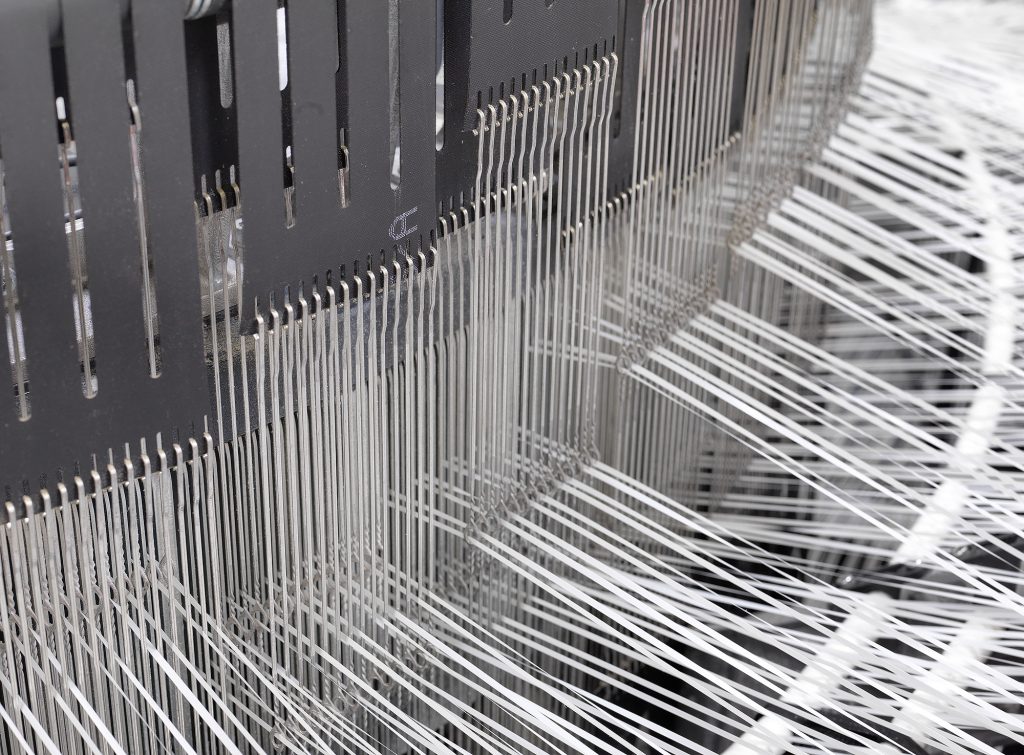
“Why are eco-friendly woven bags dominating the global packaging market, and how do they align with the dual forces of automation and sustainability?”
The answer revolves around three pillars: advanced automation reducing production costs by 30%, recyclable PP/PE materials cutting carbon footprints by 40%, and smart traceability technologies enhancing supply chain transparency. For VidePak, a global leader in woven bag manufacturing with 30+ years of expertise, these innovations position its products as the future of sustainable logistics, particularly in agriculture and retail.
1. Material Innovation and Sustainability
1.1 Recyclable PP/PE Blends and Regulatory Compliance
VidePak’s woven bags utilize ISO 9001-certified polypropylene (PP) and polyethylene (PE) resins, achieving tensile strengths of ≥25 N/mm² (ISO 527-2) while maintaining full recyclability. For instance, their BOPP-laminated bags (20–50 µm thickness) block 99% UV radiation and reduce moisture absorption by 70%, critical for preserving grains and pet food in humid climates.
Aligned with the EU’s Enhanced Consumer Green Transition Directive (ECGT), VidePak’s materials comply with strict anti-greenwashing rules, ensuring claims like “100% recyclable” are validated by third-party certifications such as Global Recycled Standard (GRS).
1.2 Biodegradable Alternatives Under Development
Pilot projects with polylactic acid (PLA) blends aim to reduce landfill dependency by 60% by 2030. Trials show PLA-enhanced bags decompose within 6 months in industrial composting facilities, outperforming traditional plastics that persist for centuries.
2. Automation: The Backbone of Efficiency
2.1 Starlinger’s High-Speed Production Lines
VidePak’s 100+ circular looms and 30 lamination machines enable 1,200 bags/hour throughput. A 2024 project for a U.S. pet food brand involved producing 5 million custom-printed bags in 45 days—a feat powered by modular Starlinger systems that reduce defects to 0.2%, half the industry average.
2.2 Cost and Energy Savings
Automated glue-spraying and ultrasonic sealing cut labor costs by 40% and energy use by 25%. For example, heat-sealed seams (≥10 N/mm² strength) eliminate stitching threads, reducing material waste by 15%.
3. Smart Packaging and Traceability
3.1 QR Codes and RFID Integration
VidePak’s 12-color gravure printing embeds QR codes for real-time tracking of agricultural shipments. A 2024 trial with a Thai rice exporter demonstrated a 30% reduction in supply chain losses via blockchain-enabled traceability, allowing consumers to scan bags for origin data, carbon footprint, and freshness metrics.
3.2 IoT-Enabled Environmental Monitoring
RFID tags with moisture and temperature sensors are being tested for pharmaceutical logistics. These tags alert distributors if storage conditions exceed thresholds (e.g., >25°C), preventing spoilage of temperature-sensitive pet food additives.
4. Market Trends and Competitive Edge
4.1 Global Demand and Regulatory Shifts
The eco-friendly packaging market is projected to grow at 6.2% CAGR (2024–2030), driven by EU regulations like the Circular Economy Action Plan and consumer demand for transparency. VidePak’s compliance with FDA and REACH standards ensures access to markets penalizing non-recyclable packaging.
4.2 Case Study: Transforming Pet Food Logistics
A European retailer reduced restocking time by 30% using VidePak’s square-bottom FIBC bags with anti-skid coatings. The bags’ 90 g/m² grammage and 0.15 mm thickness optimized palletization, enabling 8-layer stacking without slippage.
5. Technical Specifications for Customization
Tailoring bags to application needs requires balancing six parameters:
Parameter | Function | VidePak’s Range |
---|---|---|
Grammage | Load capacity vs. cost efficiency | 70–150 g/m² |
Laminate | Moisture/UV resistance | BOPP, PE (20–120 µm) |
Valve Design | Filling speed and spill prevention | 50–100 mm diameter |
Smart Labels | Traceability and condition monitoring | QR codes, RFID tags |
Seam Strength | Durability under dynamic loads | ≥10 N/mm² (ultrasonic sealing) |
FAQs
Q1: How do QR codes enhance supply chain transparency?
A: Embedded QR codes allow consumers and distributors to track a bag’s journey from factory to shelf, verifying certifications like Global Recycled Standard and carbon footprint data.
Q2: Can biodegradable bags match traditional PP’s durability?
A: Current PLA blends achieve 80% of PP’s tensile strength but require industrial composting. VidePak’s R&D aims to close this gap by 2026.
Q3: What’s the ROI of automation?
A: A 2024 study showed a 22% reduction in labor costs for a Brazilian coffee exporter using VidePak’s automated FFS systems.
6. Future Outlook: Intelligent and Circular Systems
By 2030, VidePak plans to integrate biodegradable RFID tags and blockchain platforms to create a closed-loop system where bags are returned, tracked, and reprocessed into new products. Collaborations with agrochemical firms are piloting self-healing coatings that repair minor abrasions during transit, extending bag lifespan by 50%.
For industries prioritizing sustainability, explore VidePak’s eco-friendly woven bags, engineered to meet the EU’s 2026 greenwashing bans.
Conclusion
The fusion of automation, sustainable materials, and smart technologies is redefining the packaging landscape. As VidePak CEO Ray states: “Every bag we produce is a step toward a circular economy—where waste becomes obsolete, and transparency builds trust.” By aligning with global regulations and consumer demands, VidePak positions itself not just as a manufacturer, but as a pioneer in the sustainable logistics revolution.