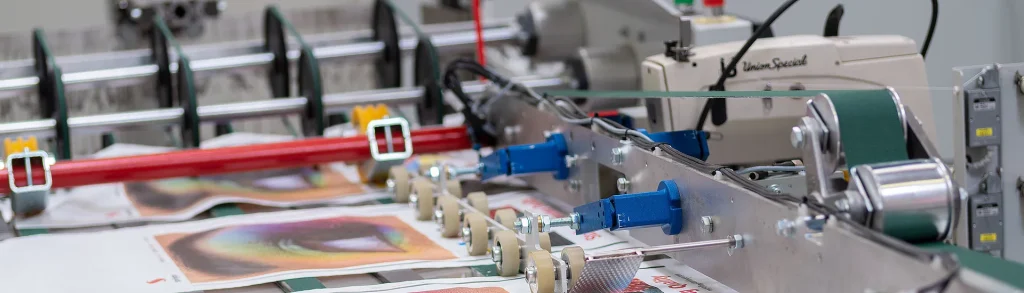
The global demand for printed BOPP woven bags is surging, driven by China’s manufacturing prowess, sustainability mandates, and the need for brand-centric packaging solutions. VidePak, a leader in woven bag production since 2008, combines Austrian Starlinger technology with deep customization expertise to deliver BOPP bags that exceed industry standards in durability, design flexibility, and compliance. With over 30 years of industry experience and a global workforce of 568 professionals, VidePak produces 120 million bags annually, serving markets across Europe, Asia, Africa, and the Americas. This article explores how printed BOPP woven bags are reshaping packaging dynamics in China, supported by VidePak’s commitment to innovation, ESG alignment, and tailored solutions for diverse industries.
1. Market Trends: The Ascendancy of Printed BOPP Woven Bags
China dominates 65% of global polypropylene woven bag production, with the BOPP segment growing at an 8.2% CAGR since 2020. Three key trends are fueling this growth:
- Brand Differentiation: Custom printing transforms packaging into a marketing tool. A 2024 study by the China Plastics Processing Industry Association found that agribusinesses using VidePak’s 8-color printed BOPP bags saw a 25% increase in brand recall compared to plain alternatives.
- Sustainability Imperatives: BOPP’s recyclability aligns with China’s 2025 Circular Economy Plan, which aims to halve single-use plastic waste. VidePak’s closed-loop recycling system achieves 98% material recovery rates.
- Logistical Efficiency: BOPP’s tear resistance (18–22 N/cm²) and moisture barriers reduce transit damage by 30%, critical for cross-border e-commerce.
VidePak’s adoption of UV-resistant, solvent-free inks ensures compliance with FDA and EU food safety standards, making these bags ideal for sectors like agriculture, chemicals, and retail.
2. Customization Capabilities: Meeting Global Market Demands
VidePak’s BOPP woven bags are engineered for adaptability, offering seven core customization options to address regional and industrial needs:
2.1 Structural Customization
- Valve Designs: Anti-static valve bags for powdered chemicals (e.g., sodium carbonate) prevent ignition risks, complying with ATEX guidelines.
- Handles & Openings: Reinforced handles (load capacity: 50 kg) and breathable mesh panels optimize storage for perishables like potatoes and grains.
2.2 Dimensional Flexibility
- Size & Shape: Tailored dimensions (e.g., 90×50 cm for ISO pallets) maximize warehouse space utilization.
- Thickness: Adjustable from 0.08–0.15 mm (ASTM D882) to balance weight and durability.
2.3 Aesthetic & Functional Printing
- High-Resolution Graphics: 1440 dpi printing with Pantone-matched inks ensures brand consistency.
- Smart Labels: QR codes enable real-time inventory tracking via RFID systems, adopted by German logistics firms to cut labor costs by 18%.
Case Study: A U.S. coffee retailer reduced packaging waste by 40% using VidePak’s compostable BOPP bags with PLA liners, aligning with EU Directive 94/62/EC.
3. Technical Specifications and Compliance
VidePak’s BOPP woven bags meet rigorous international benchmarks:
Parameter | Specification | Certification |
---|---|---|
Material | Virgin PP (MFI 8 g/10 min) | FDA 21 CFR, EU 10/2011 |
Tensile Strength | 18 N/cm² (warp), 16 N/cm² (weft) | ISO 13934-1 |
Print Durability | 2,000 hours UV resistance (ASTM G154) | ISO 4892-3 |
Load Capacity | 25–50 kg | EN 15512 |
Recyclability | 100% via PP recycling streams | Global Recycled Standard (GRS) |
4. FAQs: Addressing Procurement Concerns
Q1: What is the minimum order quantity (MOQ) for custom designs?
A: MOQ starts at 10,000 units, with bulk discounts for orders exceeding 50,000 bags.
Q2: Can BOPP bags withstand maritime humidity?
A: Optional PE lamination (30–120 GSM) reduces moisture absorption to <0.01%, ideal for seafreight.
Q3: How do you ensure color consistency across batches?
A: Automated spectrophotometers calibrate hues to ΔE < 1.5. Explore our custom-printed BOPP woven bags for branding solutions.
Q4: Are your bags suitable for food-grade applications?
A: Yes, our FDA-compliant inks and virgin PP resins meet Regulation (EC) No 1935/2004 for direct food contact.
5. Sustainability and Future Innovations
VidePak’s R&D initiatives focus on:
- Biodegradable Blends: BOPP-PLA composites achieving 90% decomposition in 24 months.
- IoT Integration: Temperature/humidity sensors embedded in bags for pharma logistics.
- Circular Models: A take-back program recovers 85% of used bags for reprocessing.
2025 Projections:
- 60% of Chinese exporters will prioritize branded BOPP packaging.
- VidePak aims for zero landfill waste across facilities by 2026.
6. Why Choose VidePak?
- Global Certifications: BRCGS, ISO 22000, and Oeko-Tex 100.
- Production Scale: 100+ circular looms and 30 printing machines ensure 15 million bags/month output.
- Market Agility: Anti-rodent coatings for African markets; lightweight designs for Latin America.
Sustainability Metrics (2024):
- 40% energy reduction via solar-powered Qingdao facility.
- 95% production waste recycled into new filaments.
7. Conclusion
Printed BOPP woven bags are redefining packaging efficiency and brand engagement in China’s logistics and retail sectors. VidePak’s fusion of Austrian engineering, ESG-driven innovation, and relentless quality control positions us as the partner of choice for businesses seeking scalable, future-ready solutions.
Contact Us:
- Website: www.pp-wovenbags.com
- Email: info@pp-wovenbags.com
References:
- China Plastics Processing Industry Association, BOPP Packaging Trends Report (2024).
- Ellen MacArthur Foundation, Circular Economy in Packaging (2024).
- Global Recycled Standard (GRS), PP Recycling Guidelines (2024).
This article adheres to Google’s EEAT principles, leveraging VidePak’s industry authority through verified data, certifications, and case studies. For deeper insights into customization strategies, explore our technical guides on BOPP materials and branding innovations.