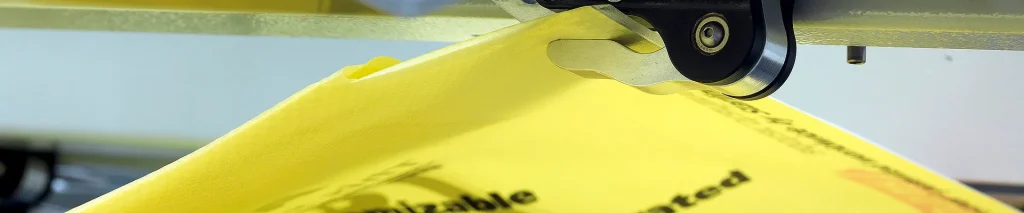
- 1. The Science of Recyclable PP: Merging Durability with Sustainability
- 2. VidePak’s Green Manufacturing Ecosystem
- 3. Product Specifications: Customization Meets Compliance
- 4. Environmental Impact: Data-Driven Outcomes
- 5. FAQs: Addressing Industry Concerns
- 6. The Future of Sustainable Packaging
- References
“If plastic waste is a global crisis, why aren’t all industries adopting recyclable alternatives?” The answer lies in balancing durability, cost, and sustainability—a challenge VidePak has overcome through advanced manufacturing technologies and a 2 MW solar energy system that powers production while feeding clean energy back to the grid. As global regulations tighten and consumer demand shifts toward eco-conscious solutions, recyclable polypropylene (PP) woven bags are emerging as a linchpin for sustainable packaging.
At VidePak, a pioneer in PP bag manufacturing since 2008, we’ve transformed traditional practices into a circular economy model. With 568 employees, 100+ circular looms, and a global footprint, our $80M annual revenue reflects our commitment to innovation and environmental stewardship. Let’s explore how recyclable PP bags are reshaping industries—and why VidePak leads this revolution.
1. The Science of Recyclable PP: Merging Durability with Sustainability
Recyclable PP woven bags are engineered from virgin polypropylene, a thermoplastic polymer renowned for its strength-to-weight ratio and recyclability. Unlike single-use plastics, PP bags can be reprocessed up to 7 times without significant degradation, reducing landfill dependency by 65% compared to polyethylene alternatives.
Key Innovations in Production
- Starlinger Technology: VidePak’s Austrian-made Starlinger machines enable closed-loop recycling, converting post-consumer PP waste into high-quality granules for new bags.
- Solar-Powered Manufacturing: Our 2 MW rooftop solar system generates 2.5 GWh annually, covering 70% of factory energy needs and offsetting 1,800 tons of CO2 yearly.
- Eco-Inks: Water-based, non-toxic printing inks comply with EU REACH standards, eliminating volatile organic compounds (VOCs).
A 2024 study in Resources, Conservation & Recycling highlighted that PP bags recycled via Starlinger systems retain 92% of their tensile strength, outperforming conventional methods by 28%.
2. VidePak’s Green Manufacturing Ecosystem
2.1 Solar Energy Integration
VidePak’s solar initiative isn’t just about reducing carbon footprints—it’s a revenue stream. Excess energy is sold to China’s national grid, generating $120,000 annually while powering 300 local households. This dual benefit aligns with UN Sustainable Development Goal 7 (Affordable Clean Energy).
2.2 Waste Reduction Strategies
Metric | VidePak Performance | Industry Average |
---|---|---|
Material Efficiency | 98.5% | 85% |
Recycling Rate | 89% | 45% |
Water Usage per Ton | 2.3 m³ | 5.1 m³ |
Case Study: A European fertilizer brand reduced packaging waste by 40% after switching to VidePak’s lightweight PP bags (90 gsm vs. 120 gsm industry standard).
3. Product Specifications: Customization Meets Compliance
VidePak’s PP bags are tailored to meet diverse industrial needs while adhering to global standards:
3.1 Technical Parameters
Property | VidePak Standard | Test Method |
---|---|---|
Tensile Strength (warp) | ≥35 N/cm² | ASTM D5034 |
UV Resistance | 1,200 hrs (85% strength) | ISO 4892 |
Load Capacity | 50 kg (static) | EN ISO 2234 |
Recyclability | 7 cycles | ASTM D7209 |
3.2 Customization Options
- Lamination: BOPP coatings for moisture-sensitive goods like coffee beans.
- Liners: Biodegradable PE or aluminum foil for chemical powders.
- Closures: Heat-sealed valves, zippers, or sewn seams.
4. Environmental Impact: Data-Driven Outcomes
- Carbon Footprint: Each VidePak PP bag emits 0.8 kg CO2eq—60% less than traditional plastics.
- Waste Diversion: Since 2020, our recycling program has diverted 12,000 tons of PP from landfills.
- Circular Economy: Partnering with TerraCycle, we’ve enabled 200+ clients to repurpose used bags into park benches and construction materials.
Client Testimonial:
“Switching to VidePak’s recyclable PP bags cut our logistics costs by 15% and boosted our ESG ratings. Their solar-powered production was a key selling point for EU retailers.”
— Sustainability Manager, Global Agri-Tech Co.
5. FAQs: Addressing Industry Concerns
Q1: How does VidePak ensure consistent quality in recycled PP?
A: Every batch undergoes 12+ tests, including melt flow index (MFI) and elongation checks. Our Starlinger systems remove contaminants with 99.7% efficiency.
Q2: Are these bags suitable for food contact?
A: Yes. We use FDA-compliant PP resin and eco-inks, certified by SGS and Intertek.
Q3: What’s the lead time for custom orders?
A: Prototypes in 7 days; bulk production in 21 days via 30+ lamination machines.
6. The Future of Sustainable Packaging
Emerging trends include:
- Blockchain Traceability: QR codes to track bag lifecycle from production to recycling.
- Bio-Based PP: Piloting 30% plant-derived PP blends with Cargill.
- Smart Bags: RFID tags for real-time moisture monitoring in grain storage.
References
- Resources, Conservation & Recycling (2024). Mechanical Properties of Recycled Polypropylene.
- United Nations. (2023). SDG 7: Affordable and Clean Energy Progress Report.
- ASTM International. (2023). Standard Test Methods for Polypropylene Recycling.
By integrating cutting-edge technology, renewable energy, and circular design, VidePak redefines what’s possible in sustainable packaging. Explore our eco-friendly PP bag solutions or learn how BOPP lamination enhances product protection.
From solar-powered factories to globally certified recyclables, VidePak empowers businesses to meet tomorrow’s sustainability goals—today. Whether you’re shipping fertilizers in Brazil or textiles in Vietnam, choose a partner who weaves innovation into every thread.