
- 3. Are there specific fillers to avoid for food-grade bags?
- 4. Can Printed BOPP Woven Sacks be used for liquids?
- 5. What is the lead time for wholesale orders?
When it comes to Printed BOPP Woven Bags, the packaging industry finds itself at the intersection of aesthetics, durability, and versatility. These bags are recognized for their excellent print quality, strength, and adaptability, making them a staple for industries ranging from agriculture to retail. Additionally, choosing the right materials and additives, such as polypropylene (PP) or polyethylene (PE), alongside stabilizers like UV inhibitors and antioxidants, is essential in optimizing bag performance.
Key Features of Printed BOPP Woven Bags
Printed BOPP Woven Bags excel in packaging due to their unique blend of properties:
Features | Advantages |
---|---|
High-quality printing | Vibrant, detailed designs for branding and product identification. |
Durability | Strong woven structure resists tearing and punctures. |
Weather resistance | Excellent resistance to moisture, UV rays, and chemicals when laminated. |
Eco-friendly options | Recyclable materials and sustainable production processes align with global environmental standards. |
With these features, Printed BOPP Woven Bags cater to sectors like agriculture, construction, and retail, providing tailored solutions for packaging needs.
Printed BOPP Woven Sacks in Industry Applications
The versatility of Printed BOPP Woven Sacks is unmatched. They are widely used for:
- Agricultural Products: Packaging grains, seeds, and fertilizers.
- Construction Materials: Cement, sand, and other heavy materials.
- Food Products: Flour, sugar, and animal feed.
Their adaptability to diverse product types while offering enhanced visual appeal makes them a preferred choice in competitive markets.
Material Properties: Polypropylene (PP) vs. Polyethylene (PE)
The choice of base material significantly impacts the performance of woven bags. Below is a comparison of PP and PE properties:
Property | Polypropylene (PP) | Polyethylene (PE) |
---|---|---|
Strength | High tensile strength, ideal for heavy-duty bags. | Moderate strength, better for lighter loads. |
Moisture resistance | Superior, especially when laminated. | Good but slightly less effective than PP. |
Temperature tolerance | Handles higher temperatures effectively. | More flexible at lower temperatures. |
Weight | Lightweight with excellent stiffness. | Heavier but softer texture. |
Cost | Slightly higher but delivers better overall value. | More economical for certain uses. |
For Printed PP Bags, the superior strength, lightweight structure, and durability of PP make it the favored choice, especially in industries requiring robust packaging.
Additives and Fillers: Enhancing Bag Performance
To further enhance the durability and functionality of Printed PP Woven Bags, various additives and fillers are incorporated during manufacturing.
Commonly Used Additives
Additive | Function |
---|---|
UV stabilizers | Protect bags from degradation caused by prolonged sun exposure, extending their outdoor lifespan. |
Antioxidants | Prevent material degradation during high-temperature processing. |
Anti-slip agents | Improve bag stacking efficiency by increasing surface friction. |
Color pigments | Provide vibrant, customizable designs for branding purposes. |
Fillers in Woven Bags
Fillers, such as calcium carbonate, can be added to reduce production costs and improve bag stiffness. However, excessive use of fillers may compromise bag strength and flexibility, requiring a balance tailored to specific applications.
Customization for Printed Woven Bags Wholesale
For buyers seeking Printed woven bags wholesale, customization plays a critical role in meeting market demands. Custom options include:
- Sizes and shapes: From small retail bags to large industrial sacks.
- Printing designs: Up to 10-color high-resolution graphics for branding and marketing.
- Lamination types: Glossy or matte finishes for aesthetic and functional needs.
Bulk orders of Printed BOPP Woven Bags can also benefit from economies of scale, reducing per-unit costs while maintaining high-quality standards.
FAQs About Printed PP Woven Bags
1. What makes Printed BOPP Woven Bags eco-friendly?
These bags are recyclable and can incorporate sustainable materials, such as bio-based polypropylene. Production processes are designed to minimize waste, and bags can often be reused multiple times.
2. How can I ensure durability for outdoor storage?
Incorporating UV stabilizers during manufacturing will protect bags from sun exposure, while lamination can provide additional weather resistance.
3. Are there specific fillers to avoid for food-grade bags?
Yes, food-grade bags should avoid non-food-safe fillers and additives. Always verify compliance with industry standards and certifications.
4. Can Printed BOPP Woven Sacks be used for liquids?
While they are not inherently liquid-proof, an additional PE liner can be added to improve moisture and liquid containment.
5. What is the lead time for wholesale orders?
Lead times typically depend on order size and customization requirements, ranging from 2-6 weeks.
External References and Resources
For more insights into Printed BOPP Woven Bags, visit the following resources:
- Learn about advanced production techniques for Printed BOPP Woven Bags: VidePak’s Expertise.
- Explore the use of high-grade PP pellets in Printed PP Bags manufacturing: Quality Standards.
These articles delve deeper into the technologies and innovations that define the industry, offering valuable knowledge for both buyers and manufacturers.
By understanding the features of Printed BOPP Woven Bags, the material selection process, and the role of additives, businesses can make informed choices that align with their operational and sustainability goals. Whether for agriculture, construction, or retail, these bags offer unmatched versatility, strength, and branding potential.